【徹底解説】亜鉛メッキの種類とその用途とは?
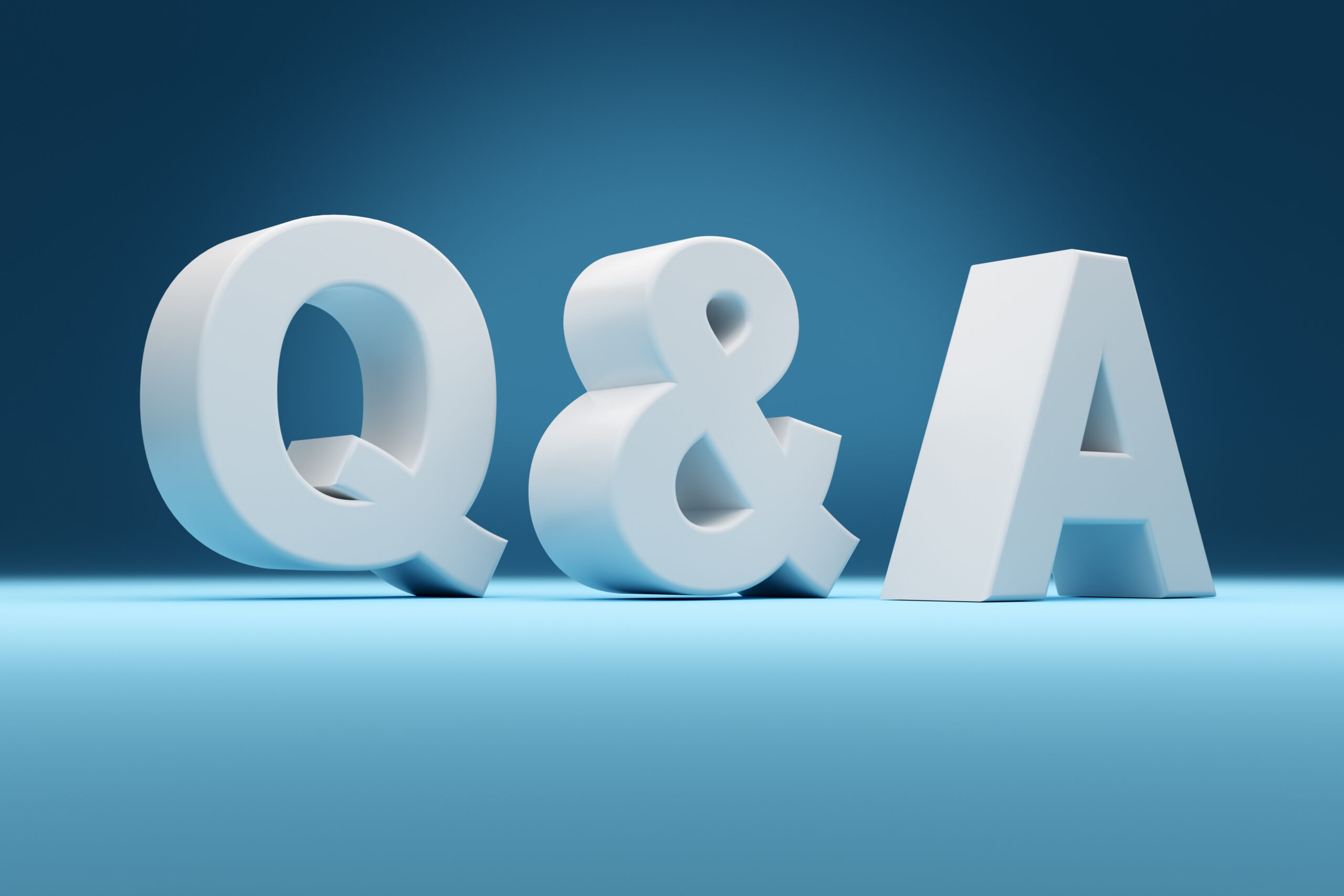
金属の耐久性を高めるための手法として、特に注目を集めているのが特定の加工技術です。これにより、さまざまな環境下でも腐食や劣化から守ることが可能となります。しかし、具体的にどのような種類が存在し、それぞれの用途は何なのか、詳しく知っている人は少ないのではないでしょうか。
この記事では、金属加工の中でも特に重要な技術の種類やその特性、さまざまな業界での利用方法について詳しく解説します。これを読むことで、どの技術がどのようなニーズに応えているのかを理解し、実際の選択肢として考える手助けになるでしょう。
初心者から専門家まで、幅広い読者に向けて、基礎知識から実践的な情報までを網羅した内容をお届けします。金属の加工技術に興味がある方は、ぜひ最後までお付き合いください。
亜鉛メッキの種類とは?それぞれの特徴と用途を徹底解説
亜鉛メッキには大きく分けて、電気亜鉛メッキと溶融亜鉛メッキの2種類があります。電気亜鉛メッキは電気の力を使って亜鉛を素材にメッキする方法で、均一な膜厚が得られるため、機械部品など細かい加工が必要な部品に適しています。一方、溶融亜鉛メッキは高温で溶かした亜鉛に素材を浸す方法で、膜が厚いため耐食性が高く、建築資材や大型構造物に使われます。それぞれの方法は用途に応じて選ばれ、被メッキ物の目的や使用環境に合わせた保護効果を提供します。
代表的な亜鉛メッキの種類とその特徴
代表的な亜鉛メッキには、電気亜鉛メッキと溶融亜鉛メッキがあります。電気亜鉛メッキは、薄くて均一な膜を形成できるため、耐摩耗性や精密部品への適用が可能です。また、溶融亜鉛メッキは膜厚が100μm以上になることが多く、屋外の建材やインフラなど腐食環境での使用に優れています。これらの特徴を活かして、用途に応じた選択が行われます。
用途別に見る亜鉛メッキの選び方
亜鉛メッキの選択は、使用する環境や目的により異なります。例えば、屋内での使用には、薄くて見た目が良く、電気的特性が求められる電気亜鉛メッキが適しています。一方、屋外での耐久性が求められる構造物には、耐食性の高い溶融亜鉛メッキが選ばれることが多いです。また、自動車産業では、衝突時の安全性を考慮して、薄膜で軽量化を図れる電気亜鉛メッキが好まれることもあります。このように、使用用途に応じた適切な亜鉛メッキの選択が、製品の性能や寿命を左右します。
亜鉛メッキとクロメートの違いを理解しよう
亜鉛メッキは、耐食性に優れており、金属の錆びや腐食を防ぐ効果があります。そのため、建築材料や自動車のボディパーツなど、耐久性が求められる製品に使用されています。クロメートメッキは、亜鉛メッキの上にクロムをコーティングする方法です。クロメートメッキは、耐食性に優れているだけでなく、塩害や腐食にも強い特徴があります。
亜鉛メッキとクロメートの基本的な違い
亜鉛メッキは、金属表面に亜鉛をコーティングする技術で、酸化を防ぎ耐食性を向上させます。一方、クロメートメッキは、亜鉛メッキの上にさらにクロム化合物の層を追加し、さらなる耐食性と外観の美しさを提供します。具体的な例として、亜鉛メッキは主に構造用途で見かけますが、クロメートは装飾的な用途や厳しい環境下でも使用されます。
それぞれのメリットとデメリット
亜鉛メッキのメリットとしては、腐食防止効果が高く、コストパフォーマンスが良い点が挙げられます。しかし、酸性環境などでは劣化が早まることもあります。一方、クロメートメッキは、さらに高い耐食性を提供し、外観の美しさや手触りの良さを加えますが、環境規制の対象になることもあります。例として、六価クロメートは一部の用途で制限されていますが、三価クロメートは環境負荷が少ないため人気があります。
亜鉛メッキの加工工程を詳しく解説
亜鉛メッキは、金属の耐食性を高めるために行われる表面処理であり、その工程は非常に多岐にわたります。基本的には、メッキが施される金属表面を清潔にし、適切にメッキ液に浸すことから始まります。具体的には、まず脱脂処理を行い、表面の油脂や汚れを完全に除去します。次に、酸洗処理で酸化皮膜や不純物を取り除き、金属表面を活性化させます。その後、メッキ液に浸すことで、亜鉛メッキコーティングを形成します。このプロセスを経ることで、均一で耐久性の高いメッキ層が得られます。これらの一連の工程は、金属製品の長寿命化と品質向上に寄与しています。
亜鉛メッキの基本的なプロセス
亜鉛メッキの基本的プロセスは、大きく分けて溶融亜鉛メッキと電気亜鉛メッキの2種類があります。溶融亜鉛メッキは、金属を高温の溶融亜鉛槽に浸し、亜鉛の皮膜を形成する手法で、耐食性が高いのが特徴です。一方、電気亜鉛メッキは、電気的な力を用いて亜鉛を金属表面に析出させる方法で、より薄いメッキ層を形成することができます。これらのプロセスを選択する際には、製品の用途や性能要件に応じて最適な方法を選定することが肝要です。
加工工程別の注意点とポイント
亜鉛メッキ加工の際には、各工程における注意点が重要です。例えば、脱脂処理では不完全な油脂除去がメッキ品質の低下を招くため、入念な処理が不可欠です。酸洗工程では、過剰なエッチングを防ぐために適切な酸濃度と処理時間を管理することが求められます。また、メッキ工程では、電流密度やメッキ浴の温度を適切に制御し、均一なメッキ膜厚を実現することがポイントです。これらの注意点を踏まえて施工を行うことで、高品質で耐久性のある亜鉛メッキが施され、製品の信頼性を向上させることができます。
亜鉛メッキの種類別に見る耐久性と防錆効果
亜鉛メッキは、金属表面に亜鉛の皮膜を形成することで、優れた防錆効果を発揮します。ポイントは、亜鉛の皮膜が犠牲的に酸化されることで素材本体を錆から守ることにあります。例として、電気亜鉛メッキと溶融亜鉛メッキの違いがあります。電気亜鉛メッキは薄い皮膜で精密な仕上がりが特徴で、機械部品に多く用いられます。一方、溶融亜鉛メッキは厚い皮膜で耐久性に優れ、屋外構造物に適しています。要点として、目的に応じた亜鉛メッキの選択が重要です。
亜鉛メッキの防錆効果を高めるポイント
亜鉛メッキの防錆効果は、皮膜の厚さや外部条件に大いに依存します。特に、メッキされた部品の管理や使用環境が防錆効果を左右します。たとえば、湿度や温度の管理、及び適切な保管方法が白さびの発生を防ぐ鍵と言えます。具体例として、電気亜鉛メッキ後のクロメート処理は、変色を抑えつつ防錆効果を高めます。最終的に、防錆効果を長期間維持するためには、適切なメンテナンスや環境管理が必要です。
耐久性を左右する要因と選び方
亜鉛メッキ製品の耐久性は、塗料の品質や施工方法に大きく影響されます。耐久性の高い塗料を選ぶことで、長期間の使用に耐えることができます。具体例としては、環境条件や使用目的に適した塗膜構造を選択する必要があります。たとえば、屋外に露出している金属構造物には、より厚いメッキが必要です。最終的には、使用環境や目的に応じた適切な亜鉛メッキの選び方が、その製品の耐久性を大きく左右します。
亜鉛メッキの選び方ガイド:考慮すべきポイントと注意点
亜鉛メッキを選ぶ際には、まず考慮する要点としてコスト、耐食性、見た目が挙げられます。これらの要素は使用する環境や要求される耐用年数、部品の形状や寸法精度によって異なります。例えば、亜鉛メッキは鉄製品の耐久性を高め、美観を保持するために使用されることが多いです。具体的には、鉄製品に薄い亜鉛の層を施すことで腐食を防ぎ、長期間の保護を提供します。このように、目的に応じて最適なメッキ方法を選択することが重要です。
用途に合わせた最適な亜鉛メッキの選び方
亜鉛メッキにはさまざまな種類があり、それぞれ固有の特性と用途があります。用途に応じた最適なメッキ方法を選ぶことで、使用環境に応じた最適な保護を提供することができます。例えば、湿気が多い環境では耐食性を重視したメッキが必要になります。さらに、使用部品の形状や寸法に合わせて選択することで、効率的で効果的な防錆効果を実現できます。これにより、部品の耐用年数を延ばし、長期的なコスト削減につながります。
選択時に注意すべき落とし穴と対策
亜鉛メッキを選択する際に注意すべきは、表面的な条件だけで判断しないことです。例えば、見た目の美しさに惑わされて重要な特性を見落としてしまうことがあります。このような場合、後々の腐食や劣化のリスクが生じる可能性があります。特に、耐食性を求める場合は、その環境に最適な仕様書を基に慎重に選ぶべきです。対策としては、徹底したリサーチを行い、使用環境に適した亜鉛メッキのタイプを選択することが重要です。
まとめ
亜鉛メッキは、金属の防錆効果を高めるための重要な技術です。用途に応じてさまざまな種類が存在し、一般的に熱間メッキや電気メッキ、亜鉛合金メッキなどが用いられます。それぞれのメッキ方法は、耐食性や強度、さらには用途に最適化されており、様々な産業で幅広く利用されています。
これらのメッキは、自動車部品や建築材料、電子機器などに不可欠で、特に耐久性が求められる環境下でその効果を発揮します。適切な亜鉛メッキの選択は、製品の寿命を延ばし、コスト削減にもつながるため、各種の特徴や用途を理解し、目的に合った選択をすることが重要です。