ブランク加工の種類とその特性を理解しよう
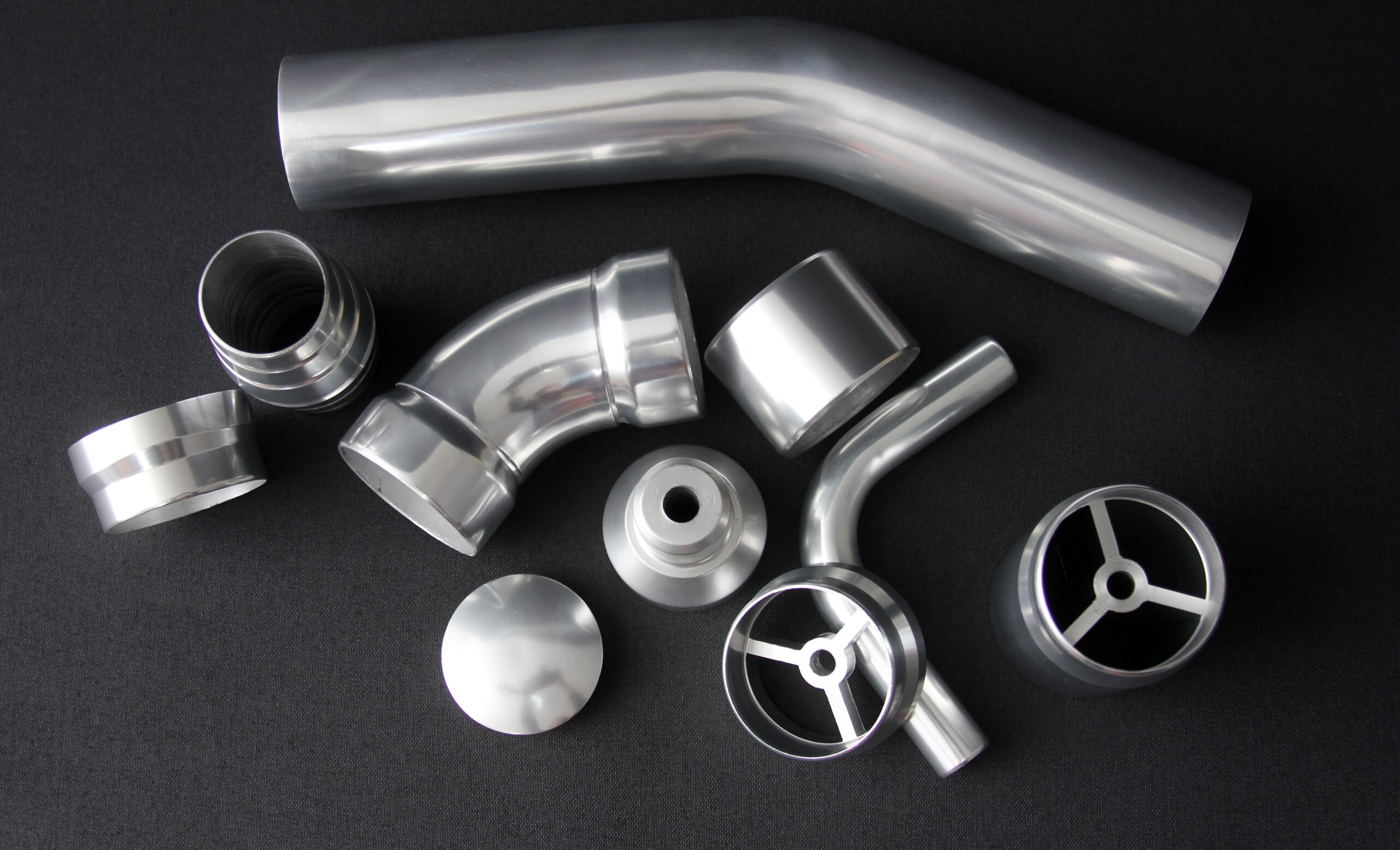
製造業や技術の進化に伴い、様々な加工方法が生まれています。その中でも、特に注目されているのが、特定の形状やサイズに材料を整える技術です。しかし、どのような種類があり、それぞれの特性は何なのでしょうか?
この記事では、これらの加工方法について詳しく解説し、それぞれの利点や適用場面を紹介します。初めてこの分野に触れる方から、さらなる知識を深めたい方まで、幅広く役立つ情報を提供します。
もし、製造プロセスの効率化や製品の品質向上に興味があるなら、この内容はあなたにとって必見です。それぞれの加工方法を理解することで、あなたのプロジェクトに最適な選択をする手助けになるでしょう。さあ、さっそくその魅力を探ってみましょう!
ブランク加工の基本プロセスとその利点
ブランク加工は、金属板やシートから必要な形状の部品を切り出すプロセスです。この方法には「スタンピング」、「プレス加工」、「レーザー切断」などが含まれ、主に製品の基礎部品を作るために使用されます。効率が高く大量生産に適しているため、コスト削減に寄与します。例えば、自動車部品の製造において、トヨタの生産ラインではブランク加工が広く用いられています。結果として、生産速度が向上し、品質のばらつきを減少させることができます。
ブランク加工とは?基本から理解する
ブランク加工とは、プレス加工における基礎的な加工方法で、「抜き加工」とも呼ばれます。このプロセスでは、金属板やその他の材料を特定の形状に切り出します。主に部品の初期形状を作成するために用いられ、最終製品の寸法精度や表面品質を左右します。例えば、航空機や家電製品の製造において、ブランク加工は重要な役割を果たします。具体的には、製品の精密性と表面の均一性を確保するために、精密な金型が使用されます。
ブランク加工の利点とは?効果的な活用法
ブランク加工のメリットは、複数の加工工程を一台の機械で行えるため非常に効果的であることです。これにより、加工の効率性が向上し、生産コストの削減につながります。高い生産性を発揮し、精度の高い加工が可能になるため、製品の品質が安定します。例えば、自動車産業では、一度に大量の部品を加工できるため生産スピードが速く、工程の効率化が図られます。これにより、企業は市場の需要に迅速に対応できるようになります。
ブランク加工に必要な金型の種類と選び方
ブランク加工は、プレス加工の基本であり、主にプレス金型を使用して製品を製作していきます。ブランク加工に必要な金型には、単発型、順送型、トランスファー型などがあります。選択する金型は、使用する材料の特性や生産量、製品の機能性に応じて決定することが重要です。例えば、単発型は低コストでの試作や小ロット生産に適しており、順送型は効率的な大量生産を可能にします。従って、適切な金型を選ぶことで、生産コストを抑えつつ高品質な製品を生産することができます。
金型の基本とブランク加工での役割
金型は、金属板を加工するための型として使用され、ブランク加工の精度を確保するために不可欠です。ブランク加工では、金型が正確な寸法を決定し、複数の部品を一度に加工することが可能になります。これにより、生産性の向上と安定した品質を実現できるのが特徴です。具体的には、プレス機を用いて金属板を金型に当て、圧力を加えることで部品が成形されます。これにより、必要な形状のパーツを一括で製造できるため、高い生産性と安定した品質が実現できます。
ブランク加工に最適な金型の選び方
ブランク加工における最適な金型の選び方は、製品の仕様、生産量、使用する材料の特性に基づいて行われます。例えば、直線的な切断を行う場合には単発型が適しており、複雑な形状を持つ製品には順送型が効果的です。また、材料の無駄を最小限に抑えられる金型設計を工夫し、材料の歩留まりを向上させることが可能です。これにより、コストの削減や生産効率を高めることができます。さらに、金型の素材や硬度、寿命も選定の重要な要素となります。
ブランク加工と他の加工方法との違い
要点として、ブランク加工とは金属板やその他の材料を所定の形状に切り出す加工方法であり、主に部品の初期形状を作るために使用されます。理由として、ブランク加工は金属を自在に形作るために必要な初期段階の加工であり、部品の最終形状に至る初めのステップとして非常に重要です。具体例として、金属板材料を使用して製品の輪郭や穴を切断する工程があり、これをまとめて「ブランク加工」や「抜き加工」と呼びます。要点として、ブランク加工は製造プロセスにおける初期段階の役割を果たします。
ブランク加工と切削加工の違いを比較
要点として、ブランク加工と切削加工は目的やプロセスが異なり、選択の基準が異なります。理由として、ブランク加工は一度に大量の部品を一括して抜き加工することで高い生産性を実現する一方、切削加工は刃物を用いて材料を削るため細かい形状の成形に適しています。具体例として、ブランク加工が迅速な大量生産に向く一方、切削加工は高精度を要求される場面で選ばれることがあります。要点として、加工目的や精度要求に応じて、効率の良い加工方法を選ぶことが重要です。
ブランク加工が優れている点とその理由
要点として、ブランク加工の主な利点は生産性の高さにあります。理由として、一度に大量の部品を加工できるため、生産スピードが速くコスト削減にもつながります。具体例として、精密な加工を行う際にも高精度が求められ、NC制御による加工が可能で安定した高品質な製品が得られます。要点として、ブランク加工はコストと生産性を重視する製造において非常に効果的な方法であると言えます。
ブランク加工導入時のコストと効率性
ブランク加工を導入する際には、コスト削減と効率性の向上を期待できることが多いです。理由として、新しい技術の導入による自動化が挙げられます。これにより、製品の品質を一貫して保ちながら、人件費を削減し、生産効率を高めることが可能です。具体例として、製造プロセスでのマシニングセンターやシステム導入により、属人的であった情報の共有化が進み、より効率的な業務運営が実現します。結果として、コスト削減と効率性の向上が両立可能です。
ブランク加工のコストに関する基本知識
ブランク加工のコストは、使用する設備や材料、加工の精度に大きく依存します。コスト削減のためには、適切な金型を用いることが重要です。例えば、タレパン加工は適切な機械設備を使用することで、コストを抑えられます。また、材料コストも重要で、必要な性能を満たしつつ、最適な材料を選定することが求められます。結果として、加工効率を向上させつつコストを抑えることが可能です。
効率的なブランク加工の実践法
効率的なブランク加工の実践には、高精度なレーザーカッティングや自動化設備の導入が鍵となります。これらの技術を用いることで、複雑な形状でもスムーズに加工することができ、時間とコストの削減につながります。例えば、レーザーを使用することで、細かい形状や複雑なデザインでも高い精度で切断が可能です。これにより、プロジェクトの柔軟性と迅速な調整が可能となり、効率性の向上が実現します。
ブランク加工における一般的な問題点と対策
ブランク加工は金属板を特定の形状に切り出すプロセスで、多くのメリットがある一方、様々な問題点も抱えています。要点として、例えば、切断時に発生するバリや変形があります。これに対する理由は、切れ刃の摩耗や不適切な切込み設定などが含まれます。具体例として、バリを減少させるためには、クリアランスを適切に調整したり、パンチ・ダイの再研磨を行うことが挙げられます。これにより部品の精度を向上させることができ、全体の生産性も向上します。
よくある問題点とその原因
ブランク加工における一般的な問題点として、不良品の発生や加工コストの増加があります。これらの問題は、金型が不適切に設計されている場合や、工具の摩耗、適切ではない切削パラメータが原因となります。具体例として、切り込みが大きすぎると、高い切削力と温度負荷が発生し、工具の摩耗や振動を引き起こす可能性があります。要点として、これらの問題を未然に防ぐためには、定期的な金型のメンテナンスと適切な切削条件の設定が不可欠です。
ブランク加工のトラブルシューティング方法
ブランク加工のトラブルシューティングでは、まず工具の点検を行い、摩耗や損傷がないかを確認します。次に、加工条件を見直し、速度や送り量を適切に調整し、切削油の供給を最適化します。具体例として、しわや破れを防ぐためには、曲げ半径を大きくする方法を採用することがあります。これらの対策により、製品の品質向上とトラブルの軽減が図られます。要点として、定期的な設備メンテナンスと作業者の熟練度向上が重要です。
まとめ
ブランク加工は、金属や材料を特定の形状に形成するための重要な技術です。様々な種類があり、それぞれに独自の特性があります。例えば、プレス加工や切削加工、鍛造加工などがあり、それぞれの方法は目的や求める精度によって使い分けられます。
加工の選択は、製品の品質やコストに大きな影響を与えるため、適切な技術を選ぶことが重要です。ブランク加工を理解することで、製造工程における効率や製品の性能を向上させる手助けとなるでしょう。