スポット溶接とは? 特徴とメリットを解説
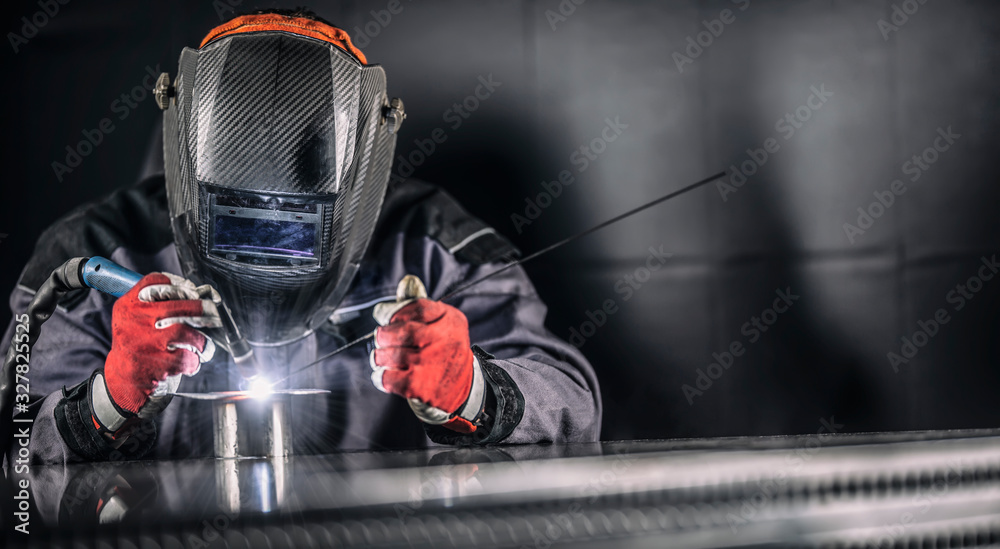
スポット溶接は、2枚以上の金属板を重ね合わせて、電極を通して電流を流すことで接合する溶接方法です。溶接箇所を局所的に加熱し、溶融させて接合します。自動車のボディや家電製品など、様々な分野で広く使用されています。
本記事では、スポット溶接の基本から特性、利点、欠点、他の溶接方法との比較まで、詳しく解説します。スポット溶接について理解を深め、適切な溶接方法を選択する参考にしてください。
スポット溶接の基本とは?
スポット溶接は、2枚の金属板を重ねて電極で挟み、電流を流して接合させる抵抗溶接の一種です。電極と板の接触部位が高温になり、溶融または塑性変形を起こして接合されます。
スポット溶接は、局部的な溶接が可能で熱影響が小さく歪みが少ない、自動化が容易で大量生産に適している、薄板の接合に適しているなどの特長があります。このため、自動車の車体や部品組み立て、家電製品の製造、各種金属製品の接合など、様々な産業分野で広く使用されています。
スポット溶接には、以下のような特性があります。
- 電極と板のみに電流を集中できるため、局部的な溶接が可能
- 大電流・短時間で行われるため熱影響が小さく歪みが少ない
- 自動化が容易で大量生産に適している
- 薄板の接合に適している一方で、厚板には不向き
スポット溶接では、様々な種類の材料を使用することができます。一般的な材料としては、鋼板、ステンレス鋼、アルミニウム、銅などが挙げられます。
スポット溶接の利点としては、以下のような点が挙げられます。
- 高速で接合できる
- 歪みが少ない
- 自動化が容易
- 薄板の接合に適している
一方、スポット溶接には以下のような欠点も存在します。
- 厚板の接合には不向き
- 接合強度が低い場合がある
- 表面処理の影響を受けやすい
スポット溶接は、様々な産業分野で広く使用されている接合技術です。しかし、スポット溶接にはメリットだけでなくデメリットも存在するため、使用する際にはそれぞれの特性を考慮する必要があります。
スポット溶接の特性
スポット溶接には、他の溶接方法と比較して、多くの利点があります。
- 高速で連続的に溶接できる
- 溶接部の変形が少ない
- 薄板の溶接に適している
- 溶接部に熱影響部が発生しにくい
- 自動化しやすい
- 低コストで溶接できる
これらの利点により、スポット溶接は様々な分野で広く使用されています。特に、自動車、家電製品、電子機器など、薄板の接合が必要な分野で多く用いられています。
スポット溶接で使用される材料の種類
スポット溶接は、さまざまな金属材料を接合するために使用できる汎用性の高い溶接方法です。 しかし、すべての金属がスポット溶接に適しているわけではありません。 スポット溶接に適した金属の一般的な特性を以下に示します。
- 電気伝導率が高い
- 熱伝導率が低い
- 融点が低い
- 延性がある
これらの特性を備えた金属は、スポット溶接時に必要な熱と圧力を発生させ、確実に接合することができます。 以下に、スポット溶接に適した金属の例をいくつか示します。
- 低炭素鋼
- ステンレス鋼
- アルミニウム
- 銅
- ニッケル
これらの金属は、スポット溶接に適していますが、スポット溶接に適さない金属もいくつかあります。 以下に、スポット溶接に適さない金属の例をいくつか示します。
- 高炭素鋼
- 鋳鉄
- マグネシウム
- チタン
これらの金属は、スポット溶接に適していません。 その理由は、これらの金属は電気伝導率が低く、熱伝導率が高いため、スポット溶接時に必要な熱と圧力を発生させることができないためです。 また、これらの金属は延性がないため、スポット溶接時にひび割れが発生する可能性があります。
スポット溶接に使用する材料の種類は、接合する材料の種類によって異なります。 たとえば、低炭素鋼をスポット溶接する場合は、低炭素鋼用のスポット溶接機を使用する必要があります。 ステンレス鋼をスポット溶接する場合は、ステンレス鋼用のスポット溶接機を使用する必要があります。 適切なスポット溶接機を使用しないと、適切な接合ができない可能性があります。
スポット溶接の利点
スポット溶接は、電極を通じて電流を流すことで金属板を重ね合わせる抵抗溶接の一種です。溶接される金属の抵抗によって熱が発生し、溶融状態になります。電流を遮断すると、溶けた金属が冷却して固化し、金属板が接合されます。
スポット溶接には、高速で効率的、正確性、自動化、省スペース、環境に優しい、低コストなど、さまざまな利点があります。
- 高速で効率的 – スポット溶接は、1秒間に数個のスポットを溶接することができ、大量生産に適しています。
- 正確性 – スポット溶接は、正確な位置に溶接することができ、精密な製品の製造に適しています。
- 自動化 – スポット溶接は、ロボットや自動化装置を用いて自動化することができ、人件費を削減することができます。
- 省スペース – スポット溶接機は、他の溶接機と比較して小型で、省スペースで設置することができます。
- 環境に優しい – スポット溶接は、溶接時にガスや煙が発生しないため、環境に優しい溶接方法です。
- 低コスト – スポット溶接は、設備投資やランニングコストが比較的低いため、経済的な溶接方法です。
これらの利点により、スポット溶接は、自動車、家電、航空機などのさまざまな産業分野で広く用いられています。
スポット溶接の欠点とは?
スポット溶接の欠点とは?
スポット溶接は多くの利点を持つ一方で、いくつかの欠点も存在します。主な欠点としては、強度が低いこと、板厚が厚いものには適さないこと、接合部の外観が劣ること、自動化が難しいことの4点が挙げられます。
スポット溶接は連続した溶接線ではなく、点状の溶接によって接合するため、連続溶接に比べて強度が低くなります。一般的に板厚3mm程度までの薄い金属板に適しており、それ以上の厚い金属板には強度不足となるため、他の溶接方法が推奨されます。
また、スポット溶接は溶接痕が目立つため、外観を重視する製品には適していません。さらに、スポット溶接は熟練した作業者による手作業で行われることが多く、自動化が難しいという欠点があります。
これらの欠点を考慮した上で、スポット溶接が適した用途かどうかを判断する必要があります。
スポット溶接 メリット
スポット溶接は、薄い金属板を接合するのに最適な抵抗溶接の一種です。 2枚の金属板を重ね合わせ、電極を通して電流を流すことで接合します。 電流は金属板を局所的に溶かし、接合部を形成します。 スポット溶接には多くのメリットがあり、それが幅広い用途で使用される理由となっています。
スポット溶接の主なメリットは次のとおりです。
- 高速性: スポット溶接は非常に高速なプロセスであり、他の種類の溶接よりもはるかに高速に接合を行うことができます。
- 効率性: スポット溶接は自動化が容易なため、他の種類の溶接よりもはるかに効率的です。
- 汎用性: スポット溶接は、さまざまな種類の金属および厚さに使用できます。
- 強度: スポット溶接は、他の種類の溶接と同等かそれ以上の強度を持つ接合部を作成できます。
- 低コスト: スポット溶接は、他の種類の溶接よりも低コストの機器を使用できます。
- クリーン: スポット溶接は、他の種類の溶接と比較して煙やスパッタが発生しません。
- 正確性: スポット溶接は、他の種類の溶接よりも正確に制御できます。
- 信頼性: スポット溶接は、信頼性の高い接合部を作成できます。
これらの利点に加えて、スポット溶接は、複雑な形状の接合にも適しています。 また、表面仕上げに影響を与えないため、塗装やメッキなどの仕上げが必要な場合に最適です。
スポット溶接は、以下のような幅広い用途で使用されています。
- 自動車産業
- 航空宇宙産業
- 家電業界
- 建設業界
- 医療機器業界
スポット溶接は、さまざまな利点を備えた汎用性の高い溶接プロセスです。 強度、速度、効率、および低コストに接合が必要なアプリケーションに最適です。
スポット溶接と他の溶接方法の比較
スポット溶接は、他の溶接方法と比較して、多くの利点があります。たとえば、スポット溶接は高速で効率的なプロセスであり、自動化が容易です。また、スポット溶接は他の溶接方法よりもエネルギー消費量が少ないため、環境に優しい選択肢となります。
スポット溶接の主な違いは、そのプロセスと用途にあります。プロジェクション溶接は、スポット溶接に似ていますが、より大きな溶接強度が得られます。これは、金属板に小さな突起を形成し、その突起を溶接によって接合することで実現されます。シーム溶接は、連続したスポット溶接を使用して、より長い溶接線を作成するプロセスです。これは、気密性が必要な用途に適しています。
レーザー溶接は、レーザービームを使用して金属を溶接するプロセスです。これは、スポット溶接よりも高速で正確なプロセスですが、より高価な設備が必要です。アーク溶接は、電極とワークピースの間にアークを発生させることで金属を溶接するプロセスです。これは、スポット溶接よりも汎用性の高いプロセスですが、より多くのスキルが必要です。
上記のように、スポット溶接は、用途に応じて選択できる幅広い利点と機能を提供します。詳細については、個々の溶接方法に関する他の見出しをご覧ください。
スポット溶接とプロジェクション溶接の相違
スポット溶接とプロジェクション溶接はどちらも抵抗溶接の一種ですが、電極形状と用途が異なります。
電極形状
スポット溶接では、平らな電極を使用します。一方、プロジェクション溶接では、突起状の電極を使用します。この突起は、溶接したい箇所に投影され、溶接の強度を高めます。
用途
スポット溶接は、薄板の接合に適しています。一方、プロジェクション溶接は、厚板の接合や、強度が必要な箇所の接合に適しています。
その他の違い
- プロジェクション溶接は、スポット溶接よりも電流密度が高いため、より高速で溶接できます。
- プロジェクション溶接は、スポット溶接よりも熱影響部が小さいため、歪みが少ないです。
- プロジェクション溶接は、スポット溶接よりもコストがかかります。
スポット溶接とプロジェクション溶接はどちらも用途に応じて使い分ける必要があります。薄板の接合にはスポット溶接が、厚板の接合や強度が必要な箇所の接合にはプロジェクション溶接が適しています。
スポット溶接とシーム溶接の違いとは?
スポット溶接とシーム溶接は、どちらも抵抗溶接の一種ですが、いくつかの重要な違いがあります。
スポット溶接は、2枚の金属板を重ね合わせ、電極を通して電流を流すことで、接合部を溶融させる方法です。電極は、溶接したい箇所に押し当てられ、電流が流れることで接合部が加熱され、溶融します。その後、電流を停止し、電極で接合部を冷却することで、溶接が完了します。
スポット溶接は、自動車の車体や家電製品の製造など、さまざまな用途で使用されています。
シーム溶接は、スポット溶接と同様に電極を通して電流を流して金属板を溶融させる方法ですが、スポット溶接とは異なり、連続的に溶接を行うことで、連続した溶接線を作成します。シーム溶接は、缶詰やパイプなどの製造に使用されています。
スポット溶接とシーム溶接の主な違いは、以下のとおりです。
- スポット溶接は、複数の離れた点で溶接を行うのに対し、シーム溶接は連続的に溶接を行います。
- スポット溶接は、電極の形状が円形であるのに対し、シーム溶接は、電極の形状が円筒形または円錐形です。
- スポット溶接は、自動車の車体や家電製品の製造など、さまざまな用途で使用されていますが、シーム溶接は、缶詰やパイプなどの製造に使用されています。
スポット溶接とシーム溶接は、どちらも抵抗溶接の一種ですが、いくつかの重要な違いがあります。スポット溶接は、複数の離れた点で溶接を行うのに対し、シーム溶接は連続的に溶接を行います。スポット溶接は、電極の形状が円形であるのに対し、シーム溶接は、電極の形状が円筒形または円錐形です。スポット溶接は、自動車の車体や家電製品の製造など、さまざまな用途で使用されていますが、シーム溶接は、缶詰やパイプなどの製造に使用されています。
スポット溶接とレーザー溶接の相違
スポット溶接とレーザー溶接は、どちらも接合部を生成するために熱を使用する接合プロセスですが、いくつかの重要な違いがあります。
-
熱源: スポット溶接では、電気抵抗を使用して2つの金属片の間に熱を生成します。レーザー溶接では、集束レーザービームを使用して熱を生成します。
-
プロセス: スポット溶接では、電極を使用して金属片を一緒に保持し、電流を流して接合部を形成します。レーザー溶接では、レーザービームを使用して金属片を溶融し、接合部を形成します。
-
用途: スポット溶接は、一般的に薄い金属板の接合に使用されます。レーザー溶接は、厚い金属板や異なる種類の金属の接合に使用できます。
-
利点: スポット溶接は、比較的安価で高速なプロセスです。レーザー溶接は、より正確で、強度の高い接合部を生成できます。
-
欠点: スポット溶接は、レーザー溶接よりも柔軟性が低く、複雑な形状の接合部を形成することはできません。
一般的に、レーザー溶接はスポット溶接よりも用途が広く、高品質ですが、より高価なプロセスです。
スポット溶接とアーク溶接の相違
スポット溶接とアーク溶接はどちらも広く使用されている溶接方法ですが、その原理と適用範囲は大きく異なります。
アーク溶接は、電極と母材の間にアークを発生させ、その熱を利用して金属を溶融させて接合する方法です。アーク溶接はさまざまな種類の金属を接合することができ、溶接部も比較的強固になります。しかし、アーク溶接は熱影響部が大きく、歪みが発生しやすいという欠点があります。
スポット溶接は、電極を通して母材に電流を流すことで接合部を局所的に加熱し、溶融させて接合する方法です。スポット溶接は、薄板の接合に適しており、高速で連続的に接合することが可能です。また、熱影響部が小さく、歪みが発生しにくいという利点があります。
しかし、スポット溶接は接合できる金属の種類が限られ、溶接部の強度もアーク溶接に比べて劣ります。
以下に、スポット溶接とアーク溶接の主な違いを比較した表を示します。
特徴 | スポット溶接 | アーク溶接 |
---|---|---|
適用範囲 | 薄板の接合 | さまざまな種類の金属の接合 |
接合速度 | 高速 | 比較的遅い |
熱影響部 | 小さい | 大きい |
歪み | 発生しにくい | 発生しやすい |
溶接部の強度 | 比較的弱い | 比較的強い |
接合できる金属の種類 | 限られている | さまざまな種類を接合できる |
用途に応じて、適切な溶接方法を選択することが重要です。
抵抗スポット溶接の特徴
抵抗スポット溶接は、2枚の金属板を重ね合わせて、電極を押し当て、電流を流すことで接合させる溶接方法です。接合部分は電流によって抵抗熱が発生し、溶融することで接合されます。
抵抗スポット溶接のメリットは、高速で接合できる、自動化しやすい、低コストで接合できる、溶接部の強度が高い、歪みが少ないです。デメリットは、接合できる板厚が限られている、異なる種類の金属を接合できない、溶接部の表面に跡が残る、複雑な形状の接合には不向きです。
抵抗スポット溶接の仕様は、電流、電圧、時間、圧力、電極形状によって決まります。これらの要素を調整することで、溶接部の強度や外観を調整することができます。
抵抗スポット溶接は、自動車ボディの接合、家電製品の接合、鋼製家具の接合、缶の封止など、様々な産業分野で使用されています。
抵抗スポット溶接は、他の溶接方法と比較して、高速で接合できる、自動化しやすい、低コストで接合できる、溶接部の強度が高い、歪みが少ないという特徴があります。しかし、接合できる板厚が限られている、異なる種類の金属を接合できない、溶接部の表面に跡が残る、複雑な形状の接合には不向きというデメリットもあります。
抵抗スポット溶接は、様々な産業分野で使用されており、今後も需要が高まっていくことが予想されます。
スポット溶接の打点数と距離について
スポット溶接の打点数と距離は、溶接の強度と品質に大きな影響を与えます。打点数は、溶接する箇所の面積に応じて設定され、距離は溶接する材料の厚さや種類によって異なります。
打点数が少なすぎると、溶接強度が低下し、剥がれやすくなります。逆に多すぎると、熱影響が大きくなり、材料が変形したり、強度が低下する恐れがあります。
距離は、溶接する材料の厚さや種類によって異なります。厚さが薄い材料や熱伝導率の高い材料は、熱が伝わりやすいので、距離を短くする必要があります。逆に、厚さが厚い材料や熱伝導率の低い材料は、距離を長くする必要があります。
打点数と距離は、溶接条件によって適宜調整する必要があります。適切な打点数と距離を設定することで、高品質のスポット溶接を実現することができます。
以下は、スポット溶接の打点数と距離に関する具体的な例です。
- 1mm以下の薄い鋼板をスポット溶接する場合、打点数は1cmあたり3~4点程度、距離は1~2mm程度が適切です。
- 2mm以上の厚い鋼板をスポット溶接する場合、打点数は1cmあたり2~3点程度、距離は2~3mm程度が適切です。
- アルミニウムなどの非鉄金属をスポット溶接する場合、熱伝導率が大きいため、打点数は1cmあたり4~5点程度、距離は1mm程度が適切です。
なお、これらの値はあくまで目安であり、実際の溶接条件は材料や溶接機によって異なります。適切な打点数と距離は、試験によって確認する必要があります。
溶接ナゲットについて
溶接ナゲットとは、スポット溶接で接合された2枚の金属板が溶融して固まった部分のことです。ナゲットの大きさは、溶接電流、溶接時間、電極圧力などの溶接条件によって決まり、接合強度に影響を与える重要な要素です。
溶接ナゲットの断面を観察すると、中心部が溶融して再結晶した結晶粒が細かく、周辺部は熱影響を受けた粗い結晶粒となっていることがわかります。また、ナゲットの表面には、溶融金属が冷却固化するときに生じる凝固組織が見られます。
溶接ナゲットの大きさは、溶接条件を調整することで制御することができます。溶接電流を大きくしたり、溶接時間を長くしたりすると、ナゲットは大きくなります。しかし、ナゲットが大きすぎると、接合部の強度が低下したり、溶接部にクラックが発生したりする可能性があります。
溶接ナゲットの品質は、接合強度に影響を与える重要な要素です。ナゲットが小さすぎたり、欠陥があったりすると、接合部の強度が低下します。そのため、溶接ナゲットの大きさと品質を適切に管理することが、スポット溶接の重要なポイントとなります。
溶接方法の比較
溶接は、金属や熱可塑性樹脂などの材料を接合するのに用いられる製造プロセスです。さまざまな溶接方法がありますが、最も一般的なものはアーク溶接、レーザー溶接、スポット溶接です。
各溶接方法にはそれぞれ独自の特性と利点があります。アーク溶接は、電極と母材との間にアークを発生させて熱を生み出し、材料を溶融させて接合する最も汎用性の高い方法です。レーザー溶接は、レーザービームを使用して材料を溶融させる高精度の方法です。スポット溶接は、2つの金属板を重ね合わせ、電極を通じて電流を流すことで接合する抵抗溶接の一種です。
これらの溶接方法の詳細については、以下の記事をご覧ください。
- アーク溶接の特徴
- レーザー溶接の特性
アーク溶接の特徴
アーク溶接は最も一般的な溶接方法の一つであり、金属を熱で溶かし、溶けた金属同士を接合する技術です。溶接箇所を加熱するために、電極と母材との間にアーク放電を利用します。
アーク溶接には、手動アーク溶接、TIG溶接、MIG溶接など、さまざまな種類があります。
アーク溶接は、薄板から厚板まで、さまざまな厚さの金属を溶接でき、さまざまな材料の溶接にも適しています。
アーク溶接の利点は、汎用性が高く、操作が簡単で、比較的低コストであることです。欠点は、溶接速度が遅く、熱歪みが発生しやすい、熟練した技術が必要であることです。
アーク溶接は、製造業、建設業、造船業、自動車産業など、さまざまな業界で使用されています。信頼性の高い、汎用性の高い溶接方法です。
レーザー溶接の特性
レーザー溶接は、スポット溶接と同様に接合部に局所的な熱を加えて接合を行う溶接方式ですが、熱源にレーザー光を使用する点が大きく異なります。レーザー光の持つ以下の特性により、スポット溶接とは異なる利点や特徴を持っています。
- 高エネルギー密度: レーザー光は非常に高いエネルギー密度を持つため、極めて狭い範囲に熱を集中させることができます。これにより、母材への熱影響を最小限に抑え、精密な溶接が可能となります。
- 高速: レーザー溶接は非常に高速で行うことができます。これは、レーザー光が熱伝導による熱の拡散がほとんどなく、瞬時に溶融させることができるためです。
- 非接触: レーザー溶接は非接触で溶接を行うことができるため、ワークへの汚染や損傷の心配がありません。また、溶接部の形状に柔軟に対応することができます。
- 自動化: レーザー溶接は自動化が容易で、安定した品質の溶接が可能です。
これらの特性により、レーザー溶接は以下のような利点があります。
- 高精度: 高いエネルギー密度と高速性により、精密な溶接が可能となり、非常に細い溶接や複雑な形状の溶接にも対応できます。
- 低歪み: 母材への熱影響が小さいことから、歪みが発生しにくく、高品質の仕上がりを実現できます。
- 高速性: 高速で溶接が行えるため、生産性の向上に貢献できます。
- 自動化: 自動化が容易なため、人手不足への対応や品質の安定化に有効です。
一方、レーザー溶接は以下の点にも注意が必要です。
- コスト: レーザー加工機などの設備投資が必要なため、初期コストが高くなります。
- 材質: すべての金属に適しているわけではなく、材質によってはレーザー溶接ができない場合があります。
- 安全性: レーザー光は危険なため、安全対策を徹底する必要があります。
このように、レーザー溶接は高精度、低歪み、高速性などの利点がありますが、コストや材質、安全性の点にも注意が必要です。スポット溶接と比較しながら、最適な溶接方式を選択することが重要となります。
スポット溶接のまとめ
スポット溶接は、重ね合わせた金属板を電極で挟み、電流を流して局部的に溶融・接合させる抵抗溶接の一種です。自動車の車体や家電製品の組み立てなど、幅広い分野で活用されています。
スポット溶接の主な特徴は、以下のとおりです。
- 高効率: 短時間で溶接できるため、大量生産に適しています。
- 高品質: 溶接部の強度が高く、外観もきれいです。
- 自動化しやすい: ロボットによる自動化が容易で、安定した品質を確保できます。
- 環境に優しい: 溶接時に煙やスパッタが発生しにくく、環境負荷が小さいです。
スポット溶接のメリットは、以下のとおりです。
- 高効率で低コスト: 短時間で溶接できるため、生産効率が向上し、コスト削減に貢献します。
- 高品質: 溶接部の強度が高く、外観もきれいです。
- 自動化しやすい: ロボットによる自動化が容易で、安定した品質を確保できます。
- 環境に優しい: 溶接時に煙やスパッタが発生しにくく、環境負荷が小さいです。
スポット溶接のデメリットは、以下のとおりです。
- 溶接できる板厚に制限がある: 一般的に、板厚3mm程度までしか溶接できません。
- 溶接部に凹凸ができる: 電極の形状によって、溶接部に凹凸ができてしまうことがあります。
- 表面処理に影響が出る: 溶接部に熱が入るため、表面処理が剥がれてしまうことがあります。
スポット溶接は、さまざまなメリットを持つ優れた溶接方法ですが、デメリットも存在します。溶接する材料や用途に合わせて、適切な溶接方法を選択することが重要です。