【徹底解説】樹脂成型の種類とそれぞれの特徴
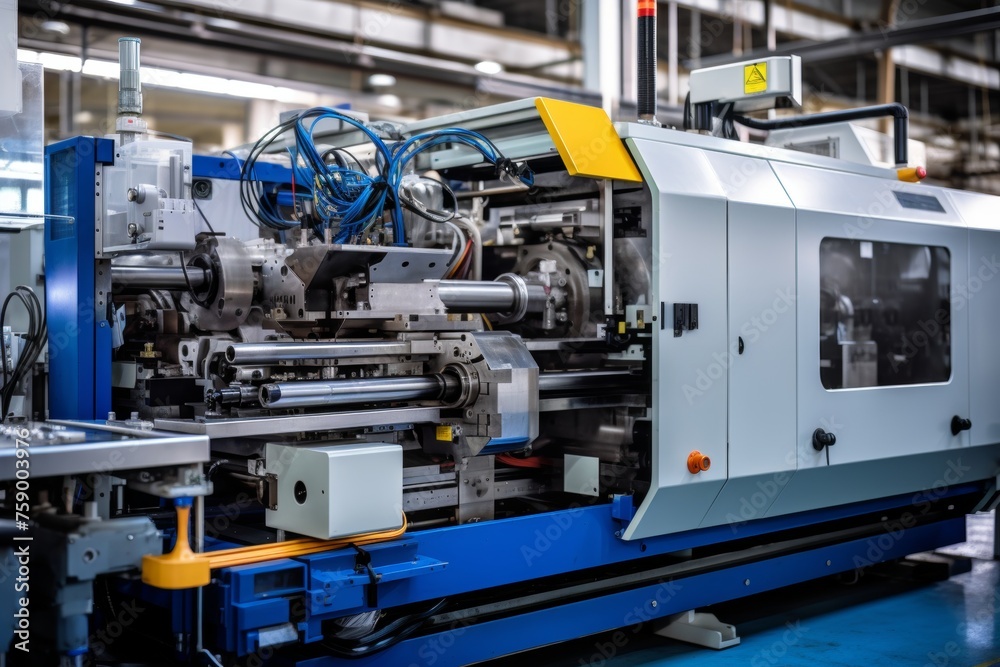
樹脂成型の世界に足を踏み入れると、さまざまな技術や方法が存在し、どれも独自の魅力を持っています。もし「どの成型方法が自分のプロジェクトに最適なのか」と悩んでいる方がいれば、この記事はまさにその疑問に応えるためにあります。
樹脂成型は、さまざまな産業において重要な役割を果たしていますが、それぞれの成型技術には異なる特性や利点があります。「この技術の違いは何か」「どの方法を選ぶべきか」といった疑問を持つ方に、詳しく解説していきます。
この記事では、樹脂成型の主要な種類やそれぞれの特徴、さらには選び方のポイントまでを網羅的に紹介します。これを通じて、あなたのプロジェクトに最適な成型方法を見つける手助けができれば幸いです。
樹脂成形の基本を学ぼう
樹脂成形とは?その基本概念を解説
要点として、樹脂成形の基本概念は、樹脂(プラスチック)を加熱して溶かし、金型を使って所定の形にし冷やして固めることで製品を作る方法です。理由として、樹脂は加熱することで容易に形を変えられる特性を持つため、複雑な形状の製品の大量生産が可能になります。具体例として、射出成形という方法があります。これは加熱した樹脂を金型に注入し、冷却して製品を作る技術で、自動車部品や日用品など非常に多岐にわたる製品の製造に使われています。要点としてまとめると、樹脂成形はその加工の柔軟性と効率性から、現代社会で不可欠な製造技術となっています。
樹脂成形が重要な理由とは?
要点として、樹脂成形は大規模かつ高精度な製品を低コストで生産できるため、非常に重要な技術です。理由として、この成形法は材料の多様性や軽量化、耐久性、耐熱性に優れているため、自動車、家電、医薬品など幅広い分野で利用されています。具体例としては、自動車のパーツや家庭用電化製品のケースといった、日常生活に欠かせない製品が挙げられます。これらは高精度で大量生産する必要があるため、樹脂成形の効率性が活かされています。要点として、樹脂成形はその精度とコスト効率の良さから、様々な産業において不可欠な技術として重要視されています。
主な樹脂成形法とその特徴
樹脂成形は、さまざまな製品の生産に不可欠な技術です。まず、射出成形は複雑な形状の製品を大量生産するのに最も一般的な方法であり、効率的です。押出成形は長尺の製品や一貫した形状の製品に適しており、パイプやチューブの製造に利用されます。ブロー成形は中空容器の製造に向いており、例えばボトルなどの製品がこれに該当します。他にも、真空成形や圧縮成形、3Dプリンティングなど、多様な方法があり、それぞれの用途や目的に応じた選択が可能です。
射出成形とは何か?そのプロセスを詳しく解説
射出成形は、熱可塑性樹脂を加熱して溶かし、金型に射出して製品を形成する成形法です。このプロセスは、インサート成形やインジェクション成形とも呼ばれます。材料をホッパーからバレルに投入し、バレル周囲の加熱リングが材料を溶かします。溶けた材料は金型キャビティに射出され、冷却されて固化します。この方法は、自動車部品や家庭用品などの複雑な形状の部品を大量に生産するのに非常に効率的で経済的です。
押出成形やブロー成形など、他の成形法の特徴
押出成形は、加熱溶融した樹脂をダイから押し出し、連続的に成形する方法です。この方法は、長いチューブ状や棒状の製品に適しており、主に配管やフィルムの製造に用いられます。ブロー成形は、溶融樹脂をパリソン(円筒状の形)に押し出し、金型内で空気を吹き込み中空製品を成形する手法です。この成形法は、特にプラスチック容器やボトルの製造に活用されます。これらの方法はさまざまな製品の製造に応用され、各成形法の特性を活かした製品設計が求められます。
樹脂成形の量産方法を探る
樹脂成形の量産方法には様々なアプローチがあります。最も一般的な方法は「射出成形」で、プラスチック製品を大量に生産する際に広く使用されています。射出成形は、熱可塑性樹脂を加熱して溶融状態にし、高圧で金型に射出して成形する方法です。これにより、製品の寸法精度が高く、表面仕上げも良好な製品が安定して得られます。例えば、自動車部品や家電製品のケースなどが射出成形で作られています。成形方法は製品の種類や要求される特性によって選択されるべきです。
量産に適した成形法の種類と選び方
量産に適した成形法には、射出成形、ブロー成形(中空成形)、押出し成形などがあります。射出成形は高精度で多様な形状の製品製作に優れており、ブロー成形は中空の製品、例えばペットボトルなどに適しています。押出し成形は長尺物や断面形状を持つ製品に最適です。成形法の選択には、使用する樹脂の種類、製品の設計、コスト、生産速度などを考慮する必要があります。例えば、自動車のダッシュボードは形状の複雑さや耐久性が求められるため、射出成形が好まれます。
量産時の効率性を高めるためのポイント
効率的な量産を実現するためには、加工プロセスの見直しや効率的な機械の活用が重要です。例えば、作業の流れや手順を最適化し、無駄な動きを排除することが挙げられます。また、最新の成形機を導入し、成形サイクルタイムを短縮することで、生産効率を向上させることができます。さらに、品質管理システムを導入し、製品の不良を減少させることも効果的です。これにより、製品の一貫した品質を保ちつつ、生産コストを削減できます。
樹脂成形導入時のコストと効率性の考慮
樹脂成形を導入する際には、コストと効率性のバランスを考慮することが極めて重要です。合理化されたツール設計により、成形プロセスのサイクルタイムが短縮され、生産効率が向上し、製造コストが削減されます。例えば、射出成形での不合格率を下げ、スクラップ材料を減らすことが効率性向上に寄与します。こうした施策により、製品の品質と生産性が向上し、企業の競争力が強化されます。
樹脂成形におけるコスト構造を理解する
樹脂成形におけるコスト構造を理解することは、製造プロセスの最適化に欠かせません。主要なコスト要因には、材料費、加工費、設備費、金型費などが存在します。これらは製品の価格に大きく影響を与えるため、各要因の割合を理解し、効率的なコスト管理を行うことが求められます。例えば、材料費は射出成形金型コストの15%から30%を占めることが一般的です。
効率的な樹脂成形のためのヒントと対策
効率的な樹脂成形を実現するには、プロセス条件の最適化が不可欠です。材料の選定、加熱温度、冷却速度、注入速度など、さまざまな要素が製品の品質に影響を与えます。例えば、成形品の不良を減らすためには、射出速度を調整し、金型の温度を適切に管理することが効果的です。また、スマートファクトリー化は生産性の向上に大きく寄与し、カーボンニュートラルの推進にも繋がります。
まとめ
樹脂成型は、様々な種類があり、それぞれが異なる特性を持っています。射出成型は高精度な製品が作れる一方で、圧縮成型は大型部品に適しています。また、ブロー成型は中空製品を作成するのに最適で、真空成型は薄い樹脂シートを利用した成型に優れています。これらの技術を理解することで、最適な方法を選択し、製品開発を行うことが可能になります。
さらに、樹脂成型の選択肢を検討する際には、用途や求められる性能、コストなどを考慮することが重要です。各成型方法の特徴を生かし、効果的な生産プロセスを選ぶことで、品質の高い製品を効率よく生み出すことができるでしょう。