工作機械の種類や金属加工の種類を詳しく解説
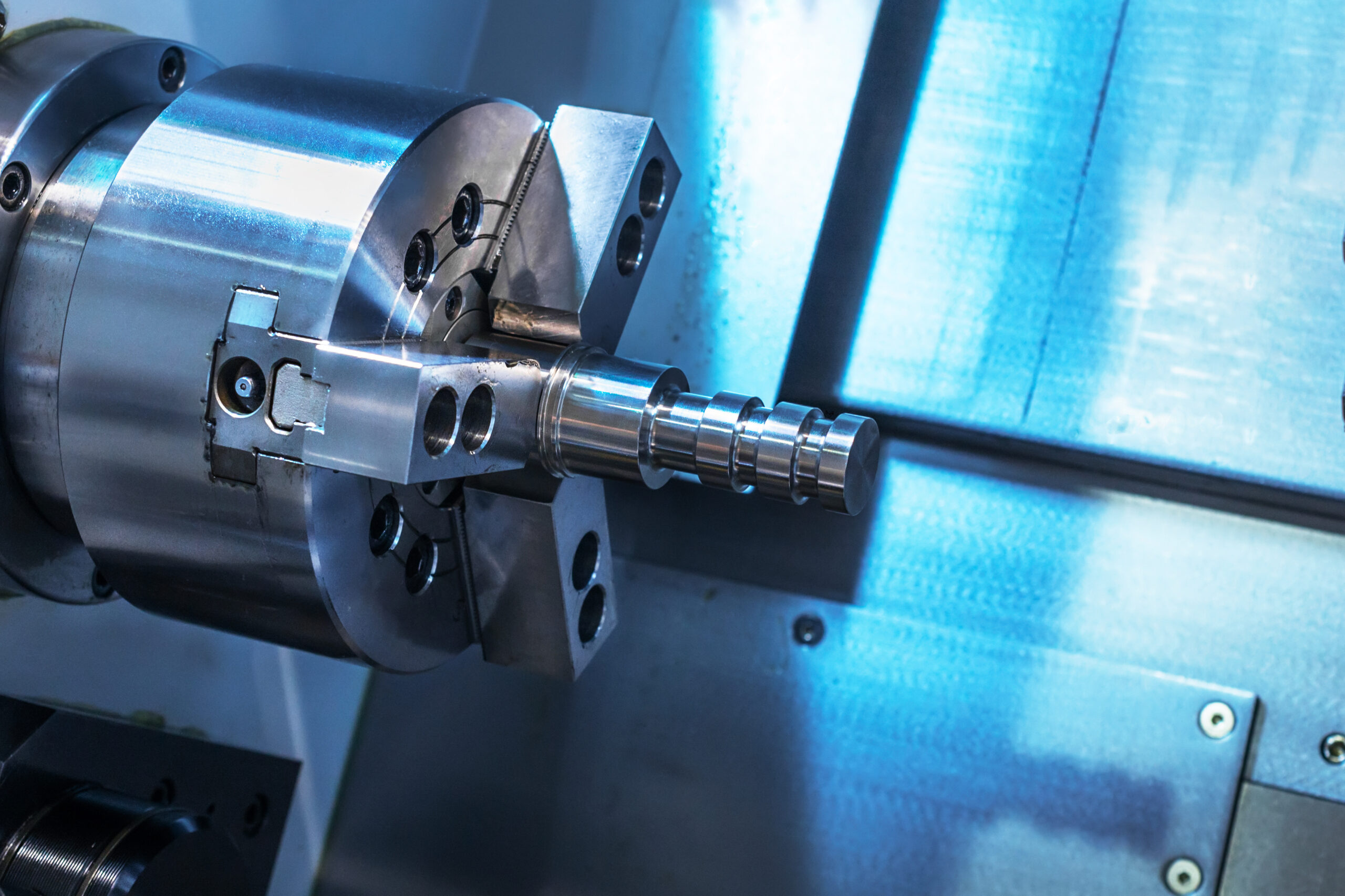
工作機械は、金属やプラスチックなどの材料を切削加工したり、塑性加工したりする機械です。工作機械は、様々な種類があり、それぞれに異なる機能と用途があります。
NC工作機械は、数値制御によって動作する工作機械です。NC工作機械は、従来の工作機械よりも自動化されており、精度が高く、効率的です。CNC工作機械は、航空機や自動車などの複雑な部品の製造に使用されています。
CNC工作機械は、コンピュータによって制御されます。コンピュータは、工作機械の動作を制御するプログラムを実行します。プログラムは、CAD/CAMソフトウェアを使用して作成されます。CAD/CAMソフトウェアは、コンピュータを使用して設計図を作成し、工作機械の動作をシミュレートするためのソフトウェアです。
旋盤は、回転する材料を切削加工する工作機械です。旋盤は、円筒形の部品や球形の部品の製造に使用されています。マシニングセンタは、複数の切削工具を使用して様々な形状の部品を加工できる工作機械です。マシニングセンタは、複雑な部品の製造に使用されています。
金属加工は、金属を切削加工したり、塑性加工したりするプロセスです。金属加工は、様々な方法で行うことができます。切削加工は、切削工具を使用して金属を切削するプロセスです。研削加工は、砥石を使用して金属を研磨するプロセスです。放電加工は、電極とワークピースの間に放電現象を起こして金属を加工するプロセスです。
成型加工は、金属を加熱したり、圧力を加えたりして変形させるプロセスです。塑性加工は、金属を加熱したり、圧力を加えたりして塑性変形させるプロセスです。鋳造は、溶けた金属を型に流し込んで固めるプロセスです。
付加加工は、金属を積層したり、被覆したり、接合したりするプロセスです。積層造形は、金属粉末や樹脂を積層して立体物を形成するプロセスです。被覆加工は、金属の表面に別の金属や樹脂を被覆するプロセスです。接合加工は、金属同士を接合するプロセスです。
熱処理は、金属の機械的性質を変化させるプロセスです。熱処理は、金属を加熱したり、冷却したりするプロセスです。
工作機械の基本とは?
工作機械とは、金属などの材料を切削や研磨、塑性加工などによって加工するための機械です。様々な種類があり、それぞれ得意な加工方法や用途があります。
工作機械の基本的な構成は、以下の通りです。
- 主軸: 回転運動を伝える部分
- ベッド: 主軸や工具台を支える台座
- 工具台: 工具を取り付ける部分
- 送り機構: 工具を送り込むための機構
工作機械には、手動で操作するものと、コンピュータで制御されるものがあります。コンピュータで制御される工作機械は、NC工作機械と呼ばれ、より複雑な加工を行うことができます。
NC工作機械の利点とは?
NC工作機械は、コンピュータプログラムで制御された工作機械です。従来の手動制御の工作機械と比較して、NC工作機械には多くの利点があります。
NC工作機械は、プログラムに従って正確に工具を制御するため、手動制御よりも高い精度と品質を実現できます。プログラムに従って自動的に動作するため、オペレーターの負担を軽減し、生産効率を向上させます。複雑な形状の加工もプログラムで制御できるため、手動制御では難しい加工も可能になります。
プログラムに従って常に同じ動きをするため、製品の品質を安定させることができます。自動化されているため、オペレーターの人件費を削減できます。プログラムに従って動作するため、オペレーターが危険な作業をする必要がなく、安全性を向上させます。プログラムデータを保存できるため、データ管理が容易になります。
NC工作機械は、さまざまな分野で活用されており、産業の発展に大きく貢献しています。
参考情報
NC工作機械とCNC工作機械の違いとは?
工作機械には、数値制御(NC)工作機械とコンピュータ数値制御(CNC)工作機械の2種類があります。どちらもプログラムに従って自動的に加工を行う機械ですが、いくつかの違いがあります。
- 制御方式: NC工作機械は、パンチカードやテープに記録されたプログラムに従って動作します。一方、CNC工作機械は、コンピュータに記憶されたプログラムに従って動作します。
- 柔軟性: CNC工作機械は、NC工作機械よりも柔軟性が高く、プログラムの変更や追加が容易です。
- 精度: CNC工作機械は、NC工作機械よりも精度が高く、複雑な加工にも対応できます。
- コスト: CNC工作機械は、NC工作機械よりもコストが高くなります。
NC工作機械とCNC工作機械の違いを理解することで、それぞれの機械の適した用途を選択することができます。
工作機械とは
工作機械は、金属やプラスチックなどの材料を切削加工したり、曲げたり、穴を開けたりする機械のことです。工作機械は、さまざまな産業で使用されており、現代社会を支える重要な機械です。
CNC工作機械の定義
CNC工作機械は、コンピュータの数値制御によって動作する工作機械のことです。CNC工作機械は、プログラムに従って自動的に加工を行うことができるため、高精度な加工が可能です。また、プログラムの変更や追加が容易なため、柔軟性も高いです。
NC工作機械とCNC工作機械の違い
NC工作機械とCNC工作機械の違いは、制御方式と柔軟性、精度、コストです。NC工作機械は、パンチカードやテープに記録されたプログラムに従って動作し、CNC工作機械は、コンピュータに記憶されたプログラムに従って動作します。CNC工作機械は、NC工作機械よりも柔軟性が高く、プログラムの変更や追加が容易です。また、CNC工作機械は、NC工作機械よりも精度が高く、複雑な加工にも対応できます。CNC工作機械は、NC工作機械よりもコストが高くなります。
NC工作機械とCNC工作機械の適した用途
NC工作機械とCNC工作機械の適した用途は、加工の精度や複雑さ、コストによって異なります。高精度な加工が必要な場合は、CNC工作機械が適しています。複雑な加工が必要な場合も、CNC工作機械が適しています。コストを抑えたい場合は、NC工作機械が適しています。
〈工作機械とは〉
工作機械とは、金属や樹脂などの材料を切削加工したり、塑性加工したりする機械の総称です。工作機械には様々な種類があり、それぞれ得意な加工方法や加工対象が異なります。
工作機械は、現代の工業社会に欠かせない存在であり、自動車や機械製品からスマートフォンや家電製品まで、あらゆる製品の生産に用いられています。
<工作機械の種類>
工作機械には、さまざまな種類があります。ここでは、代表的な工作機械の種類について紹介します。
<切削加工機>
- 旋盤: 円筒形や円盤状の材料を回転させ、刃物で切り削りして加工する機械です。
- フライス盤: 刃物が回転しながら材料を切削し、溝や面などの加工を行う機械です。
- ボール盤: ドリルを使って穴をあける機械です。
- 穴あけ盤: 穴あける作業に特化した機械です。
<成形加工機>
- プレス機: 金属板などの素材に力を加え、塑性変形させて加工する機械です。
- 鍛造機: 金属を加熱し、ハンマーやプレス機で叩いて塑性加工する機械です。
- 曲げ加工機: 金属板などを曲げる機械です。
<研削加工機>
- 平面研削盤: 平らな砥石を使って材料の表面を研削する機械です。
- 円筒研削盤: 円筒形の砥石を使って材料の表面を研削する機械です。
- 工具研削盤: 切削工具などを研磨する機械です。
<特殊工作機>
- 放電加工機: 電極と加工物間に電気を流して放電させ、加工物の一部を溶かしながら形状を作り出す機械です。
- レーザー加工機: レーザー光線で材料を切断したり、彫刻したりする機械です。
- ウォータージェット加工機: 高圧の水流で材料を切断する機械です。
〈CNC工作機械の定義〉
CNC工作機械とは、コンピュータによって制御される工作機械のことです。NCとはNumerical Controlの略であり、コンピュータに数値データを与えることで機械を制御することができます。CNC工作機械はさまざまな用途で使用されており、金属加工やプラスチック加工、木材加工などさまざまな分野で広く活躍しています。
<NC工作機械とCNC工作機械の違い>
NC工作機械とCNC工作機械の違いは、数値制御の方法にあります。NC工作機械は、パンチテープや磁気テープなどのメディアに数値情報を記録し、機械に読み込ませます。一方、CNC工作機械はコンピュータに数値情報を入力し、直接機械を制御することができます。
<CNC工作機械の利点>
CNC工作機械には、さまざまな利点があります。
- 高い精度
- 高い効率
- 高い品質
- 柔軟性が高い
これらの利点により、CNC工作機械はさまざまな産業で広く活躍しています。特に、自動車産業や航空機産業などの精密な加工が必要な産業では欠かせない存在となっています。
旋盤の基本原理
旋盤の基本原理は、切削工具を回転させて、形状を加工する機械です。切削工具は、ワークピースを回転させながら、切削工具をワークピースに供給します。切削工具の回転速度とワークピースの回転速度は、加工形状に応じて調整されます。旋盤は、円筒形や円錐形の加工に適しています。
旋盤の基本原理を理解するには、以下の要素を理解する必要があります。
- 切削工具
- ワークピース
- 回転速度
- 加工形状
切削工具は、形状を加工するために使用する工具です。切削工具には、さまざまな種類があり、加工形状に応じて選択されます。
ワークピースは、加工される材料です。ワークピースには、さまざまな種類があり、加工形状に応じて選択されます。
回転速度は、切削工具とワークピースの回転速度のことです。回転速度は、加工形状に応じて調整されます。
加工形状は、加工される形状のことです。加工形状は、さまざまな種類があり、加工形状に応じて切削工具、ワークピース、回転速度が選択されます。
旋盤の基本原理を理解することで、旋盤を使用してさまざまな形状を加工することができます。
マシニングセンタの概要
マシニングセンタは、工具を自動的に交換しながら、さまざまな加工を行うことができる工作機械です。多軸制御機能を持ち、複雑な形状の加工にも対応できるため、近年では広く普及しています。
<マシニングセンタの特徴>
- 多軸制御機能: X, Y, Z 軸に加えて、回転軸や傾斜軸など、複数の軸を同時に制御することができます。
- 自動工具交換機能: ATC(Automatic Tool Changer)を搭載しており、工具を自動的に交換することができます。
- 高精度加工: サーボモーターやリニアモーターを採用することで、高い精度での加工が可能です。
- 無人運転: プログラム制御により無人運転が可能で、生産性の向上に貢献します。
<マシニングセンタの用途>
マシニングセンタは、航空機や自動車、医療機器など、さまざまな分野で利用されています。複雑な形状の部品や精密部品の製造に適しています。
<マシニングセンタの種類>
- 立形マシニングセンタ: 縦型の構造を持つマシニングセンタです。ワークをテーブルに固定して加工を行います。
- 横形マシニングセンタ: 横型の構造を持つマシニングセンタです。ワークをテーブルに対して水平に固定して加工を行います。
- 5軸マシニングセンタ: 3軸に加えて回転軸と傾斜軸を持つマシニングセンタです。複雑な3次元形状の加工が可能です。
<マシニングセンタ導入のメリット>
- 生産性の向上: 自動化による無人運転が可能となり、生産性を向上させることができます。
- 高精度加工: サーボモーターやリニアモーターを採用することで、高い精度での加工が可能となります。
- コスト削減: 複数工程を1台のマシニングセンタで加工できるため、加工コストを削減することができます。
<マシニングセンタの注意点>
- 導入コスト: マシニングセンタは高価な設備であるため、導入コストがかかります。
- 操作技術: マシニングセンタを操作するには、専門的な技術が必要です。
- 保守管理: マシニングセンタは定期的な保守管理が必要となります。
マシニングセンタは、多軸制御機能や自動工具交換機能など、さまざまな特徴を持つ高性能な工作機械です。複雑な形状の加工や精密部品の製造に適しており、生産性の向上やコスト削減に貢献します。
金属加工の基礎知識
金属加工には、切削加工、研削加工、塑性加工、電気化学加工など、さまざまな種類があります。これらの加工方法は、それぞれ異なる目的や効果を持ち、製品の形状や機能に合わせて使い分けられます。
<加工方法の選び方>
加工方法を選ぶ際には、以下の点を考慮する必要があります。
- 加工精度: 加工する製品の精度要求
- 加工速度: 加工時間を短縮したい場合
- 加工コスト: 加工費を抑えたい場合
- 加工品質: 表面仕上げや強度などの品質要求
<切削加工>
切削加工は、工具を用いて金属を削り取る加工方法です。高い加工精度が得られますが、加工時間がかかる傾向があります。
<研削加工>
研削加工は、研削砥石を用いて金属を削り取る加工方法です。切削加工よりも高い加工精度が得られますが、加工時間がさらに長くなります。
<塑性加工>
塑性加工は、金属に塑性変形を加えて加工する加工方法です。加工時間が短く、加工コストも比較的低くなります。
<電気化学加工>
電気化学加工は、電気分解を利用して金属を加工する加工方法です。複雑な形状の加工も可能ですが、加工精度が低い傾向があります。
金属加工には、さまざまな種類があり、製品の形状や機能に合わせて使い分けられます。加工方法を選ぶ際には、加工精度、加工速度、加工コスト、加工品質などを考慮する必要があります。
加工方法とその種類
金属加工には、切断、穴あけ、塑性加工など様々な方法があります。それぞれに、さらに細分化された種類が存在します。
- 切削加工
- フライス加工
- 旋盤加工
- ドリル加工
- 切断加工
- 研削加工
- 平面研削
- 円筒研削
- 内部研削
- 研磨加工
- バフ研磨
- バレル研磨
- ラッピング
- 放電加工
- ワイヤーカット放電加工
- ドリル放電加工
- 放電研削加工
これらの加工方法には、それぞれ得意な形状や材料、加工精度などがあります。また、加工方法によって加工にかかる時間や費用も異なります。
金属加工には、切削加工、研削加工、研磨加工、放電加工など多くの種類があります。それぞれに得意な形状や材料、加工精度があり、加工時間や費用も異なります。
これらの加工方法を理解することで、最適な加工方法を選択することができ、製品の品質向上やコスト削減を実現することができます。
次のセクションでは、各加工方法について詳しく説明します。
金属加工の基礎知識:切削加工
旋盤とフライス盤は、どちらも切削加工を行う工作機械ですが、得意とする加工形状や、加工精度が異なります。
旋盤は、回転する材料に対して工具を移動させて切削加工を行う機械です。円柱形状の材料や、円弧形状の加工に適しています。
フライス盤は、回転する工具に対して材料を移動させて切削加工を行う機械です。平面形状や、複雑な形状の加工に適しています。
▶ 旋盤
旋盤加工とは、回転するワークに対して固定された刃物で切削加工を行う切削加工方法の一種です。ワークはチャックやセンターで固定され、主軸によって回転します。刃物は旋盤台に取り付けられ、ワークの回転に合わせて送り運動を行いながら切削を行います。
旋盤加工は、円筒状や円錐状のワークの加工に適しており、外径加工、内径加工、ねじ切り加工、溝加工など、様々な加工を行うことができます。また、旋盤加工は精度が高く、複雑な形状のワークの加工にも対応できるため、機械加工において最も基本的な加工方法の一つとして広く用いられています。
旋盤加工の主な種類は以下のとおりです。
- 外径加工:ワークの外周を削って円筒状や円錐状にする加工。
- 内径加工:ワークの内周を削って円筒状や円錐状にする加工。
- ねじ切り加工:ワークにねじを切る加工。
- 溝加工:ワークに溝を切る加工。
旋盤加工には、切削速度や送り速度、切削深さなどの加工条件が設定されます。これらの加工条件は、ワークの材質、形状、切削工具の種類などに応じて最適なものを選択する必要があります。
旋盤加工は、熟練した技能を必要とする加工方法です。近年では、自動化や数値制御技術の進歩により、作業の効率化や精度向上が図られています。
フライス加工の基礎知識
フライス加工とは、回転する刃物(フライス)を用いて材料を切削加工する方法です。フライスは複数の刃を持ち、材料を削りながら回転することによって、形状を形成します。
フライス加工は、以下の特徴を持ちます。
- 多様な形状の加工が可能
- 高精度な加工
- 大量生産に適している
フライス加工には、以下の種類があります。
- エンドミル加工
- フェースミル加工
- サイドミル加工
フライス加工は、様々な産業分野で広く使用されています。機械部品の加工から、航空機や自動車の製造まで、幅広い用途で活用されています。
金属加工の基礎知識:研削加工
研削加工は、砥石を用いて金属を削り取る加工方法で、工作物の精度が非常に高くなることが特徴です。砥石は砥粒と結合剤からできており、砥粒が金属を削り取っていきます。研削加工にはさまざまな種類がありますが、代表的なものには以下の3つの種類があります。
1. 表面研削 砥石を回転させながら工作物の表面に押し付け、表面を平滑にします。
2. 円筒研削 砥石を回転させながら工作物の中心に回転させ、工作物の外径を研削します。
3. 内径研削 砥石を回転させながら工作物を回転させ、工作物の内径を研削します。
研削加工は切削加工と比較して、以下の3つのメリットがあります。 メリット1 高精度の加工が可能 メリット2 硬度の高い材料も加工が可能 メリット3 表面を鏡面仕上げにすることも可能
しかし、研削加工には切削加工と比較して、以下の2つのデメリットがあります。
デメリット1 切削加工と比べると加工速度が遅い デメリット2 切削加工よりもコストが高い
結論 研削加工は高精度の加工が要求される場合や硬度の高い材料を加工する際に有効な加工方法です。加工速度やコストがネックになるため、切削加工との使い分けが重要になります。
金属加工の基礎知識:研磨加工
研磨加工とは、砥石や研磨布などの研磨材を用いて、材料の表面を削り、平滑に仕上げる加工方法です。切削加工とは異なり、削り取る量は微量で、表面の形状や寸法精度を向上させることを目的としています。
研磨加工には、以下の特徴があります。
- 高精度加工が可能: 切削加工に比べて、加工精度が高く、表面粗さをナノメートルレベルまで仕上げることができます。
- 硬い材料の加工が可能: ダイヤモンドなどの超硬材料を使用することで、硬い材料の加工も可能です。
- 複雑な形状の加工が可能: ダイヤモンド砥石などの柔軟な研磨材を使用することで、複雑な形状の加工も可能です。
研磨加工には、以下の種類があります。
- 平面研削: 平らな砥石を使用して、材料の表面を平らに仕上げる加工方法です。
- 円筒研削: 円筒形の砥石を使用して、材料の外周を円筒形に仕上げる加工方法です。
- 内面研削: 円筒形の砥石を使用して、材料の内面を円筒形に仕上げる加工方法です。
- 工具研削: 切削工具や金型などの工具を研磨して、切れ味を回復させる加工方法です。
研磨加工は、様々な分野で用いられています。特に、機械部品や金型の製造、精密機器の組み立て、半導体製造など、高精度な表面仕上げが要求される分野で広く活用されています。
金属加工の基礎知識:放電加工
放電加工 (EDM) は、電気的放電を利用して金属を切断する加工方法です。金属を工具電極に近づけて、両者の間に電極ギャップと呼ばれる隙間を作り、そのギャップに誘電流体を流します。誘電流体は絶縁体ですが、電極ギャップの電圧が上昇すると、誘電流体はプラズマ状態に変化し、金属が溶融または蒸発します。このプロセスを繰り返し行うことで、金属を切断または造型します。
放電加工は、硬くて複雑な形状の金属を加工するのに適しています。また、熱影響が小さく、切断面の品質が高いという特徴があります。
放電加工のメリット:
- 硬くて複雑な形状の金属を加工できる
- 熱影響が小さい
- 切断面の品質が高い
放電加工のデメリット:
- 加工速度が遅い
- 誘電流体の処理が必要
- 工具電極の摩耗が激しい
成型加工の種類とその特徴
成型加工とは、塑性加工や鋳造など、さまざまな方法を用いて金属などの材料を所望の形状に変える加工方法です。代表的な成型加工の種類とその特徴について、以下に説明します。
塑性加工は、金属材料に外力を加えて塑性変形させることで、所望の形状に加工する方法です。鍛造、圧延、絞り加工などが含まれます。塑性加工は、材料の機械的特性を向上させることができるという利点があります。
鋳造は、溶融した金属を鋳型に流し込んで固化させることで、所望の形状に加工する方法です。砂型鋳造、金型鋳造などが含まれます。鋳造は、複雑な形状の製品を製造できるという利点があります。
どちらの成型加工方法も、大量生産に適しています。塑性加工と鋳造は、それぞれ異なる特徴があり、用途に応じて適切な方法を選択する必要があります。
これらの加工方法の詳細については、後続の「成型加工の基礎知識:塑性加工」および「成型加工の基礎知識:鋳造」で詳しく説明します。
成型加工の基礎知識:塑性加工
成型加工とは、塑性変形を利用して金属材料に所望の形状を与える加工方法です。塑性加工には、プレス加工、鍛造、転造など様々な種類があります。
<プレス加工の基礎知識> プレス加工は、金型とプレス機を用いて、金属材料に圧力を加えて変形させる加工方法です。プレス加工には、曲げ加工、絞り加工、打ち抜き加工などがあります。
<鍛造の基礎知識> 鍛造は、金型とハンマーを用いて、金属材料を叩いて変形させる加工方法です。鍛造は、金属材料の密度を高め、強度を高めることができます。
<転造の基礎知識> 転造は、金型と転造工具を用いて、金属材料を転がしながら変形させる加工方法です。転造は、表面を滑らかに仕上げ、寸法精度を高めることができます。
これらの塑性加工は、それぞれ異なる特徴を持ち、様々な用途で使用されています。
プレス加工の基礎知識
プレス加工は、金属板や樹脂板などの板材に、プレス機を用いて力を加えて塑性変形させる加工方法です。金属加工において最も一般的な方法の一つであり、大量生産に適していることから、自動車や家電製品などの様々な分野で広く用いられています。
プレス加工には、以下の特徴があります。
- 大量生産に適している: プレス機は一度に複数の製品を加工することができ、大量生産に適しています。
- 寸法精度が高い: プレス加工は金型を用いて加工するため、寸法精度が高く、安定した品質の製品を生産することができます。
- 自動化しやすい: プレス加工は自動化しやすく、人件費を削減することができます。
プレス加工には、以下の種類があります。
- 打ち抜き: 金型を用いて板材から所定の形状を切り抜く加工方法です。
- 曲げ: 金型を用いて板材を曲げる加工方法です。
- 絞り: 金型を用いて板材を絞り込んで立体形状を作る加工方法です。
- 深絞り: 絞りの一種で、板材を深く絞り込んで複雑な形状を作る加工方法です。
プレス加工は、様々な製品の製造に用いられており、私たちの生活に欠かせない技術の一つです。
鍛造の基礎知識
鍛造は、金属を加熱して軟化させ、ハンマーやプレスなどの機械を用いて叩いたり圧力をかけたりして塑性変形させる加工方法です。鍛造は、金属の組織を緻密化させ、強度や靭性を向上させる効果があります。
鍛造は、主に以下の利点があります。
- 強度と靭性の向上: 鍛造により、金属の内部組織が緻密化され、結晶粒が微細化されます。これにより、金属の強度と靭性が向上します。
- 成形性の向上: 鍛造は、金属を塑性変形させることで、複雑な形状に成形することができます。
- 耐疲労性の向上: 鍛造された金属は、疲労破壊に対する抵抗力が向上します。
鍛造は、主に以下の用途で使用されています。
- 機械部品: クランクシャフト、ピストンロッド、ギアなど
- 工具: ハンマー、スパナ、レンチなど
- 建材: ボルト、ナット、リベットなど
- その他: スポーツ用品、装飾品など
鍛造には、以下の種類があります。
- 自由鍛造: ハンマーやプレスなどの機械を用いて、金属を自由に叩いたり圧力をかけたりして成形する鍛造方法です。
- 型鍛造: 金属を金型に入れて、ハンマーやプレスなどの機械を用いて成形する鍛造方法です。
- 転造: 転造盤を用いて、金属を回転させながら圧力をかけて成形する鍛造方法です。
転造の基礎知識
転造加工とは、塑性加工の一種であり、塑性変形を利用して金属材料を所望の形状に成形する加工方法です。転造では、回転する工具(転造工具)とワークピースを圧接させて、ワークピースの表面に工具の形状を転写します。転造加工は、高精度、高効率、低コストなどの利点があります。
転造加工は、塑性変形を利用して金属材料を成形する加工方法です。塑性変形とは、固体材料に外力を加えて、その形状を変化させることです。塑性変形は、降伏応力と呼ばれる限界を超えて外力を加えることで発生します。
転造加工では、回転する工具(転造工具)とワークピースを圧接させて、ワークピースの表面に工具の形状を転写します。工具の回転によって、ワークピースの表面に大きな圧力が加えられ、塑性変形が発生します。塑性変形によって、ワークピースの形状が変化し、工具の形状に近づきます。
転造加工には、次のような利点があります。
- 高精度:転造加工は、高精度の加工が可能です。これは、転造工具の形状がそのままワークピースに転写されるためです。
- 高効率:転造加工は、高効率の加工が可能です。これは、転造加工が連続加工であるためです。
- 低コスト:転造加工は、低コストの加工が可能です。これは、転造加工が工具の寿命が長く、加工時間が短いいためです。
転造加工は、次のような用途に使用されています。
- シャフトの表面硬化
- ベアリングの転がり面の形成
- ギアの歯車の形成
- スプラインの形成
- ネジの形成
- 表面粗さの改善
転造加工は、さまざまな産業で使用されており、自動車、機械、家電、航空宇宙など、幅広い分野で活躍しています。
成型加工の基礎知識:鋳造
鋳造とは、溶融状態にした金属を鋳型に流し込んで固化させることで、所望の形状に成形する加工方法のことです。鋳造は、金属加工の中でも古くから行われている代表的な加工方法の一つであり、複雑な形状や大型の製品を効率的に製造できることが特徴です。
鋳造には、いくつかの種類があり、代表的なものとして砂型鋳造、金型鋳造、ダイカストがあります。砂型鋳造は、砂で作った鋳型を用いる最も一般的な鋳造方法です。金型鋳造は、金属で作った鋳型を用いる鋳造方法で、砂型鋳造よりも精度が高く、大量生産にも適しています。ダイカストは、溶融金属を高い圧力で鋳型に注入する鋳造方法で、薄肉で精密な製品の製造に適しています。
鋳造には様々なメリットがあります。まず、複雑な形状や大型の製品を製造できることです。鋳造は、溶融金属を鋳型に流し込むことで成形するため、切削加工などでは難しい形状や大型の製品を製造することができます。また、大量生産にも適していることです。鋳造は、一度に複数の製品を製造することができるため、大量生産に適しています。さらに、コストを抑えることができることです。鋳造は、比較的安価な設備で製造できるため、コストを抑えることができます。
一方で、鋳造にはデメリットもあります。まず、寸法精度が低いことです。鋳造は、溶融金属を鋳型に流し込むことで成形するため、寸法精度が低くなってしまいます。また、表面粗さが大きいことです。鋳造は、鋳型との接触面が荒いため、表面粗さが大きくなってしまいます。さらに、内部欠陥が発生しやすいことです。鋳造は、溶融金属を鋳型に流し込む際に気泡や異物が混入することがあり、内部欠陥が発生しやすくなってしまいます。
このように、鋳造はメリットとデメリットがあります。鋳造は、複雑な形状や大型の製品を効率的に製造できることが特徴ですが、寸法精度が低く、表面粗さが大きく、内部欠陥が発生しやすいというデメリットがあります。そのため、鋳造には適した用途があります。鋳造は、複雑な形状や大型の製品を製造するのに適していますが、寸法精度や表面粗さが求められる製品には適していません。
付加加工の種類とその利点
付加加工とは、材料を削り取るのではなく、材料を加えることで加工を行う方法です。積層造形、被覆加工、接合加工など、様々な種類があります。
積層造形は、3Dプリンタなどを使用し、材料を積層することで立体物を作り出す加工方法です。被覆加工は、金属や樹脂などの材料を、他の材料で覆うことで、表面の性質を変化させる加工方法です。接合加工は、熱や接着剤などを使用して、複数の材料を接合する加工方法です。
付加加工の利点は、複雑な形状の加工が可能、材料の無駄が少ない、短納期で加工が可能などがあります。これらの利点から、付加加工は様々な分野で注目を集めています。
それぞれの加工方法の詳細については、以下のヘッドラインをご覧ください。
- 付加加工の基礎知識:積層造形
- 付加加工の基礎知識:被覆加工
- 付加加工の基礎知識:接合加工
付加加工の基礎知識:積層造形
積層造形は、3Dデータを元に材料を積層して立体物を形成する付加加工技術です。従来の切削加工とは異なり、材料を削り取るのではなく、材料を積層して形を作っていくため、複雑な形状や中空構造など、従来の加工では難しかった形状も実現できます。
積層造形は、近年急速に発展しており、航空宇宙、医療、建築など様々な分野で活用されています。以下に、積層造形の主な特徴をリストアップします。
- 複雑な形状の製作が可能
- 軽量化が実現できる
- 短納期での製作が可能
- 試作品の製作に適している
- 材料の無駄が少ない
積層造形は、今後ますます発展していくことが期待されており、製造業の革新に大きな役割を果たしていくと考えられます。
付加加工の基礎知識:被覆加工
被覆加工とは、金属や樹脂などの母材の表面に、別の金属や樹脂、セラミックスなどの材料を、溶射や塗装、メッキなどの方法で付着させる加工のことです。被覆加工を行うことで、母材の表面に様々な機能を付与することができます。
被覆加工には、耐摩耗性、耐食性、耐熱性、耐薬品性、電気絶縁性、潤滑性、装飾性などの様々な機能を付与することができます。例えば、耐摩耗性を向上させたい場合は、表面に硬質のセラミックスを被覆します。耐食性を向上させたい場合は、表面にステンレス鋼やクロムメッキを被覆します。耐熱性を向上させたい場合は、表面に耐熱性のセラミックスや金属を被覆します。
被覆加工は、様々な産業分野で広く利用されています。例えば、自動車産業では、エンジン部品やブレーキ部品に耐摩耗性の高い被覆を施すことで、部品の寿命を延ばしています。航空機産業では、航空機部品に耐食性の高い被覆を施すことで、腐食による事故を防いでいます。医療機器産業では、医療機器に耐薬品性の高い被覆を施すことで、薬液による腐食を防いでいます。
被覆加工は、母材の表面に様々な機能を付与することができるため、様々な産業分野で重要な役割を果たしています。
被覆加工の主な種類は以下の通りです。
- 溶射
- 塗装
- メッキ
- 化学被覆
- 物理蒸着
- 化学蒸着
被覆加工の用途は以下の通りです。
- 耐摩耗性
- 耐食性
- 耐熱性
- 耐薬品性
- 電気絶縁性
- 潤滑性
- 装飾性
被覆加工のメリットは以下の通りです。
- 母材の表面に様々な機能を付与することができる。
- 母材の表面を保護することができる。
- 母材の外観を改善することができる。
被覆加工のデメリットは以下の通りです。
- 被覆材の選択や加工方法によっては、コストがかかる場合がある。
- 被覆材の付着力が弱いと、剥離する恐れがある。
- 被覆材の厚みによっては、母材の形状が変化する場合がある。
付加加工の基礎知識:接合加工
接合加工は、異なる材料や部品を熱や圧力、接着剤などを用いて一体化させる加工方法です。 溶接、ろう付け、はんだ付け、接着など様々な方法があり、それぞれ特徴や用途が異なります。
接合加工の主な利点として、以下の点が挙げられます。
- 複雑な形状の製品を製造できる
- 軽量化が可能
- コスト削減
接合加工は、様々な産業で幅広く活用されています。 自動車、航空機、家電、建設など、様々な分野で接合加工技術が用いられています。
熱処理の重要性と方法
熱処理は、金属の機械的特性を改善するために不可欠なプロセスです。金属を加熱し、冷却することで、硬度、靭性、延性など様々な特性を変化させることができます。
熱処理には、様々な方法があります。
- 焼鈍: 金属を高温に加熱し、ゆっくりと冷却することで、硬度を下げ、靭性を高めます。
- 焼入れ: 金属を高温に加熱し、急冷することで、硬度と強度を高めます。
- 焼き戻し: 焼入れした金属を再度加熱し、ゆっくりと冷却することで、硬度と靭性のバランスを調整します。
- 表面硬化: 金属の表面のみを硬化させ、耐摩耗性を高めます。
熱処理は、様々な産業で広く利用されています。自動車、航空機、機械、建設など、多くの分野で使用される金属部品の製造に欠かせないプロセスです。
熱処理の重要性を理解し、適切な方法を選択することで、金属の特性を最大限に引き出し、製品の品質と耐久性を向上させることができます。
機械加工の種類
機械加工は、金属やプラスチックなどの材料を切削、研削、塑性加工などの方法で所望の形状に加工する技術です。工作機械と呼ばれる機械を使用し、材料を除去したり、変形させたりすることで、様々な製品の部品や構造物などを製造します。
機械加工の種類は、大きく分けて切削加工、研削加工、成形加工に分類されます。
<切削加工>
切削加工は、回転する工具を用いて材料を削り取ることで形状を形成する加工方法です。代表的な切削加工には、旋盤加工、フライス加工、ドリル加工などがあります。
- 旋盤加工: 回転する円筒状の材料を切削工具で削り取る加工方法です。
- フライス加工: 回転する多刃工具を用いて材料を削り取る加工方法です。
- ドリル加工: 回転するドリルで材料に穴を開ける加工方法です。
<研削加工>
研削加工は、砥石と呼ばれる研磨材を用いて材料を削り取ることで表面を平滑に仕上げる加工方法です。代表的な研削加工には、平面研削、円筒研削、工具研削などがあります。
- 平面研削: 砥石が回転する平面研削盤を用いて材料の表面を平滑に仕上げる加工方法です。
- 円筒研削: 砥石が回転する円筒研削盤を用いて材料の円筒形状を正確に仕上げる加工方法です。
- 工具研削: 砥石を用いて切削工具の刃先を研磨し、切れ味を回復させる加工方法です。
<成形加工>
成形加工は、材料に力を加えて変形させることで所望の形状に加工する加工方法です。代表的な成形加工には、プレス加工、鍛造、転造などがあります。
- プレス加工: 金型を用いて材料を圧力によって変形させる加工方法です。
- 鍛造: 金型を用いて材料をハンマーで叩いて変形させる加工方法です。
- 転造: 転造工具を用いて材料の表面を圧縮することで硬化させる加工方法です。
以上のように、機械加工には様々な種類があり、それぞれ得意とする加工方法や用途があります。製品の形状や材質、精度に応じて適切な加工方法を選択することが重要です。
機械加工の加工方法
機械加工は、金属材料を切削工具で除去することで、所定の形状や寸法に加工する工程です。様々な方法があり、それぞれの特徴や用途があります。
主な機械加工方法としては、切削加工、研削加工、研磨加工、放電加工などがあります。
切削加工は、回転する円筒状の材料を切削工具で切削し、円筒状や円錐状の形状に仕上げる旋盤加工、回転する切削工具で材料を切削し、平面や溝、穴などの形状に仕上げるフライス加工、ドリルを回転させながら材料に穴を開けるドリル加工、ドリル盤を使用して、穴あけやねじ立てなどの加工を行うボール盤加工、ねじ穴を加工する工具(タップ)を用いて、雌ねじを形成するタップ加工などがあります。
研削加工は、研削砥石を使って、材料の平面を研削する平面研削、研削砥石を使って、材料の円筒面を研削する円筒研削、研削砥石を使って、材料の内径を研削する内径研削などがあります。
研磨加工は、バフと呼ばれる布製の研磨材を使って、材料の表面を滑らかに仕上げるバフ研磨、材料を研磨材と一緒に回転するバレルに入れて、表面を滑らかに仕上げるバレル研磨などがあります。
放電加工は、細いワイヤ電極とワークの間を放電させて、加工を行うワイヤ放電加工、電極とワークの間を放電させて、材料を溶融・蒸発させて加工するEDM(放電加工)などがあります。
上記以外にも、様々な機械加工方法があります。加工の種類や材料の特性、加工精度やコストなどを考慮して、適切な方法を選択する必要があります。
まとめ
工作機械は、金属などの材料を切削加工や研削加工、成形加工などによって、所望の形状や寸法に仕上げるための機械です。 大きく分けて、手動で操作する手動工作機械と、自動制御で加工を行うNC工作機械の2種類があります。 NC工作機械は、コンピュータで制御されるCNC工作機械と、数値制御されたテープで制御されるNC工作機械の2種類があります。
金属加工は、金属材料を加工して、所望の形状や寸法にすることです。切削加工、研削加工、成形加工、付加加工、熱処理などの様々な加工方法があります。
切削加工は、刃物を使って材料を削り取る加工方法です。旋盤やフライス盤、ドリル盤などが代表的な切削加工機械です。
研削加工は、砥石を使って材料を削り取る加工方法です。研削盤やホニング盤などが代表的な研削加工機械です。
成形加工は、材料に力を加えて、所望の形状に変化させる加工方法です。プレス加工や鍛造、転造、鋳造などが代表的な成形加工方法です。
付加加工は、材料に新しい材料を加えて、所望の形状に変化させる加工方法です。積層造形や被覆加工、接合加工などが代表的な付加加工方法です。
熱処理は、材料を熱して、その組織や性質を変える加工方法です。焼き入れや焼きなまし、焼き戻しなどが代表的な熱処理方法です。
工作機械や金属加工は、様々な製品の製造に必要不可欠な技術です。 工作機械や金属加工に関する知識は、製造業に携わるすべての人にとって重要です。