【知っておきたい】ローレット加工の基礎知識とそのメリットとは?
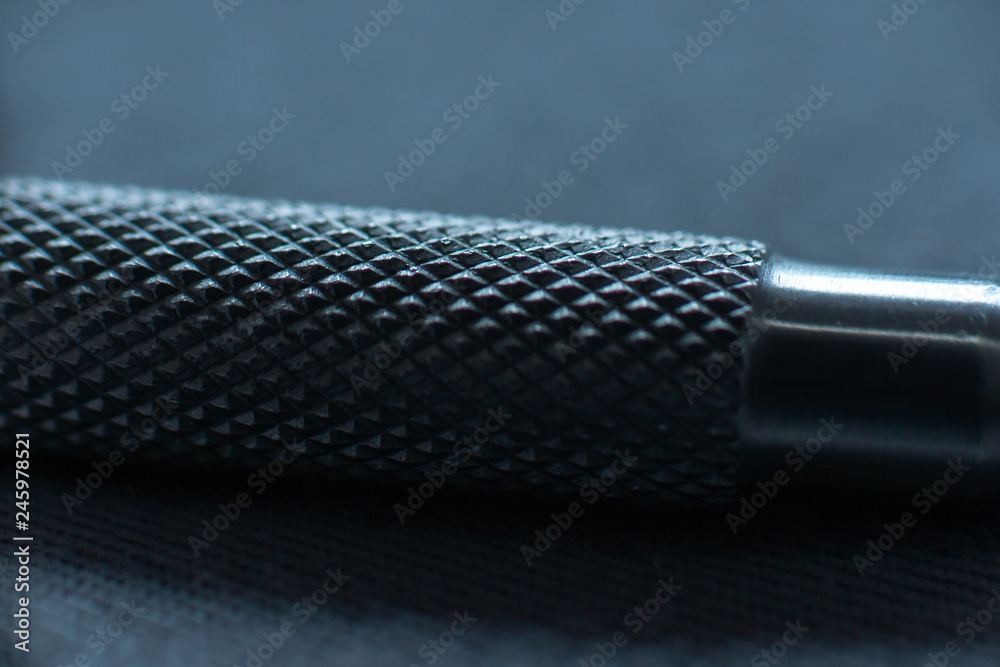
「ローレット加工」という言葉を聞いたことはありますか?この加工技術は、日常生活のさまざまな場面で目にすることができ、その重要性は計り知れません。特に、製品の滑り止め機能や美観を向上させるために広く利用されています。しかし、この加工がどのように行われ、どのようなメリットがあるのかをご存じでしょうか?
本記事では、ローレット加工の基本的な知識から、その利点までを詳しく解説します。もし、製品の品質向上やコスト削減を検討しているのであれば、ぜひ読み進めてみてください。知識を深めることで、あなたの製品開発や改善に役立つ情報が得られることでしょう。
この加工技術を理解することは、製造業において競争力を高めるための第一歩です。さあ、ローレット加工の世界を一緒に探求してみましょう!
ローレット加工とは?基本知識とそのメリット
ローレット加工とは、金属の表面に細かな凹凸模様を施す加工方法のことを指します。この加工は、主に金属製品において手で触れる部分の滑り止めを目的としています。ローレット加工には、素材に圧力を加えて変形させる転造式と、素材表面を削り取る切削式があります。切削式は、素材の直径が小さくなるため、対応可能な素材の幅が広いという特徴を持っています。一方、転造式は短時間で加工できる特性があるため、大量生産に向いています。これにより製品のグリップ性が向上し、安全性が高まるというメリットがあります。
ローレット加工の種類と特性を詳しく解説
ローレット加工には、切削方式と転造方式の2種類があります。切削方式は、ワークが素材系よりも小さくなりますが、対応可能な素材の幅が広く、ワークと機械への負担が少ない特性があります。転造方式は、金属の素材に向いた加工方法で、切削に比べて短時間で加工できるのが特徴です。これらの方法により、製品には滑り止めやデザイン性の向上、さらには機械的な耐久性が期待できます。具体例として、精密機器のハンドルや工具のグリップ部品などに活用され、使用時の安全性や操作性が向上します。
転造式と切削式のローレット加工の違い
ローレット加工は、転造式と切削式という2つの主要な方法があります。転造式ローレット加工は、工具をワークに押し付けて圧力を加え盛り上げる加工法です。この方法は、素材を削らずに加工が行われるため、ワークの機械に与える負担が少ないという特徴があります。一方で、切削式ローレット加工は、ワークにローレット工具を押し付けて削り出す方法です。これにより、機械への負担が軽減され、素材の直径を小さくすることができます。
転造式ローレット加工のメリット・デメリット
転造式ローレット加工の主なメリットは、加工時に切削くずが出ないため環境に優しく、短時間で加工が可能という点です。また、素材の直径を盛り上げることができるため、段差際までの加工が容易です。しかし、デメリットとしては、加工幅が限られるため、広範囲の加工には適していない場合があります。また、工具のピッチやラジアル送りを調整しなければうまく仕上がらないこともあります。
切削式ローレット加工のメリット・デメリット
切削式ローレット加工のメリットは、精度の高い加工が可能であり、特に寸法精度が求められる場面で有効です。また、難削材の加工においても、転造より工具への負担が少ないとされています。しかし、切削くずが発生し素材を削るため、材料の直径が小さくなってしまうのがデメリットです。また、工具が摩耗しやすく、長時間の使用には適していないことが多いです。
ローレット加工の適用製品と用途
ローレット加工の主な目的は滑り止めと回り止めです。例えば、ノブやつまみ、ネジ頭部分、グリップ、ハンドルバーなどがその対象となります。これらの部分に滑り止め効果を持たせることで、作業をより安全に行うことができます。また、ローレット加工は金属部品の外周に圧入することで、接合強度を高めるためにも利用されます。具体例として、自転車のグリップや工具のハンドル部分において、滑らずしっかりと保持できることが求められ、その効果を発揮します。したがって、ローレット加工は製品の安全性向上に大いに貢献します。
どのような製品にローレット加工が適しているのか
ローレット加工は特に滑り止めが必要な製品に適しています。例えば、工具のハンドルや自動車のギア シフトノブ、医療器具のグリップ部分などが挙げられます。これらの製品は、手や指が使用中に滑らないように設計されており、ローレット加工を施すことでその効果を発揮します。具体的には、工作機械の負担を小さくする効果もあり、加工時に生じる切りくずを排出しやすくするため、工作機械への負担を軽減することができます。例えば、薄肉や長物、細物の加工においても有効であり、特に加工精度と安全性を重視する製品に向いています。結果として、ローレット加工は多様な製品に利便性を提供します。
旋盤を用いたローレット加工の手順と注意点
ローレット加工を行う際には、いくつかの注意点とポイントがあります。まず、旋盤の操作方法を正確に理解し、安全に作業を行うことが重要です。また、ワークピースの材質や形状によって、適切なローレット工具を選ぶ必要があります。正しい工具の選択は、均一で高品質な仕上がりを得るための鍵となります。具体的な手順としては、まずワークピースを旋盤に正確に固定し、回転させながらローレット工具を押し当てて模様を転写します。この一連の作業を慎重に行うことで、均一なパターンを施すことができます。
具体的な作業手順を詳しく解説
ローレット加工の具体的な作業手順は、まずワークピースを旋盤に固定することから始まります。固定後、旋盤を起動し、ワークピースを回転させます。このとき、ローレット工具をワークピースに対して適切な位置に配置します。次に、工具を一定の圧力で押し当て、模様を刻み込みます。このプロセスを繰り返すことで、ワーク全体に均一に模様を施すことが可能です。最終的には、表面を確認し、必要であれば追加の仕上げを行って、望む仕上がりを得ることができます。
加工時に注意すべきポイント
ローレット加工時に注意すべきポイントは、適切な工具の選択とその使用方法です。不適切な工具や使用法は、加工精度や仕上がりに悪影響を与える可能性があります。また、加工中に工具が摩耗することがあるため、工具の状態を定期的にチェックし、必要に応じて交換することが重要です。さらに、加工過程で発生する切削屑は、仕上げに影響を与える可能性があるため、適切に排出する必要があります。これらのポイントを押さえることで、高品質なローレット加工を行うことができます。
ローレット加工導入時のコストと技術的課題
ローレット加工は、工業製品の滑り止めやデザインとして用いられる重要な加工手法ですが、導入時には様々なコストと技術的課題が存在します。まずコスト面では、切削式工具や転造式工具の選定が重要です。転造式工具は初期投資が大きい反面、効果的な量産加工が可能ですが、切削式工具はより細やかな対応が求められ、高度な技術が必要です。他方で、適切な在庫管理やコストの削減も大きな課題で、多品種少量生産に対応するための柔軟な戦略が求められます。こうした課題に対応するため、企業は加工技術の最適化や設備の選定を通じて、コスト効率の向上と生産体制の最適化を図る必要があります。
コスト面での考慮点
ローレット加工を導入する際に考慮すべきコスト面の要点は、設備投資と加工効率です。加工精度を維持しながら、コストダウンを図るには、効率的なプログラムの使用が不可欠です。例えば、特定の部品に適した切削速度や送り速度を最適化することで、加工時間を大幅に削減できるとされています。また、ローレット加工は仕上げの工程であり、基本形状が整った後に追加されるため、直接的な製造コストが増加する傾向にあります。適切な装置選定と工数管理が、コスト上昇を抑える鍵となるでしょう。
技術的な課題とその解決策
ローレット加工における技術的な課題は、加工精度や表面仕上げに影響を及ぼすことが多く、特に切削速度や工具の選定が重要です。加工時に過度の負荷がかかると、工具の消耗や表面の不具合につながります。これを防ぐためには、送り速度や切削速度の正確な調整が必要です。さらに、表面の仕上がりに影響を与える送り速度の適切な設定が求められます。最新のCNC技術やプログラムの導入により、こうした課題をクリアし、効率的かつ精度の高い加工を実現することが可能です。
まとめ
ローレット加工は、部品の表面に微細な凹凸を設ける技術で、主に摩擦力を向上させるために使用されます。この加工によって、部品同士のすべりを防ぎ、接触面の摩耗を減少させる効果があります。また、特に手で操作する部品においては、グリップ感を向上させることができるため、安全性や使い勝手の向上にも寄与します。
さらに、ローレット加工は多様な用途に対応できるため、産業界全体で広く採用されています。そのため、製品の性能向上やコスト削減にもつながる可能性があります。したがって、製造プロセスにおいてローレット加工を取り入れることは、非常に有益な選択肢となるでしょう。