金属加工の種類/切削加工における金属加工の機械加工とは?
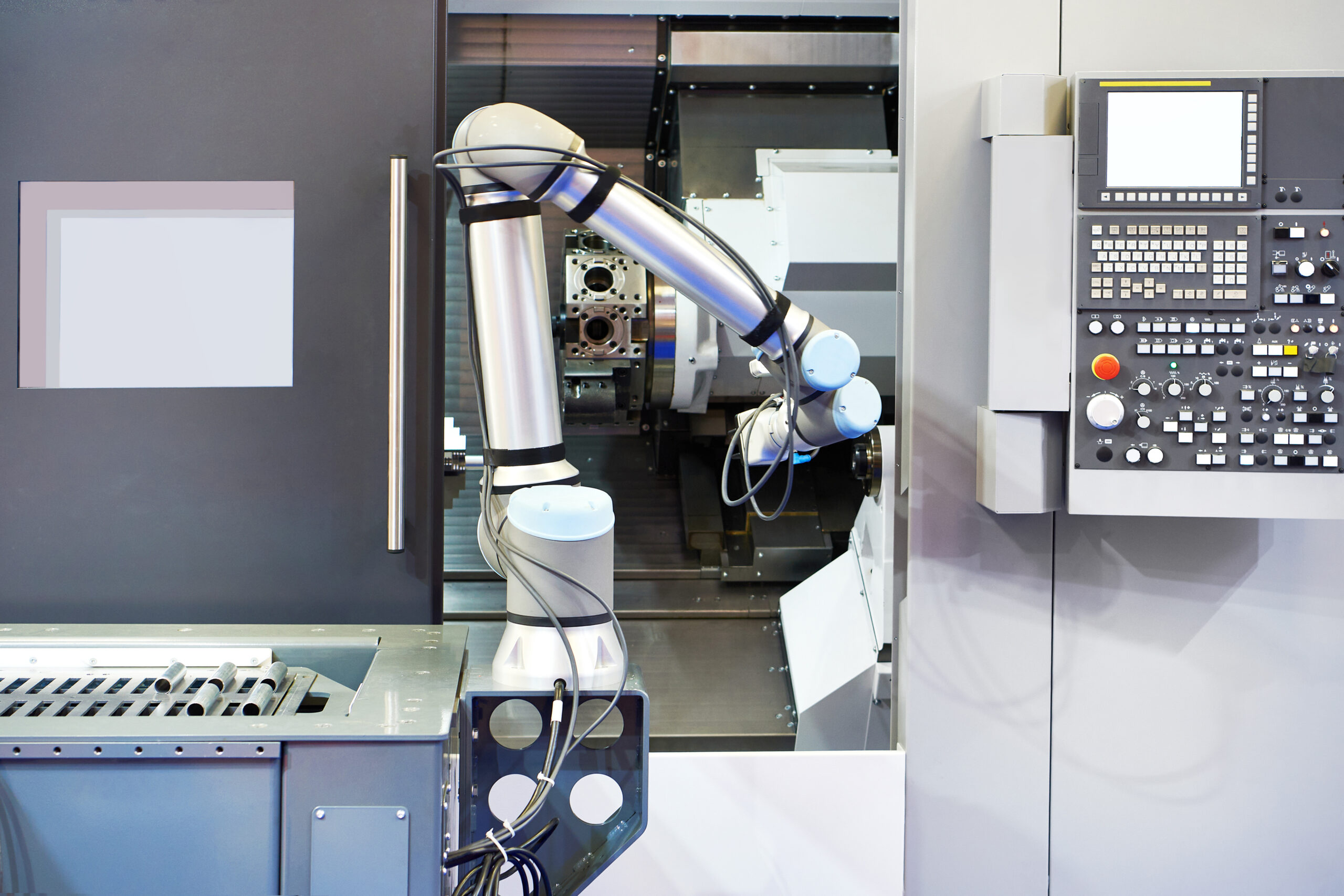
金属加工には様々な種類があり、それぞれが独自の特性を持っています。この記事では、切削加工を中心に、その種類や特徴、加工機械、重要なポイントなどについて詳しく解説していきます。旋削、フライス、穴あけなど、各加工方法の解説に加えて、マシニングセンタやNC旋盤といった加工機械の特徴にも迫ります。
また、切削加工と材料の相性、加工速度、熱管理といった重要な要素についても触れていきます。工作機械の基本や、加工精度と力の関係性についても理解を深め、金属加工の奥深い世界に踏み込みましょう!
切削加工の基本とは|切削加工の種類と特性
切削加工とは、回転する刃物を用いて材料を除去し、所望の形状に加工する方法です。金属加工の中でも最も一般的な方法の一つであり、様々な産業分野で使用されています。
切削加工には、大きく分けてフライス加工、旋盤加工、穴あけ加工、研削加工の4種類があります。
- フライス加工: 回転するフライス盤を用いて、材料の平面や溝、穴などを加工します。
- 旋盤加工: 回転する材料に対してバイトと呼ばれる刃物を当てて、円筒形や球形などの加工を行います。
- 穴あけ加工: ドリルと呼ばれる回転する工具を用いて、材料に穴を開けます。
- 研削加工: 研削砥石と呼ばれる砥石を用いて、材料を微細に削り取って表面を滑らかに仕上げます。
切削加工を行う際には、適切な工具や加工条件を選択することが重要です。また、切削油などの潤滑剤を用いることで、加工精度や工具の寿命を向上させることができます。
このトピックの詳細については、以下のヘッドラインをご覧ください。
- 切削加工の代表的な種類
- 切削加工機械の一覧
- 切削加工における重要なポイント
切削加工の代表的な種類
切削加工は、回転する工具を用いてワークを切削することで所望の形状や寸法に加工する機械加工です。様々な種類があります。
- 旋削加工: 回転するワークに対して工具を送り、円筒や円盤状の形状に加工します。
- フライス加工: 回転する工具を用いて、平面や溝、歯車などの複雑な形状に加工します。
- 穴あけ加工: 回転するドリルを用いて、ワークに穴をあける加工です。
これらの切削加工は、それぞれに特徴があり、加工形状や精度、時間、コストなどの面で異なります。
旋削加工の特徴とは
旋削加工は、切削加工の代表的な種類の1つです。回転する工具を用いて、ワークを回転させながら切削する加工方法です。主に円筒形のワークを加工するのに適しており、軸やシャフト、ボルトなどの製造に広く用いられています。
旋削加工の特徴としては、以下の点が挙げられます。
- 高い精度と再現性を実現できる
- 切削速度が速く、加工時間が短い
- 自動化や無人化が容易
- 複雑な形状の加工にも対応できる
旋削加工は、切削加工の中でも最も基本的な加工方法であり、幅広い分野で活用されています。その汎用性と効率性から、今後もますます重要性が増していくと考えられます。
フライス加工の特異性
フライス加工は、回転する多刃工具を用いて材料を除去する切削加工方法です。工具には複数の刃が取り付けてあり、回転しながら材料表面を削ることで、平坦面、溝、穴などを加工することができます。
フライス加工の特異性は、以下の点にあります。
- 多様性: フライス加工は、多様な形状の加工に対応できる汎用性の高い方法です。平面、溝、穴、さらには複雑な形状の加工も可能です。
- 高精度: フライス加工は、高精度の加工が可能な切削方法です。NC(数値制御)技術と組み合わせることで、μm単位の精度で加工することができます。
- 複雑形状への対応: フライス加工は、複雑な形状の加工にも対応できます。回転する工具を異なる角度で傾けたり、プログラム制御することで、自由曲面や複雑な形状の加工を行うことができます。
- 効率性: フライス加工は、複数刃の工具を使用することで、他の切削加工方法と比較して効率的に材料を除去することができます。
フライス加工は、自動車部品、航空機部品、電子機器など、様々な産業分野で広く用いられています。また、近年では、3Dプリンターやレーザー加工機など、新しい加工技術との組み合わせも進んでいます。
穴あけ加工の特質
穴あけ加工は、ドリルと呼ばれる回転工具を用いて、ワークに穴を開ける加工方法です。様々な機械加工の中でも最も基本的な作業の一つです。穴あけ加工は、以下の特徴があります。
- 多様な用途: 穴あけ加工は、機械部品や電子機器など、様々な製品の製造に使用されます。ネジ穴や軸穴などの穴あけだけでなく、穴を利用した切断や溝加工などにも使用できます。
- 高い精度: 穴あけ加工は、他の加工方法と比較して高い精度が求められることが多いです。特に、精密機器や電子機器の部品加工では、μm単位の精度が要求されます。
- 様々なドリルを使用可能: 穴あけ加工には、様々な種類のドリルが使用されます。サイズや形状、材質などが異なるドリルを選択することで、穴の形状や精度、加工速度などを調整することができます。
- 冷却液の使用: 穴あけ加工では、ドリルとワークの摩擦熱を軽減するために、冷却液が使用されることが多くなります。冷却液は、工具の寿命を延ばし、加工精度を高める効果があります。
- 穴加工の種類が多い: 穴あけ加工には、様々な種類があります。代表的なものとしては、貫通穴加工、底穴加工、段穴加工、袋穴加工などがあります。加工する穴の種類によって、ドリルや加工方法が異なります。
穴あけ加工は、多様な用途と高い精度が求められる加工方法です。様々なドリルを使用することで、加工のニーズに合わせて穴の形状や精度、加工速度などを調整することができます。
切削加工機械の一覧
切削加工は、金属加工において最も一般的な方法であり、回転工具を使用して材料から切りくずを除去することで形状を作成します。切削加工に使用される機械は多種多様であり、それぞれ異なる機能と能力を持っています。
以下は、切削加工機械の代表的な例です。
- マシニングセンタ: 多数の工具と軸を備えた汎用性の高い機械で、複雑な形状の加工に適しています。
- NC旋盤: 回転する材料から切りくずを除去するのに使用される機械で、円筒形や円錐形の形状の加工に適しています。
- 同時5軸加工: 5つの軸を同時に制御できる機械で、複雑な形状の加工を高速かつ高精度で行うことができます。
これらの機械は、それぞれ異なる機能と能力を持っており、加工する形状や材料に合わせて選択されます。それぞれの機械の詳細については、以下の記事で詳しく説明します。
マシニングセンタの特色
マシニングセンタは、フライス加工、穴あけ加工、タップ加工、ボーリング加工、さらには旋盤加工など、さまざまな切削加工を一台の機械で行うことができる多機能な工作機械です。
主な特色:
- 複数の軸を同時に制御することで、複雑な形状の加工を可能にします。
- 高精度な加工を実現するために、高剛性な構造と高性能な制御システムを採用しています。
- 自動工具交換やプログラムによる自動運転が可能で、無人化にも対応できます。
- 多機能でありながら、設置面積が小さく、スペース効率に優れています。
マシニングセンタは、航空機や自動車、医療機器など、幅広い分野で活用されています。特に、複雑な形状や高精度の加工が求められるような製品の製造に適しています。
その他:
- マシニングセンタには、さまざまな種類があり、加工能力や機能によって分類されます。
- マシニングセンタの導入には、設備投資が必要ですが、生産性の向上や加工コストの削減など、さまざまなメリットがあります。
NC旋盤の特性
NC旋盤とは、コンピューター制御によって自動的に旋盤加工を行う工作機械です。従来の旋盤と比較して、以下の特徴を持っています。
- 高精度加工: コンピューター制御により、工具の移動や回転速度などを正確に制御できるため、高精度な加工を実現できます。
- 自動化による効率化: プログラムに従って自動的に加工を行うため、作業者の負担を軽減し、生産効率を向上させることができます。
- 複雑な形状への対応: NC旋盤は、複雑な形状の加工にも対応できます。これは、工具の移動や回転速度などを自由にプログラムできるためです。
- 加工時間の短縮: プログラムに従って自動的に加工を行うため、加工時間を短縮できます。
- 安定した加工品質: コンピューター制御により、毎回同じ加工品質を確保できます。
NC旋盤は、自動車部品や機械部品などの製造に幅広く活用されています。特に、複雑な形状の部品や、大量生産が必要な部品の加工に適しています。
同時5軸加工の特徴
同時5軸加工は、3軸加工と比較して、複雑な形状の加工や難しい切削加工を効率的に行うことができます。
3軸加工と同時5軸加工の特徴は次のとおりです。
項目 | 3軸加工 | 同時5軸加工 |
---|---|---|
軸数 | 3軸 | 5軸 |
加工可能形状 | 比較的単純な形状 | 複雑な形状 |
工具の動き | 3軸方向 (X, Y, Z) | 5軸方向 (X, Y, Z, A, B) |
加工時間 | 長い | 短い |
切削精度 | 精度が低い | 精度が高い |
加工コスト | 高い | 低い |
同時5軸加工の特徴は次のとおりです。
- 複雑な形状の加工が可能: 同時5軸加工では、5つの軸を同時に制御することで、複雑な形状の加工が可能です。
- 切削時間の短縮: 同時5軸加工では、工具を最適な角度で加工することができるため、切削時間を短縮することができます。
- 切削精度の向上: 同時5軸加工では、工具の角度を正確に制御することで、切削精度を向上させることができます。
- 加工コストの削減: 同時5軸加工では、切削時間の短縮と切削精度の向上により、加工コストを削減することができます。
同時5軸加工は、航空宇宙産業や自動車産業など、複雑な形状の加工が必要な産業で広く使用されています。
切削加工における重要なポイント
切削加工は、回転する工具を用いて材料を削り取る加工方法です。金属加工において最も一般的な方法の一つであり、複雑な形状の部品を高い精度で加工することができます。
切削加工において重要なポイントは、以下の3つです。
- 切削加工と材料の相性: 切削加工は、加工する材料との相性によって、加工のしやすさが異なります。硬い材料や粘り強い材料は加工が難しく、切削工具の摩耗が早くなります。
- 切削加工と加工速度: 切削速度は、加工の効率に大きく影響します。切削速度が速すぎると、切削工具が破損したり、加工精度が低下したりする可能性があります。
- 切削加工と熱の管理: 切削加工では、摩擦熱が発生します。この熱は、加工精度や切削工具の寿命に影響を与えます。そのため、切削加工では、適切な冷却方法を用いて熱を管理することが重要です。
これらのポイントを抑えることで、効率的で高品質な切削加工を行うことができます。
次のセクションでは、それぞれについて詳しく説明します。
切削加工と材料の相性
切削加工において、加工精度や効率を左右する重要なポイントの一つが、切削加工と材料の相性です。材料と切削条件の組み合わせによって、加工のしやすさや仕上がり精度が大きく異なるため、最適な組み合わせを選択することが求められます。
ここで、材料の代表的な分類と切削加工との相性をリストアップします。
- 鉄鋼材料:鉄鋼材料は、切削加工の代表的な材料の一つであり、比較的加工しやすい性質を持っています。しかし、硬度や炭素含有量によって加工性が変化するため、切削条件の調整が必要となります。
- アルミニウム合金:アルミニウム合金は、軽量で耐食性に優れていることから、航空機や自動車部品など幅広い分野で利用されています。切削加工においても比較的加工しやすい材料ですが、加工時に粘りが出やすく、工具摩耗が進行しやすい傾向があります。
- ステンレス鋼:ステンレス鋼は、耐食性と強度を兼ね備えていることから、建築資材や医療機器など幅広い分野で利用されています。硬度が高く、切削加工に時間を要する傾向がありますが、専用の工具や切削条件を用いることで効率的な加工が可能です。
- チタン合金:チタン合金は、軽量で高強度、耐食性に優れていることから、航空機や宇宙開発など厳しい環境で使用される部品に多く用いられています。硬度が高く、切削加工が難しい材料の一つですが、専用の工具や切削条件を用いることで加工が可能です。
- 樹脂材料:樹脂材料は、軽量で成形性に優れていることから、様々な分野で利用されています。切削加工においては、比較的加工しやすい材料ですが、熱に弱い性質があるため、加工時に熱の影響を考慮する必要があります。
このように、材料の特性によって切削加工のしやすさは異なるため、加工条件や工具の選択を適切に行うことが重要です。また、材料と切削加工との相性を考慮することで、加工精度や効率を向上させることができます。
切削加工と加工速度
切削加工は、ワークに対して相対的に移動する刃物を使用して材料を切断する加工方法です。加工速度は、切削工具の送り速度と回転速度によって決まります。送り速度は、切削工具が1分間に移動する距離であり、回転速度は、切削工具が1分間に回転する回数です。
加工速度は、切削加工の効率と品質に大きな影響を与えます。速度が速すぎると、切削工具が摩耗したり破損したりする可能性があります。また、表面仕上げが悪くなったり、ワークが変形したりする可能性もあります。速度が遅すぎると、加工時間が長くなり、生産性が低下します。
適切な加工速度を選択するには、加工する材料、使用する切削工具、切削深さ、切削幅などのさまざまな要因を考慮する必要があります。切削工具のメーカーは、特定の工具と材料の組み合わせに推奨される加工速度を提供しています。
切削加工には、さまざまな速度が使用されます。たとえば、アルミニウムなどの軟質材料は、鋼などの硬質材料よりも高速で切削できます。また、小径工具は、大径工具よりも高速で切削できます。
適切な加工速度を選択することが、切削加工を効率的かつ効果的に行うために重要です。速度が速すぎても遅すぎても、切削工具の寿命、表面仕上げ、ワークの品質に悪影響を及ぼす可能性があります。
切削加工と熱の管理
切削加工において、熱の管理は重要なポイントです。切削加工では、工具とワークピースの摩擦によって熱が発生します。この熱は、工具の摩耗やワークピースの変形を引き起こす可能性があります。
熱を管理するために、切削液を使用することがあります。切削液は、工具とワークピースを冷却し、摩擦を軽減します。また、切削液は、切り屑を洗い流す役割も果たします。
熱を管理するための他の方法としては、切削速度や送り速度を調整することがあります。切削速度とは、工具の回転速度のことです。送り速度とは、工具の移動速度のことです。切削速度や送り速度を下げることで、発生する熱の量を減らすことができます。
切削加工の熱の管理は、工具の寿命とワークピースの品質に大きな影響を与えます。切削加工を行う際には、熱の管理を適切に行うことが重要です。
工作機械の基本を理解する
切削加工は、回転する刃物で素材を削り取って加工する方法です。切削加工には、旋削加工、フライス加工、穴あけ加工などがあります。
旋削加工は、円筒状の素材を回転させながら刃物で削り取る加工方法です。フライス加工は、回転する刃物で素材を削り取る加工方法です。穴あけ加工は、回転する刃物で素材に穴を開ける加工方法です。
工作機械には、それぞれに特徴があります。マシニングセンタは、旋削加工や穴あけ加工など、様々な加工を一台でできる多機能な工作機械です。NC旋盤は、プログラム制御によって自動的に旋削加工を行う工作機械です。同時5軸加工は、5つの軸を同時に制御して複雑な形状を加工できる工作機械です。
切削加工を行う際には、加工条件や加工方法を適切に選択する必要があります。切削加工と材料の相性、切削加工と加工速度、切削加工と熱の管理などが重要です。加工条件や加工方法を適切に選択することで、高品質な製品を効率的に生産することができます。
加工精度と力の関係性
加工精度とは、加工された製品が設計図通りの形状や寸法にどれだけ正確に仕上がっているかを示す指標です。加工精度に影響を与える要因は多くありますが、その中でも重要なのが加工時に発生する力です。
加工時に発生する力は、加工物の変形や工具の摩耗など、様々な問題を引き起こす可能性があります。加工物の変形は、製品の寸法や形状が設計図通りにならない原因となります。また、工具の摩耗は、加工精度が悪化したり、工具の寿命が短くなったりする原因となります。
そこで、加工精度を向上させるためには、加工時に発生する力を適切に制御することが重要です。加工時に発生する力を制御するためには、剛性の高い工作機械を使用したり、加工条件を最適化したりすることが必要です。
剛性とは、物体が変形しにくい性質のことです。剛性の高い工作機械は、加工時に発生する力に対して変形しにくいため、加工精度を向上させることができます。加工条件の最適化とは、加工速度や送り速度、切削深さなどを最適な値に設定することです。加工条件を最適化することで、加工時に発生する力を最小限に抑えることができます。
このように、加工精度と力の関係性は非常に重要です。加工精度を向上させるためには、加工時に発生する力を適切に制御することが必要です。加工時に発生する力を制御するためには、剛性の高い工作機械を使用したり、加工条件を最適化したりすることが必要です。
【1】剛性とは何か
切削加工における重要なポイントとして、剛性が挙げられます。これは、加工物の変形に対する抵抗力を指し、高いほど加工精度が向上します。剛性の低い加工物では、切削工具の力が加わることで変形が生じ、寸法誤差や表面粗さに悪影響を及ぼします。特に、薄肉の加工物や複雑形状のものは、剛性が低下しやすいため注意が必要です。
剛性を確保するためのポイントは以下の通りです。
- 加工速度の調整: 高速加工を行う場合は、切削力が大きくなるため、適切な加工速度の設定が必要です。
- 送り速度の調整: 送り速度が速いほど、工具に大きな力が加わるため、適切な速度の設定が必要です。
- 工具の選定: 工具の強度や剛性に応じて、加工条件の調整を行う必要があります。
- 工作機械の剛性確保: 機械本体の剛性を確保することで、加工物の変形を抑えることができます。
切削加工における剛性は、加工精度向上に不可欠な要素です。剛性の確保によって、寸法誤差や表面粗さを低減し、高品質な製品の製造が可能となります。
【2】変形の影響とは
加工精度と力の関係性について説明します。
加工精度とは、加工された製品の寸法や形状が設計通りの値にどれだけ近づいているかを示す指標です。力の関係性とは、加工時に加える力と加工精度との相関関係のことです。
切削加工では、工具が材料を切削する際に力が必要となります。この力は切削力と呼ばれ、その大きさは加工条件や材料の種類によって異なります。切削力が大きすぎると、材料が塑性変形を起こし、加工精度が悪化します。逆に切削力が小さすぎると、切削がうまくいかず、バリが発生したり、工具が摩耗したりするおそれがあります。
切削加工における力の関係性は、加工精度を高めるために重要なポイントです。適切な切削力を設定することで、加工精度を向上させることができます。切削力は、以下の要因によって影響を受けます。
- 切削速度: 切削速度とは、工具が材料を切削する速度のことです。切削速度が速いほど、切削力も大きくなります。
- 送り速度: 送り速度とは、工具が材料に食いつく速度のことです。送り速度が速いほど、切削力も大きくなります。
- 工具の切れ味: 工具の切れ味が悪いと、切削力も大きくなります。
- 材料の種類: 材料の種類によって、切削力も異なります。
加工精度を高めるためには、これらの要因を考慮して適切な切削力を設定する必要があります。また、加工条件や材料の種類によって切削力は異なるため、事前に加工実験などを行い、最適な切削条件を決定することが重要です。
まとめ
切削加工は、金属加工の中でも最も基本的な加工方法の一つです。切削工具を用いて材料を削り取り、所望の形状に加工します。切削加工にはさまざまな種類があり、それぞれに特徴があります。代表的な種類としては、旋削加工、フライス加工、穴あけ加工などがあります。
切削加工に使用する機械には、マシニングセンタ、NC旋盤、5軸加工機などがあります。これらの機械は、コンピュータ制御によって複雑な形状の加工も可能です。
切削加工を行う際には、切削工具と材料の相性、加工速度、熱の管理など、さまざまなポイントに注意する必要があります。切削工具と材料の相性は、加工精度や効率に影響します。加工速度は、加工時間と加工品質に影響します。熱の管理は、加工精度と工具寿命に影響します。
切削加工は、さまざまな製品の製造に用いられています。機械部品、自動車部品、航空機部品など、さまざまな製品の製造に必要不可欠な加工方法です。