研磨加工の基礎知識 種類と手順を解説
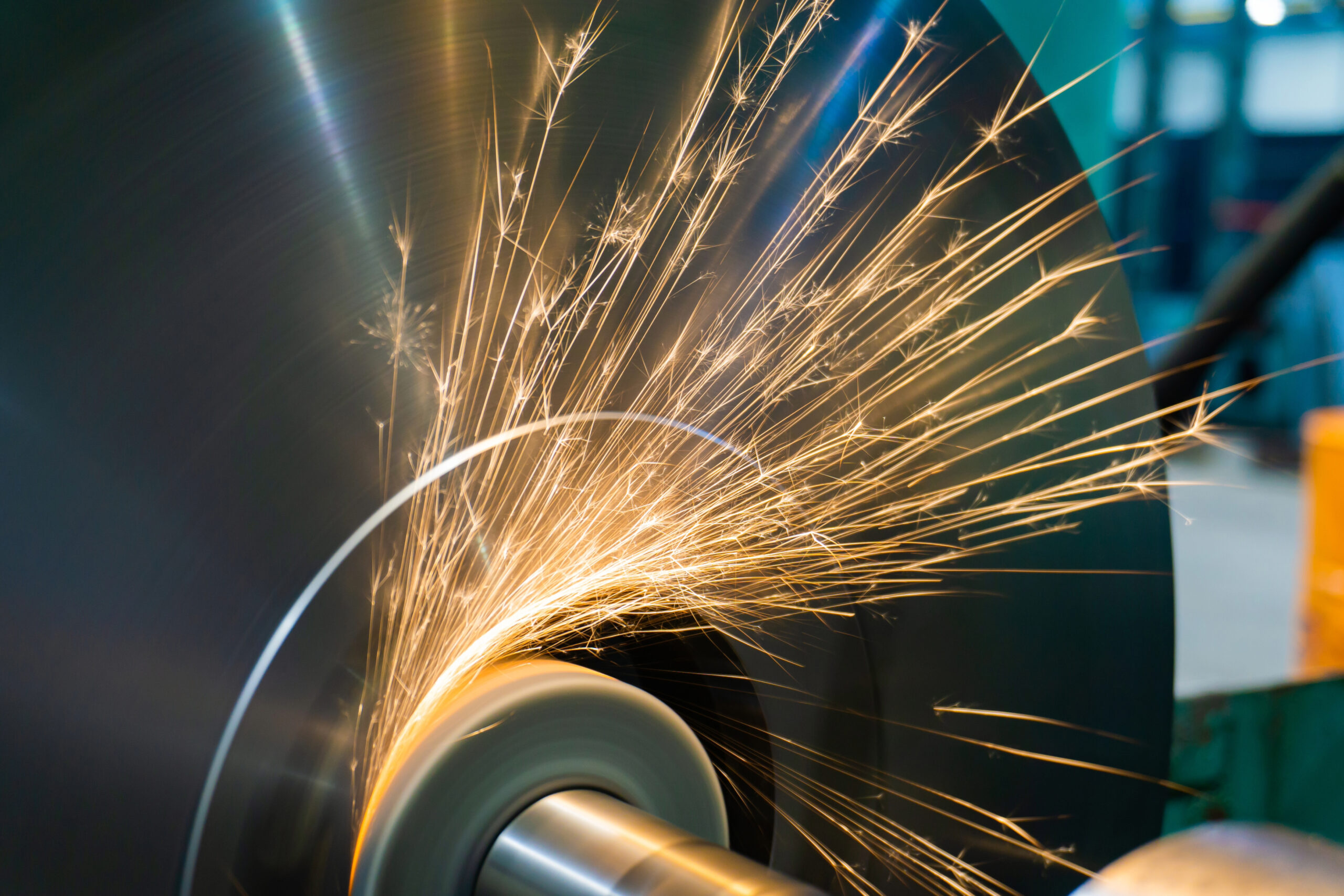
研磨加工は、砥石などの研磨材を用いて材料表面を削り、平滑に仕上げる加工方法です。研磨加工は、研削加工と研磨加工に分類され、前者は機械加工の一種で、後者は研削加工を含まない方法です。
研磨加工には、砥石による研磨、ラッピング、バフ研磨、バレル研磨、電解研磨などがあります。各手法は、用途や目的によって使い分けられます。
研磨加工の手順は、下地処理、ならし、つや出し、鏡面仕上げの順に行われます。各工程では、適切な砥粒や機械を使用することが重要です。
砥粒は、ダイヤモンド、アルミナ、炭化ケイ素、CBNなどの種類があり、それぞれ特性が異なります。研磨加工では、これらの特性を考慮して砥粒を選択する必要があります。
研磨加工は、表面仕上げと密接な関係があります。適切な研磨加工を行うことで、鏡面のような滑らかな表面を得ることができます。
研磨加工の基本
研磨加工は、砥石や研磨剤を用いてワークの表面を削り、平滑性や形状精度を高める加工方法です。研削加工とは、砥粒の突出量が少ない砥石を用いて仕上げを行うのに対し、研削加工は砥粒の突出量が多い砥石を用いて切削加工を行う点が異なります。
研磨加工の種類には、砥石を使った研磨、ラッピング研磨、バフ研磨、バレル研磨、電解研磨などがあります。研磨加工の手順は、下地処理、ならし、つや出し、鏡面仕上げの4段階に分かれます。下地処理は、研磨を行う前にワークの表面の汚れや傷を取り除く作業です。ならしは、砥石を使ってワークの形状を整える作業です。つや出しは、バフを使ってワークの表面に光沢を出す作業です。鏡面仕上げは、さらに細かい砥石を使ってワークの表面を鏡のように滑らかにする作業です。
研磨加工の品質は、砥石の種類や特性、研磨剤の種類や粒度、研磨速度、研磨圧力など様々な要素によって決まります。適切な条件を選択することで、必要な平滑性や形状精度を達成することができます。
研磨加工と研削加工の違いについて
研磨加工と研削加工は、どちらも表面を加工してなめらかにする加工方法ですが、いくつかの違いがあります。
研磨加工は、砥石や研磨剤などの微粒子が切削工具として用いられる加工方法です。砥石や研磨剤は、被加工物を押さえつけながら回転させたり、往復運動させたりすることで、被加工物の表面を削り取ります。研磨加工は、主に鉄などの金属やセラミックスなどの硬い素材の加工に用いられます。
研削加工は、砥石が切削工具として用いられる加工方法です。砥石は、高速に回転させながら被加工物を削り取ります。研削加工は、主に鉄やアルミニウムなどの金属の加工に用いられます。
研磨加工と研削加工の主な違いは以下の表のとおりです。
特徴 | 研磨加工 | 研削加工 |
---|---|---|
切削工具 | 砥石や研磨剤 | 砥石 |
加工速度 | 遅い | 速い |
適用素材 | 金属、セラミックス | 金属 |
加工精度 | 高い | 低い |
表面粗さ | 細かい | 粗い |
研磨加工と研削加工は、どちらも表面を加工してなめらかにする加工方法ですが、切削工具や加工速度、適用素材などの違いがあります。加工する素材や求められる精度によって、どちらの加工方法を選択すればよいかを判断する必要があります。
研磨加工の種類一覧
研磨加工には様々な種類があり、それぞれ特徴や用途が異なります。以下に、代表的な研磨加工の種類を箇条書きでまとめました。
- 砥石を使った研磨: 回転する砥石を用いて素材表面を削り取る方法。
- ラッピング研磨: 研磨剤を塗布した平面プレート上で素材を押し付け、研磨する方法。
- バフ研磨: 回転する布バフに研磨剤を塗布し、素材表面を磨く方法。
- バレル研磨: 研磨材と素材をバレルに入れて回転させ、摩擦で研磨する方法。
- 電解研磨: 電解液中で電流を流すことで素材表面を溶解・研磨する方法。
それぞれの研磨加工方法については、以下の項目で詳しく解説します。
砥石を使った研磨
砥石を使った研磨は、最も基本的な研磨方法の一つです。砥石は、硬い鉱物やセラミックでできており、研磨剤として使用されます。研磨剤の粒径によって、粗研ぎから仕上げ研ぎまで様々な用途に使用することができます。砥石は、手動で操作するタイプと電動で操作するタイプがあります。手動で操作するタイプは、砥石を回転させながら研磨対象を押し当てて研磨します。電動で操作するタイプは、砥石が回転している状態に研磨対象を押し付けて研磨します。
砥石を使った研磨は、比較的簡単な方法ですが、技術が必要です。研磨の際には、砥石の角度や圧力、速度を適切に調整する必要があります。また、砥石の粒径も研磨対象に合わせて選択する必要があります。
砥石を使った研磨のメリットは、コストが比較的安いことです。また、様々な用途に使用できることもメリットです。しかし、砥石を使った研磨は時間がかかることがデメリットです。また、技術が必要なため、失敗することもあります。
砥石を使った研磨の際には、以下の点に注意が必要です。
- 砥石の角度や圧力、速度を適切に調整する
- 砥石の粒径を研磨対象に合わせて選択する
- 安全に作業を行う
ラッピング研磨の手法
ラップ研磨は、平面度や parallelism を必要とする精密部品の研磨に適した手法です。研磨剤を含浸させた布や紙を研磨台に巻き付け、ワークを押し当てながら回転させることで研磨を行います。
ラップ研磨は、高い平面度と parallelism が得られる、鏡面仕上げまで仕上げることができる、ワークへのダメージが少ないという利点があります。一方で、加工時間が長い、高価な研磨剤が必要、熟練した技術が必要という欠点もあります。
ラップ研磨は、光学レンズ、半導体ウエハー、金型、精密機器の部品など、高い精度が要求される部品の研磨に適した手法です。ただし、加工時間が長く、コストがかかるため、他の研磨方法と比較してコストパフォーマンスが劣る場合があります。
バフ研磨の特徴
バフ研磨は、研磨剤としてバフと呼ばれる柔らかい素材の円盤を使用する研磨方法です。バフは、布、毛皮、フェルトなどの素材で作られており、回転させながら研磨剤を塗布したワークに押し当てて研磨します。
バフ研磨は、以下の特徴があります。
- 高精度な研磨が可能
- 表面を傷つけにくい
- 鏡面仕上げにも対応できる
- 複雑な形状の研磨にも適している
バフ研磨は、鏡面仕上げや精密部品の研磨など、高い精度が求められる研磨に適しています。また、柔らかいバフを使用するため、ワークの表面を傷つけにくいというメリットがあります。
バフ研磨の欠点は、研削加工に比べて研磨速度が遅いことです。また、バフの素材や研磨剤によって研磨結果が異なるため、経験や技術が必要となります。
バレル研磨の手順
バレル研磨は、多くの部品を同時に処理できるため、大量生産に適した研磨方法です。以下の手順で実施されます。
- バレルへの投入: バレルに研磨対象の部品と研磨材、研磨液を入れます。
- バレルの回転: バレルを回転させます。回転によって、研磨材と研磨液が部品に当たり、研磨されます。
- 洗浄: バレルの回転を停止し、部品を取り出します。その後、部品を洗浄して研磨材や研磨液を取り除きます。
- 乾燥: 洗浄した部品を乾燥させます。
バレル研磨は、比較的簡単な方法ですが、以下の点に注意が必要です。
- 研磨材の選択: 研磨材は、研磨対象の材質や形状に合わせて選択する必要があります。
- 研磨液の選択: 研磨液は、研磨材や研磨対象の材質に合わせて選択する必要があります。
- バレルの回転速度: バレルの回転速度は、研磨対象の材質や形状に合わせて調整する必要があります。
- 研磨時間: 研磨時間は、研磨対象の材質や形状、desired surface finish を考慮して調整する必要があります。
電解研磨の方法
電解研磨は、電解液中で金属をアノードとして電流を流すことで金属表面を溶解させ、表面を平滑化させる加工方法です。研磨加工の中でも高精度な加工が可能で、複雑な形状の部品や微細な加工にも適しています。
電解研磨の主な利点としては、以下の点が挙げられます。
- 高精度な加工が可能: 電解液中のイオンが金属表面を均一に溶解させるため、高精度な加工が可能です。
- 複雑な形状の加工が可能: 電解液は複雑な形状にも浸透するため、複雑な形状の部品の加工にも適しています。
- 微細な加工が可能: 電流密度を調整することで、微細な加工も可能です。
- 研磨熱が発生しない: 電解液が熱を吸収するため、研磨熱が発生せず、変形や焼入れなどの影響を最小限に抑えることができます。
一方で、以下の点には注意が必要です。
- 加工できる材料が限定される: 電解研磨は、電気を通す金属のみ加工可能です。
- 設備コストが高い: 電解研磨には専用の設備が必要となるため、設備コストが高くなります。
- 安全対策が必要: 電解液は腐食性があるため、安全対策が必要です。
電解研磨は、高精度な加工が必要な部品や複雑な形状の部品の加工、微細な加工に適した方法です。ただし、加工できる材料が限定されることや設備コストが高いこと、安全対策が必要であることに注意が必要です。
研磨加工の手順と工程
研磨加工は、金属や樹脂などの表面を削り取って形状を整えたり、表面の品質を向上させる加工方法です。代表的な手順と工程を紹介します。
- 下地処理: 研磨加工を始める前に、表面に付着している汚れや錆などを除去することが重要です。ワイヤーブラシやサンドペーパーなどを使用して、表面をきれいにします。
- ならし作業: 表面の大きな凹凸を平滑にするために、粗目の砥石を使用してならし作業を行います。この工程は、仕上がりの精度を高めるために欠かせません。
- つや出し: ならし作業が終わったら、つや出し作業を行います。この工程では、細かい傷や凹凸を消して表面に光沢を出すことが目的です。
- 鏡面仕上げ: さらに表面を滑らかにし、鏡のような光沢を出すためには、鏡面仕上げを行います。この工程では、超微粒子の砥石を使用し、丁寧に磨きます。
- 砥石研磨での水使用: 砥石研磨では、水を使用することが一般的です。水は、砥石の冷却と研磨粉の除去を促進します。また、砥石の目詰まりを防ぎ、研削効率を高めます。
これらの工程を経て、研磨加工は完了します。各工程の詳細は、後述のネストされているヘッドラインで詳しく紹介しています。
下地処理の重要性
研磨加工を行う前に、下地処理を行うことで、以下のメリットが得られます。
- 研磨加工後の表面を平坦化し、仕上がりを向上させる。
- 研磨加工の効率を向上させる。
- 研磨加工後の表面の傷や凹凸を軽減する。
下地処理には、様々な方法があります。代表的な方法としては、研磨、サンドブラスト、化学研磨などがあります。下地処理の方法は、研磨加工の目的や材料によって異なります。
研磨加工を行う前に、適切な下地処理を行うことで、仕上がりの向上や研磨効率の向上を図ることができます。
ならし作業の手順
研磨加工において最初に実施される工程がならし作業です。この工程は、砥石の表面を整え、切削力を安定させ、加工面の精度を高めることを目的としています。以下の手順で行います。
- 砥石の整形: ダイヤモンド砥石を用いて、砥石の表面を平坦に整えます。
- ドレッシング: ドレッシング工具を用いて、砥石の表面に細かい溝を形成します。この溝によって、切削時に砥石とワークの間に切粉が溜まりにくくなり、切削力を安定させます。
- 荒砥ぎ: 粗い砥石を用いて、ワークの表面を荒く削ります。この工程では、ワークの形状を整え、大きなバリを取り除きます。
- 中砥ぎ: 荒砥ぎよりも細かい砥石を用いて、ワークの表面をより滑らかに仕上げます。
- 仕上げ砥ぎ: 最も細かい砥石を用いて、ワークの表面を鏡面仕上げレベルまで仕上げます。
ならし作業は、研磨加工の精度を左右する重要な工程です。適切な手順で行うことで、高精度な加工を実現することができます。
つや出しのプロセス
つや出しとは、表面を滑らかに研磨し、光沢を出すための仕上げ工程です。研磨加工の最終段階として行われることが多く、鏡面仕上げのように金属が鏡のように光る状態にすることも可能です。
つや出しには様々な方法がありますが、代表的なものとして以下の3つがあります。
- バフ研磨:柔らかいバフと研磨剤を用いて、表面を磨きます。鏡面仕上げにも対応できる方法です。
- 化学研磨:薬品を用いて表面を溶解し、光沢を出します。複雑な形状にも対応できますが、環境への配慮が必要となります。
- 電解研磨:電解液を用いて表面を溶解し、光沢を出します。化学研磨よりも環境に優しい方法です。
つや出しの具体的な手順は、以下の通りです。
- 下地処理:表面を平滑化し、傷や汚れを落とします。
- 粗研磨:粗い砥石や研磨剤を用いて、表面をある程度まで研磨します。
- 中研磨:より細かい砥石や研磨剤を用いて、表面をさらに研磨します。
- 仕上げ研磨:非常に細かい砥石や研磨剤を用いて、表面を滑らかに磨きます。
- つや出し:バフや薬品、電解液を用いて、表面を光沢を出します。
つや出しは、製品の美観や耐食性、滑り性を向上させる効果があります。また、表面の汚れが付着しにくくなるため、メンテナンスが容易になります。
鏡面仕上げの手法
鏡面仕上げは、研磨加工の種類の1つで、表面を非常に滑らかにする仕上げ方法です。研磨剤やバフを使用して、表面の凸凹を削り取ることによって、鏡のように光沢のある表面に仕上げます。
镜面仕上げの用途は多岐にわたります。例えば、自動車やバイクのボディ、金属製品、レンズ、鏡、金型など、様々な製品の表面に使用されます。鏡面仕上げを施すことで、製品の外観を向上させたり、耐食性や耐摩耗性を高めたりすることができます。
鏡面仕上げを行うには、いくつかの手順が必要です。まず、表面の汚れや傷を研磨剤を使用して取り除きます。次に、より細かい研磨剤を使用して表面をさらに滑らかにします。最後に、バフを使用して表面を研磨することで、鏡のように光沢のある表面に仕上げます。
鏡面仕上げの品質は、表面の粗さや光沢によって評価されます。表面の粗さは、表面の凹凸の大きさを表す指標です。表面の光沢は、表面がどれだけ光を反射するかを表す指標です。
鏡面仕上げを行うには、技術と経験が必要です。また、鏡面仕上げの品質は、使用する研磨剤やバフの種類、作業者の技術などによって左右されます。
砥石研磨での水使用の理由
砥石研磨では、研削力を高め、研削熱を冷却するために水が使用されます。水は、砥石とワークの間に潤滑剤として働き、摩擦を軽減し、熱を発生させます。水はまた、研削屑を洗い流す役割も果たし、ワークの表面をきれいに保ちます。
砥石研磨では、水の種類と量を適切に選択することが重要です。水が多すぎると、研削力が低下し、ワークの表面が波打つことがあります。逆に、水が少ないと、研削熱が上昇し、ワークが焼けたり、変形したりする可能性があります。
砥石研磨で使用する水の量は、砥石の粒度、ワークの材質、研削速度などによって異なります。一般的には、砥石の粒度が細かいほど、水の量は少なくなり、ワークの材質が硬いほど、水の量は多くなります。
砥石研磨で水を使用する主な理由を以下に示します。
- 研削力を高める
- 研削熱を冷却する
- 研削屑を洗い流す
適切な水の種類と量を選択することで、砥石研磨の効率と品質を向上させることができます。
砥石は、研磨剤として使用される多孔質の岩石です。砥石には、天然砥石と人造砥石の2種類があります。天然砥石は、自然界で産出される岩石で、人造砥石は人工的に製造された砥石です。
砥石には、粒度、硬度、結合剤の種類など、さまざまな特性があります。粒度は、砥石の表面の粗さを表し、数字が小さいほど粒度が粗くなります。硬度は、砥石の硬さを表し、数字が大きいほど硬度が高くなります。結合剤は、砥石の粒を固めるために使用される物質です。
砥石の特性は、研磨加工に大きな影響を与えます。粒度の細かい砥石は、表面を滑らかに仕上げるのに適していますが、研削力が弱いため、硬い材料の研磨には適していません。粒度の粗い砥石は、研削力が強いですが、表面が粗くなるため、仕上げには適していません。硬度の高い砥石は、硬い材料の研磨に適していますが、研削力が弱いため、柔らかい材料の研磨には適していません。結合剤の種類は、砥石の形状や研削力を変化させることができます。
砥石の特性を理解することで、適切な砥石を選択し、効率的な研磨加工を行うことができます。
砥粒の種類と特性
研磨加工は、研磨砥粒を用いて材料表面を削り取って形状や表面粗さを整える加工方法です。研磨加工には、ダイヤモンド、アルミナ、炭化ケイ素、CBN(立方晶窒化ホウ素)など、硬さや靭性、耐摩耗性などの特性が異なる様々な種類の砥粒が用いられます。
それぞれの砥粒は用途や加工条件によって使い分けられます。ダイヤモンド砥粒は硬度が高く研削力が強い、アルミナ砥粒はコストが安く汎用性に優れている、炭化ケイ素はダイヤモンドに次ぐ硬度を持ち切削性が良い、CBN砥粒は高温硬度が高く硬い材料の研削に適しているなど、それぞれの砥粒には特徴があります。
砥粒の種類と特性について理解したら、研磨加工の種類や手順について解説します。研磨加工には、平面研削、円筒研削、内面研削など、加工対象や形状によって様々な種類があります。また、研磨加工の手順には、砥石の選択、切削条件の設定、研削加工の実施、仕上げ研磨など、いくつかのステップが含まれます。
研磨加工を行う際には、砥石の選択、切削条件の設定、研削加工の実施、仕上げ研磨など、いくつかのステップが必要です。また、研磨加工には、安全に作業を進めるために注意すべき点があります。例えば、適切な保護具を着用する、砥石の回転方向に注意する、切削条件を正しく設定するなど、安全に作業を進めるために必要な注意点があります。
これらの解説を読むことで、研磨加工に対する理解が深まります。
ダイヤモンド砥粒の特徴
ダイヤモンド砥粒は、研磨加工に用いられる砥粒の中で最も硬度が高く、研削力に優れています。また、耐摩耗性にも優れており、形状が崩れにくいため、長期間の使用が可能です。
ダイヤモンド砥粒は、主に以下の利点があります。
- 高い研削力: ダイヤモンド砥粒は、他の砥粒よりも硬度が高いため、非常に高い研削力を発揮します。
- 優れた耐摩耗性: ダイヤモンド砥粒は、摩耗しにくいため、形状が崩れにくく、長期間の使用が可能です。
- 高い形状保持性: ダイヤモンド砥粒は、形状が崩れにくいため、安定した研磨加工を行うことができます。
- 幅広い用途: ダイヤモンド砥粒は、ガラス、セラミックス、金属など、様々な素材の研磨に用いることができます。
しかし、ダイヤモンド砥粒は高価であるため、コストを抑える必要がある場合は、他の砥粒を使用することがあります。
また、ダイヤモンド砥粒は脆いため、衝撃に弱いという欠点もあります。
アルミナ砥粒の用途
アルミナ砥粒は、切削性と耐久性のバランスに優れているため、さまざまな研磨用途に使用されています。
<切削工具>
アルミナ砥粒は、砥石、切断砥石、研削砥石など、切削工具の製造に使用されています。これらの工具は、金属や他の材料の切削や研削に使用されます。
<研磨剤>
アルミナ砥粒は、研磨剤としても使用されており、研磨ペースト、研磨布、研磨ベルトなどに使用されています。これらの研磨剤は、表面の光沢や平滑性を向上させるために使用されます。
<研磨材>
アルミナ砥粒は、研磨材としても使用されており、研磨剤の硬度と切削性を調整するために使用されています。研磨剤は、金属や他の材料の表面を研磨するために使用されます。
<表面処理>
アルミナ砥粒は、表面処理にも使用されており、表面の平滑化や光沢の向上に使用されます。この処理は、金属や他の材料の外観や性能を向上させるために使用されます。
<アルミナ砥粒の主な特徴>
- 高硬度
- 高切削性
- 高耐久性
- 耐熱性
- 低コスト
アルミナ砥粒は、硬度、粒度、結晶構造などによって特性が異なるため、用途に合わせて適切なものを選択することが重要です。
アルミナ砥粒は、研磨加工に幅広く使用されており、さまざまな産業で重要な役割を果たしています。その切削性、耐久性、コストパフォーマンスのバランスが、さまざまな用途への適用を可能にしています。
炭化ケイ素の特性
炭化ケイ素は、研削加工に用いられる砥粒として広く使用されている材料です。その優れた特性により、様々な用途で高い性能を発揮しています。
炭化ケイ素はダイヤモンドに次ぐ硬度を持ち、硬い材料の研削に適しています。また、高温に強く、熱による性能低下が起きにくい性質を持っています。さらに、摩耗に強く、長期間使用しても研削力が低下しにくいのが特徴です。そして、化学的に安定しており、酸やアルカリなどの薬品にも強い性質を持っています。
炭化ケイ素は、その優れた特性から、以下の用途で広く使用されています。
- 砥石: 砥石の砥粒として使用され、金属、セラミック、ガラスなどの研削に用いられます。
- 研削材: 研削材として使用され、研削加工や研磨加工に用いられます。
- 耐摩耗性部品: 耐摩耗性部品として使用され、機械部品や工具に使用されます。
炭化ケイ素には、以下の種類があります。
- グリーンカーバイド: 最も一般的な炭化ケイ素で、研削材や砥石に使用されます。
- ブラックカーバイド: グリーンカーバイドよりも硬度が高く、研削材や耐摩耗性部品に使用されます。
- 立方晶窒化ホウ素 (CBN): 炭化ケイ素よりも硬度が高く、超硬合金やセラミックの研削に使用されます。
炭化ケイ素は、その優れた特性から、様々な用途で広く使用されています。今後も、研削加工や研磨加工において重要な役割を果たしていくでしょう。
CBN(立方晶窒化ホウ素)の特徴
CBN(立方晶窒化ホウ素)は、ダイヤモンドに次ぐ硬度を持つ超硬材料です。その硬度はダイヤモンドの約40%に達し、優れた耐摩耗性と耐熱性を備えています。また、化学的にも安定しており、酸化や腐食に強いことが特長です。
CBNは、以下の用途で広く使用されています。
- 高硬度材料の切削加工
- 研削工具の研磨剤
- 耐摩耗性部品の材料
CBNの主な特長をまとめると以下のとおりです。
- ダイヤモンドに次ぐ硬度
- 優れた耐摩耗性
- 耐熱性
- 化学的に安定
これらの特長により、CBNは様々な産業分野で重要な役割を果たしています。
研磨加工と表面仕上げの関係
研磨加工は表面仕上げに大きな影響を与えます。例えば、鏡面仕上げされた部品は光を反射しやすく、美しい輝きを放ちます。また、表面の摩擦係数が低くなるため、機械部品の摺動性を向上させることもできます。
一方、研磨加工の精度や仕上げレベルによっては、部品の機能性や耐久性が損なわれる可能性もあります。例えば、研磨が不十分な部品は表面の粗さが大きくなるため、摩擦抵抗が大きくなり摩耗しやすくなります。また、研磨加工が深すぎると、部品の寸法精度が悪化したり、強度が低下したりすることもあります。
そのため、研磨加工を行う際には、目的や用途に応じて適切な方法や条件を選択することが重要です。研磨加工の専門家やメーカーに相談することで、最適な加工方法や仕上げレベルを決定することができ、製品や部品の品質向上やコスト削減につなげることができます。
<研磨加工の種類と表面仕上げの例>
研磨加工の種類 | 表面仕上げの例 |
---|---|
バフ研磨 | 鏡面仕上げ、ヘアライン仕上げ |
電解研磨 | 鏡面仕上げ |
バレル研磨 | バリ取り、面取り |
ラッピング研磨 | 高精度な平面研磨 |
砥石研磨 | 粗研磨、仕上げ研磨 |
この表は、代表的な研磨加工の種類とその表面仕上げの例を示しています。様々な研磨加工方法によって、目的や用途に応じた表面仕上げを実現することが可能です。
研磨加工は、表面仕上げに大きな影響を与え、製品や部品の機能性や耐久性を向上させることができる加工方法です。適切な方法や条件を選択することで、製品の品質向上やコスト削減につなげることができます。
まとめ
研磨加工は、研磨材を用いてワークの表面を削り、平滑性や形状精度、光沢などを向上させる加工技術です。研磨加工は、研削加工と混同されがちですが、研削加工は砥石を用いてワークの形状を変化させる加工技術であり、目的や手法が異なります。
研磨加工には、砥石を使った研磨、ラッピング研磨、バフ研磨、バレル研磨、電解研磨など様々な種類があります。それぞれの方法には特徴があり、加工目的やワークの材質に合わせて適切な方法を選択する必要があります。
研磨加工の手順は、下地処理、ならし、つや出し、鏡面仕上げの4つの工程に分かれています。下地処理は、研磨前のワーク表面の汚れや傷を除去する工程です。ならしは、砥石や研磨材を用いてワークの表面を平滑にする工程です。つや出しは、さらに細かい砥石や研磨剤を用いてワークの表面に光沢を出す工程です。鏡面仕上げは、最終工程として、ワークの表面を鏡のように滑らかに仕上げる工程です。
研磨加工には、砥粒の種類や特性も重要な要素です。ダイヤモンド砥粒は硬度が高く、研削力に優れています。アルミナ砥粒は汎用性が高く、様々な用途に使用されます。炭化ケイ素は硬度が高く、研削力が強いですが、もろいという特徴があります。CBN(立方晶窒化ホウ素)は、ダイヤモンドに次ぐ硬度を持ち、高温にも強いという特徴があります。
研磨加工は、表面仕上げと密接に関係しています。表面仕上げは、ワークの表面を加工して所望の形状や機能、外観を得るための技術です。研磨加工は、表面仕上げの重要な手段の一つであり、ワークの表面に平滑性や光沢、耐摩耗性などを付与することができます。
研磨加工は、様々な産業分野で広く活用されています。機械部品の表面仕上げ、鏡やレンズなどの光学機器の製造、宝石や貴金属の加工など、様々な用途で使用されています。今後ますます需要が高まる技術の一つです。