【完全ガイド】無電解ニッケルの特性と用途を徹底解説
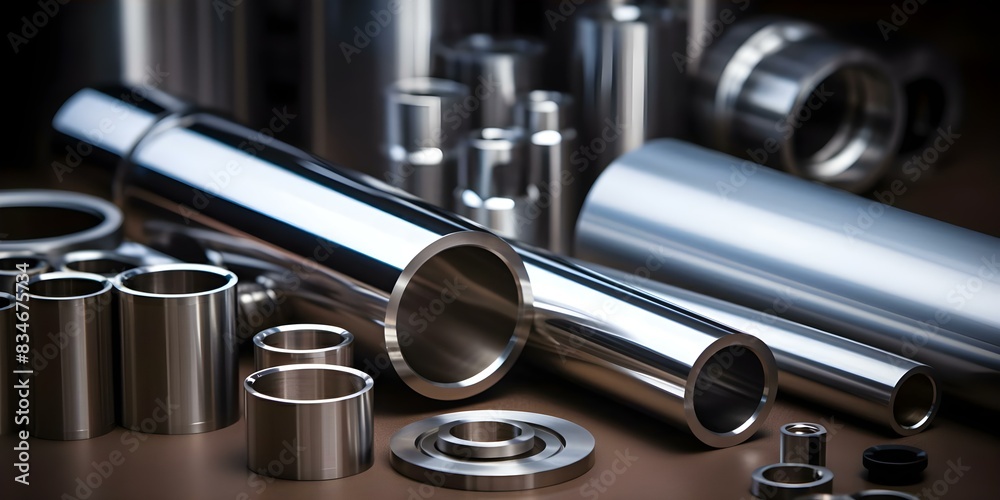
無電解ニッケルは、金属表面処理の分野で注目を集めている技術の一つです。その特性や用途を理解することは、さまざまな産業において重要な要素となります。特に、耐腐食性や耐摩耗性を求められる部品の製造において、この技術は欠かせないものです。
この記事では、無電解ニッケルの基本的な特性やその具体的な用途、さらには処理方法について詳しく解説します。これからこの技術を学びたい方や、実際に導入を検討している方にとって、必要な情報を網羅しています。
無電解ニッケルの魅力は、その適用範囲の広さにもあります。電子機器から自動車部品、さらには医療機器に至るまで、多岐にわたる用途で利用されています。この記事を通じて、無電解ニッケルの可能性を探り、その特性を最大限に活かす方法について知識を深めていきましょう。
無電解ニッケルメッキの特性と他のメッキ方法との違い
無電解ニッケルメッキは、還元剤を用いた酸化還元反応によりメッキ被膜を形成します。これに対して、電気ニッケルメッキは外部から電流を流して成膜します。この違いにより、仕上がりや加工可能な素材も異なります。無電解ニッケルメッキは、複雑な形状の対象物にも均一な被膜を形成できるため、精密部品にも適しています。
無電解ニッケルメッキの基本特性
無電解ニッケルメッキの最大の特長は、複雑な形状の対象物にも均一な厚さでメッキ処理できる点です。電気メッキのように電流の流れに左右されないため、隅々まで均一な被膜を形成でき、高い寸法精度を維持できます。硬度が高く、耐摩耗性に優れている点も特長です。
他のメッキ方法との比較
電解メッキと比べると、均一な膜厚が得られる反面、処理時間が長くコストが高くなります。ただし、複雑形状部品や大量生産には無電解メッキが適しています。また、電解メッキは低コストで様々な金属にメッキできるため広範に使用されています。
選択のポイント
無電解ニッケルメッキの一番の特長は、膜厚の均一性です。膜厚が均一なので、寸法精度が求められる場合に最適です。また、膜厚に厚みをだすことができるので、ピンホールの発生を少なくできる点もメリットの一つといえるでしょう。
無電解ニッケルメッキの具体的な用途と産業での活用
無電解ニッケルメッキは、様々な産業分野で広く利用されています。その一般的な用途には、自動車や航空機の部品、電子機器の接点、建築資材の防錆、装飾品などがあります。自動車や航空機の部品においては、無電解ニッケルメッキは耐摩耗性や耐腐食性に優れているため、長期間にわたって高い性能を維持することができます。
無電解ニッケルメッキの主な用途
無電解ニッケルメッキの用途は多岐にわたります。自動車部品(ディスクブレーキ等)をはじめ、精密機器の部品、航空機部品、その他のプラスチック部品(水栓金具、家電の装飾、電子機器の電磁波シールドなど)など、様々な用途で使われています。
各産業での具体的な活用事例
無電解ニッケルメッキは、自動車産業でのエンジン部品やデジタルデバイスの導体などに使われています。電子機器においては、耐腐食性が必要とされる部品に広く利用されています。航空宇宙産業では、機械部品の耐久性を向上させるために使用されます。
用途に応じた選定基準
無電解ニッケルメッキを選定する際の基準は、使用環境によって異なります。例えば、耐摩耗性が重要であれば厚めのメッキを選ぶ必要がありますし、電磁シールド効果が必要であれば特定の膜厚を維持することが求められます。各用途に応じた適切な仕様を選定することが重要です。
無電解ニッケルメッキの処理工程と方法詳細
無電解ニッケルメッキとは、電気を使用せずに化学的還元反応を用いて行うメッキの一種で、その大きな特徴としてメッキの膜厚を均一に処理できることがあります。この処理によって、製品の形状にとらわれず被膜の均一性を保つことが可能であるため、非導電性素材に対してもメッキを施すことが可能です。処理工程は複数の段階があり、精密な工程管理が求められます。
無電解ニッケルメッキの基本的な処理工程
無電解ニッケルメッキの基本的な処理工程は、主に以下の6つに大別されます。1. 脱脂工程:製品に付着している油分を除去します。2. エッチング(表面粗化)工程:表面を粗化してメッキの密着性を高めます。3. スマット除去:表面の不純物を取り除きます。4. ジンケート処理:亜鉛置換を行います。5. ジンケート剥離:表面を整えます。最終的な成果物の品質はこれらの工程でのコントロールに大きく左右されます。
メッキ方法の種類と選び方
メッキ方法には、乾式と湿式の2種類があります。乾式メッキは蒸着やスパッタリング技術を用いる方法で、湿式メッキは電解や無電解メッキを指します。無電解メッキは、均一なコーティングが可能なため、微細なディテールを持つ部品や複雑な形状の部品に最適です。選択の際には、処理対象の素材特性や最終用途に応じて適切な方法を選ぶことが重要です。
工程における注意点
無電解ニッケルメッキの工程では、高温処理が必要なため、耐熱性の低い素材や、加熱によって変形や物性変化を起こす可能性がある素材には適していません。また、膜厚コントロールにおいては、メッキ液の条件や温度管理が重要で、均一な成膜を可能にするために、一定のプロセス管理が求められます。特に、高温環境では変色のリスクがあるため、注意が必要です。
無電解ニッケルメッキの膜厚調整と目的別最適化
無電解ニッケルメッキは、用途や使用環境に応じて様々な膜厚を選択できます。たとえば、耐摩耗性や耐食性をより向上させたい場合には、メッキの膜厚を厚くすることが推奨されます。一般的な無電解ニッケルメッキの膜厚は5〜10µmが多いですが、耐摩耗性を目的とする場合は比較的厚めにメッキすることが望ましいです。膜厚の調整は、対象物の膜厚が均一になるため、高い寸法精度が求められるような電子部品や精密機械部品等で用いられることが多いです。
膜厚の重要性とその影響
膜厚の重要性は、コーティングの効果を最大限に発揮するために欠かせません。膜厚が適切でない場合、外壁に対する保護機能が不十分になり、耐久性が低下してしまいます。特に、自動車のボディや部品の下地塗装として膜厚の管理は必須であり、膜厚が薄い場合でも厚い場合でも性能が十分に発揮できない場合があります。したがって、膜厚管理は必要な性能を確保するために欠かせません。
目的に応じた膜厚の選び方
膜厚の選び方は、素材と被膜の種類から用途に応じた膜厚計を選びます。たとえば、磁性のある金属素材の上に非磁性体の塗装をしている場合は電磁式膜厚計を、磁性のない金属素材の場合は渦流式膜厚計を選ぶのが一般的です。膜厚計はレンタルも可能で、使用目的に合わせた選択が重要です。購入時には必ず測定範囲が指定されていることを確認する必要があります。
膜厚調整の具体的な方法
膜厚を均一化するためには、いくつかの工夫や調整が必要です。主な方法としては、ゼロ点調整や、調整点が実際の膜厚範囲より厚めで、なおかつ最も最大値に近いフォイルで実施することが推奨されます。また、膜厚の測定技術としては、光の干渉効果を利用したピークバレー法が一般的で、このパターンのピーク、バレー波長から膜厚を求めます。
無電解ニッケルメッキ導入時のコスト、技術的課題、リスク
無電解ニッケルメッキの導入においては、まずコスト面で高額となる傾向があります。理由として、電解メッキと比較すると、無電解メッキは材料費が高く、メッキの析出速度も遅いことが挙げられます。例えば、無電解メッキに必要な機械や装置の構築は変動が大きく、管理面での負担が増すことがデメリットとされています。このため、導入に際しては設備投資が必要となる場合が多いです。要点は、無電解メッキの特徴を活かすためには、初期投資を伴うものであるという認識が必要です。
導入にかかるコストの内訳
無電解ニッケルメッキの導入にかかるコストの内訳としては、材料費、労働力、機械設備の維持費などが挙げられます。理由として、無電解ニッケルメッキは大量処理が可能である反面、化学反応を利用するため、電流を必要とせず、一度に多数の製品を処理することができるためです。例えば、無電解メッキは通常の電解メッキと比べ、均一な被膜を得やすいが、設備の自動化が進むことで、24時間稼働を可能にするシステムの導入も進められています。要点として、導入初期のコストは高いものの、長期的にはコスト削減が可能であるという点が挙げられます。
技術的課題とその対策
無電解ニッケルメッキは、技術的課題としてはんだ付け性が低いという点があります。理由は、被膜形成しやすい酸化被膜が表面にあり、これがはんだと金属表面の密着性を阻害するためです。具体例として、無電解メッキの後にベーキング処理を行うことで、高い硬度を実現することが可能です。RoHS指令にも抵触しないため、安心して使用できる点も特徴です。要点は、無電解メッキの技術的課題を理解し、適切な処理を施すことで対策が可能であるということです。
リスク管理と予防策
無電解ニッケルメッキのリスク管理には、腐食の進行やコスト高騰のリスクが存在します。理由として、適切なメッキを施しても過酷な環境に晒されると、めっきの腐食が進む可能性があるためです。例えば、高湿度や酸性の環境では錆が発生するリスクがあります。これを防ぐためには、製品の用途や使用環境に適した表面処理を行うことが重要です。要点として、無電解メッキのリスク管理には、メッキの均一性と被膜の存在が影響を及ぼすため、均一なメッキを適用することが耐食性を高めることに繋がります。
まとめ
無電解ニッケルは、優れた耐腐食性や耐摩耗性を持つため、多くの産業で幅広く利用されています。この技術は、電気を使用せずに金属表面にニッケルを析出させるため、複雑な形状の部品にも均一にコーティングできるのが特徴です。
無電解ニッケルの主な用途には、電子機器、航空宇宙、医療機器などがあり、高い性能が求められる場面で重宝されています。また、コーティング方法には、化学的還元を利用する方法が一般的で、特定の条件下で反応を進行させることで、品質の高い仕上がりを実現します。