部品の強度を高めるための【設計の基本】ガイド
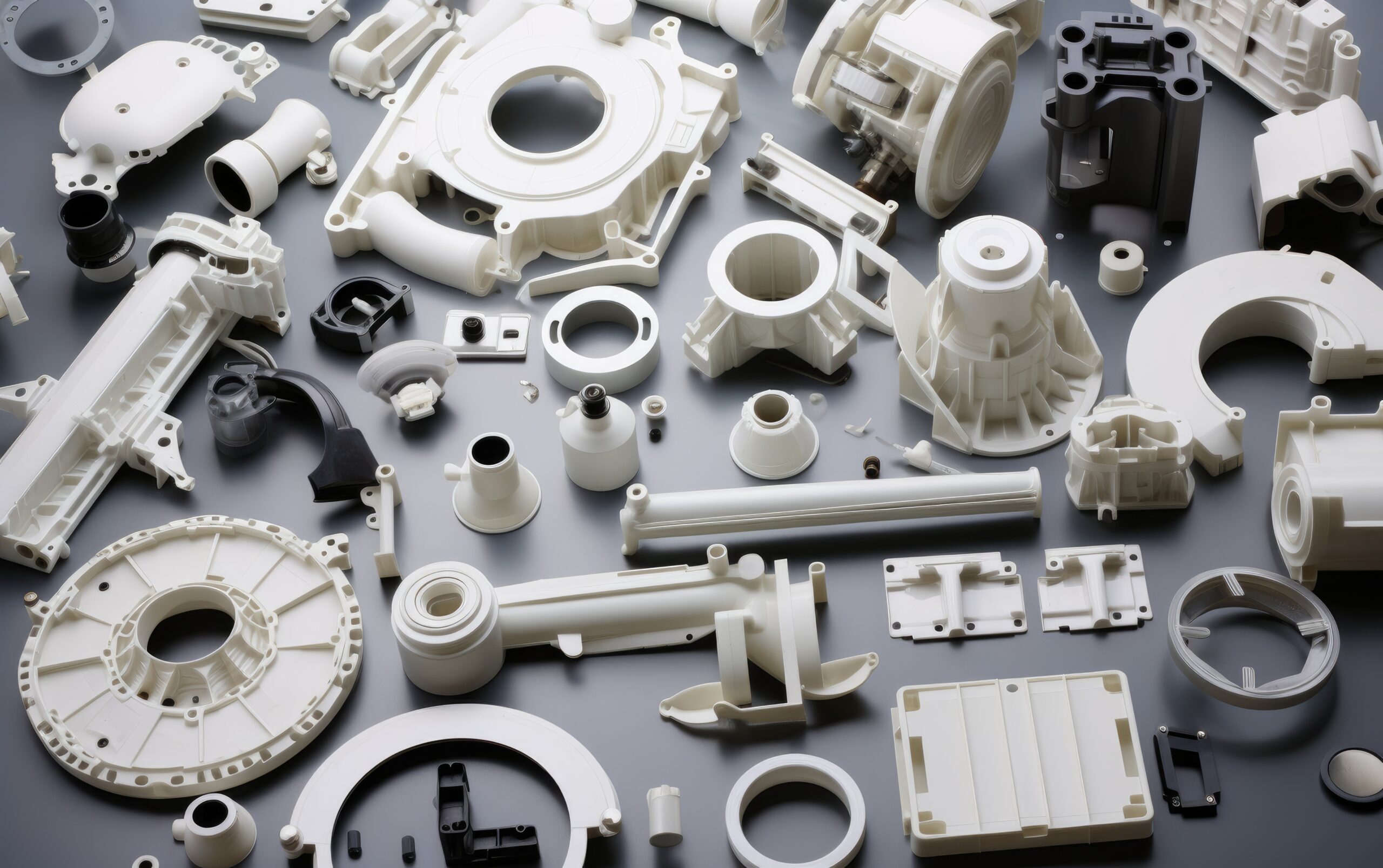
「部品の強度を高めたいけれど、どのように設計すれば良いのか分からない」とお悩みの方は多いのではないでしょうか。そんな皆様に向けて、設計の基本をしっかりと押さえたガイドをお届けします。
本記事では、部品の強度を向上させるための設計の基本について解説します。強度だけでなく、耐久性や機能性を両立させるためのポイントも紹介し、実際に役立つ情報をお届けします。
設計がしっかりしていれば、製品の性能や信頼性にも大きく影響します。これから設計を始める方や、より一層スキルを向上させたい方にとって、必見の内容となっています。さあ、強度を高めるための設計の世界に一歩踏み出してみましょう!
部品の強度を考慮した設計の基本的な手法とアプローチ
部品設計において強度を考慮することは、製品の信頼性と安全性を確保するために不可欠です。これを達成するためには、材料の選定、構造の最適化、そして負荷を受ける際の応力と変形を十分に理解することが必要です。例えば、SUS304の材料を使用する際、曲げや衝撃が頻繁に発生する部分には板厚を増やすなどの設計工夫が求められます。このように、特定の材料特性や負荷条件を考慮に入れた最適化が、強度設計の成功につながります。
強度設計における重要な要素と基準
強度設計には、応力やひずみの理解が重要です。適切な強度設計を進めるためには、材料の物性や標準強度から発生する応力を評価し、それが許容範囲内に収まるように形状や寸法を工夫することが求められます。例えば、材料の弾性率や破壊靭性は製品や部品の耐久性や信頼性に直接的な影響を与えるため、材料選定は非常に重要です。適切な基準の設定により、コストを抑えつつも十分な強度を確保することが可能です。
設計プロセスでの強度評価のステップ
強度評価のプロセスでは、まず使用する部品の図面を描き、寸法や締結方法を決定します。次に、その構造が求められる強度を満たすように、設計の各ステップで評価を行います。CAE解析などを活用することで、実物の試作品を作成する前に問題を発見し、改善することが可能です。これにより、より精度の高い設計が実現され、製品の品質向上につながります。
実際の設計事例から学ぶ強度向上のポイント
実際の事例を通じて強度設計の重要性を学ぶことは非常に有用です。例えば、事故事例の分析では、材料の力学的特性の検証を通じて全体像を明らかにし、そこから得られる教訓を設計に活かすことができます。具体例として、耐久性の向上を目指したプラスチック製品の設計では、割れや破損のリスクを低減するために、材料の基本的な知識や応力の伝播を考慮した設計が活用されています。これにより、設計の初期段階での計画がしっかりしていれば、後工程でのトラブルを未然に防ぐことができ、製品の品質を維持しながらコストの最適化が可能です。
部品の強度を評価するための力学の基礎知識
部品の強度を確保するためには、力学の基礎知識が不可欠です。力学は物体に作用する力とその効果を理解するための科学であり、部品の耐久性や安全性を評価するための基本的な要素となります。特に、材料力学や静力学の知識は、部品がどのように力を受けるのかを予測し、設計に反映させるために重要です。例えば、CAE(Computer-Aided Engineering)を活用することで、部品全体の応力状態をシミュレーションし、最も負荷がかかるポイントを特定することができます。このように、現代の機械設計において力学の基礎知識は、部品の強度を評価し、安全性を確保する上で要となります。
力学の基本概念とその応用
力学の基本概念は、設計プロセスにおいて非常に重要です。力学の基本には、力のつり合いや運動の原理などが含まれ、これらを正確に理解することで、設計の精度や効率を向上させることができます。例えば、静力学の応用により、建物や機械の構造がどのように力を受け止めるのかを理解し、適切な材料選択や構造設計を行うことが可能です。このように、力学の基礎知識は多くの産業分野で応用され、その成果物の品質向上に寄与します。
強度評価に必要な計算とその手法
部品の強度評価には、いくつかの計算手法が必要です。これには、材料の引張強度や圧縮強度の測定、およびこれらの特性をもとにした応力やひずみの計算が含まれます。例えば、CAE解析を用いることで、設計段階で部品がどのような圧力を受けるのかを詳細にシミュレーションし、必要な強度を持つ設計を行うことができます。また、手計算による強度評価も重要で、CADと組み合わせることで、設計の精度を向上させることができます。このように、強度評価には計算手法の理解と適用が欠かせません。
実践で使える力学の知識とツール
実践で役立つ力学の知識は、3DCADやCAE解析などの最新のツールを用いることで、より効果的に活用できます。これらのツールは、部品の設計や強度評価において、精密な解析と改善を可能にします。例えば、CAEソフトウェアを使用すると、複雑な構造の強度解析を迅速かつ正確に行うことができ、設計変更のサイクルを短縮します。また、材料力学や機械力学の知識を応用することで、現場で直面する問題を効率的に解決するスキルを身につけることができます。これらの知識とツールを適切に組み合わせることで、設計の質を高め、より安全で耐久性のある製品を作り出すことが可能です。
プラスチック製品の強度設計における特有の課題と注意点
プラスチック製品の強度設計では、その特性上、特有の課題が多く存在します。要点として、プラスチックは金属に比べて強度が低いため、設計時には応力集中が発生しやすい形状や過度な薄肉化に注意が必要です。理由として、こうした設計は破損の原因になるため、適切な強度設計が必要です。具体例として、日常使われるプラスチック部品が軽量でデザインの自由度が高い反面、応力集中による破損のリスクがあることが挙げられます。したがって、設計段階で強度に関するデータやシミュレーションが重要になります。
プラスチック材料の特性と強度設計の要点
プラスチックの特性は、強度設計において重要な役割を果たします。要点としては、プラスチックは耐化学薬品性、軽量さ、耐摩耗性などの特長を持ちますが、引っ張り強度や圧縮強度が金属に比べて劣る場合があります。理由として、このためプラスチック製品の強度設計には、使用する材料の特性を正確に見積もることが必要です。具体例として、ABSなどのプラスチックは耐衝撃性が要求される製品に使用されますが、その強度を満たすための設計が求められます。これにより、プラスチックの特性を生かした設計が製品の品質向上に貢献します。
よくある設計ミスとその回避法
設計ミスは製品の強度不足や性能不良を招くため、回避が重要です。要点として、設計ミスは設計者の経験不足やチェック体制の不備によって発生します。理由として、例えば、素材の選定ミスや負荷の計算誤りが挙げられ、これらは製品の故障や劣化を引き起こします。具体例として、キャリアの設計において荷重分布が偏ることによる破損が報告されています。これを防ぐために、設計レビューやシミュレーションの活用が重要です。これにより、設計の精度を高め、製品トラブルを未然に防ぎます。
環境要因がプラスチック強度に与える影響
プラスチックの強度は、環境要因によって大きな影響を受けます。要点として、温度、湿度、紫外線などが強度に影響を与える主な要因です。理由として、例えば、高温多湿環境下では材料の強度が低下しやすく、紫外線による劣化が進行します。具体例として、屋外で使用されるプラスチック製品は紫外線による劣化が早く、強度が低下することがあります。これに対し、UVカット素材の使用や耐候性のあるプラスチックの採用が対策となります。したがって、設計段階から環境要因を考慮し、適切な材料選定と設計が求められます。
引張強度、許容応力、安全率の具体的な計算方法と適用例
部品の強度を高めるための設計には、引張強度、許容応力、安全率の理解と計算が不可欠です。これらの要素は、安全で効率的な設計の基本を形成し、それぞれの適用方法と具体例を示したいと思います。
引張強度の計算とその実用例
引張強度は材料の最大引張荷重を破断面積で除した値で表され、材料の強さを示す重要なパラメータの一つです。例えば、SS400という軟鋼の引張強度は400 N/mm²です。この数値を使って安全率を考慮した具体的な設計例を導き出します。多くの工学的な用途で、引張強度は試験機を用いて標準化された方法で計測されます。このようなデータは、設計者が安全性を確保しながら最大限の効率を引き出せるように活用されます。
許容応力を設計に取り入れる方法
許容応力は、材料が安全に負荷を受けることができる最大応力を指し、基準強度を安全率で除して求められます。許容応力設計法は、構造物に発生する応力がその材料の許容応力を超えないように設計する方法です。例えば、ある材料の基準強度が500 N/mm²で安全率を2とした場合、許容応力は250 N/mm²になります。この設計手法は、様々な条件下での構造安全性を確保するために重要です。
安全率の考え方とその具体的な適用
安全率は、設計時にどの程度の余裕を持たせるかを示す数値で、通常は1以上を設定します。安全率が高いほど、設計はより頑丈で信頼性の高いものとなります。例えば、100kgまで耐えられる強さが必要な棚を作る際に、実際には200kgまで耐えられるように設計することが推奨されます。これにより、不測の事態にも対応できる安全マージンが確保されます。
強度設計で直面する可能性のあるリスクと問題点の対策
強度設計においては、部品の耐久性や信頼性を確保するためのリスク管理が不可欠です。リスクとしては、材料の選定ミスや設計上の計算エラーが考えられ、これらは部品の強度不足や破損に繋がる可能性があります。具体例として、航空機や原子力発電所での部品の破損が大きな問題となることがあり、損傷許容設計や厳密な品質管理が必要とされます。最終的に、安全性と効率の両立を図ることが重要です。
設計段階でのリスクアセスメントの重要性
設計段階でのリスクアセスメントは、製品の安全性と信頼性の確保において重要な役割を果たします。適切にリスクを評価し、低減措置を講じることで、事故や故障のリスクを最小限に抑えることができます。具体的な方法として、リスクアセスメントは、機械の設計段階で行い、誤使用や計算コストの課題を解決することで製品の安全性向上に寄与します。最終的に、設計者はこれを継続的に見直すことが必要です。
一般的な問題点とその解決策
強度設計における一般的な問題点として、応力集中による材料の疲労や破損が挙げられます。これに対する解決策として、適切な形状設計が求められます。例えば、シャープなエッジを避け、均等な応力分布を保つようにします。また、材料の選定も計算コストの増加や精度不足を回避するために重要です。これにより、製品の耐久性と信頼性を高めることができます。
リスクを最小化するためのプロセスと手法
リスクを最小化するためには、リスクアセスメントを適切に実施し、リスク低減策を選択することが重要です。具体例として、安全設計や品質保証システムの導入が挙げられます。適切なリスク低減手法を用いることで、信頼性の高い製品を提供することが可能となります。これには、安全係数と材料選定基準を明確化し、設計者が技術的に適切な方法を採用することが含まれます。最終的に、継続的なリスク評価とプロセス改善が必要です。
まとめ
部品の強度を高めるためには、設計段階での工夫が非常に重要です。材料の選定や形状の最適化、負荷の分散といった要素が絡み合い、全体の強度を決定づけます。特に、応力解析を行い、弱点を特定することで、より効果的な設計が可能となります。
また、製造プロセスにおいても、適切な加工方法や熱処理を選ぶことで、部品の耐久性を向上させることができます。さらに、試作やテストを繰り返すことで、実際の使用条件下での性能を確認し、必要に応じて設計を修正することが大切です。