半導体業界必見!【PVDとCVD】の違い徹底解説
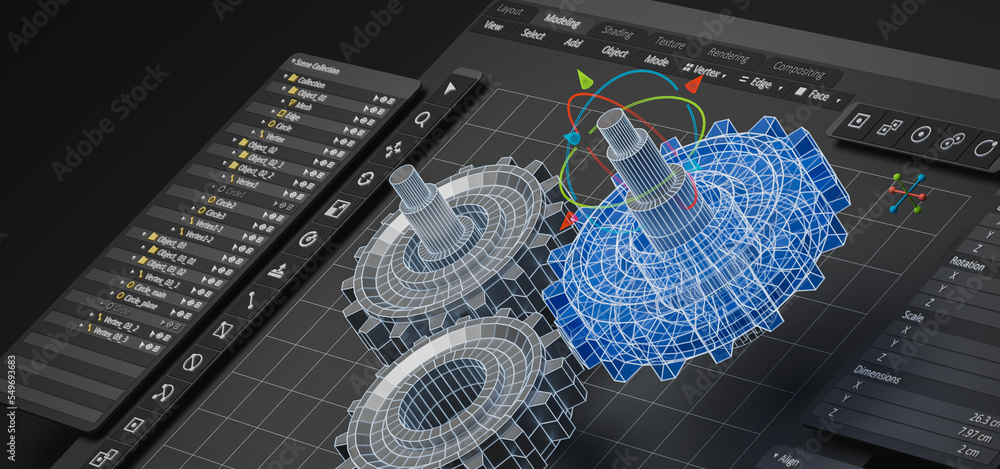
半導体業界の進化が止まらない中、製造プロセスの選択はますます重要になっています。特に、薄膜を形成する技術の中でも、特定のニーズに応じた選択が求められる場面が増えています。しかし、数多くの技術が存在する中で、どの方法を選べば良いのか迷っている方も多いのではないでしょうか。
本記事では、薄膜形成における二つの主要な手法について詳しく解説します。これらの技術の特徴や利点、適した用途を理解することで、あなたのプロジェクトに最適な選択をする手助けができればと思います。製造工程の効率化やコスト削減を目指す方々にとって、これらの知識は非常に価値のあるものとなるでしょう。
さあ、半導体製造の世界を深く掘り下げ、最適な技術選択を行うための一歩を踏み出しましょう!
半導体業界におけるPVDの役割
物理蒸着(PVD)プロセスは、半導体業界で重要な役割を果たしています。要点として、PVDは材料が凝縮相から蒸気相に移行し、再び薄膜の凝縮相に戻るプロセスを特徴としています。理由として、このプロセスはスパッタリングや蒸発などの方法によって行われ、微細な構造を持つ高純度の薄膜を形成することが可能です。具体例として、磁気記録媒体や光学コーティングなど、精密さが要求されるデバイスに広く活用されています。これにより、PVDは半導体製造において欠かせない技術として確立されています。
半導体業界におけるCVDの役割
CVDプロセスもまた、半導体製造において重要な位置を占めています。要点は、化学蒸着(CVD)ではウェハー(基板)が揮発性の前駆体にさらされ、基板表面で反応または分解して所望の堆積物を生成する点です。理由として、CVDは細かい制御が可能で、均一な薄膜を大規模に供給できるためです。具体例として、シリコン、窒化ケイ素、酸化ケイ素などの層を形成する際に使われ、微細な回路パターンを作成するのに不可欠です。このプロセスがあることで、半導体の性能向上と製造効率が大きく向上します。
PVDとCVDの技術的な違いとそれぞれのメリット
結論として、CVDとPVDは、それぞれ独自のメリットを持ち、用途に応じて選択されるべき技術です。CVDは化学反応を利用して高密着性の薄膜を形成するのに対し、PVDは物理的なプロセスを通じて特に耐久性のあるコーティングを施すことができます。適切な成膜技術の選択により、製品の性能と寿命が大きく向上します。
PVDの技術とその利点
PVDは金属材料にセラミックスの薄膜を生成させる技術で、有名な手法には真空蒸着、スパッタリング、イオンプレーティングがあります。PVDコーティングは、金属表面の特性を変化させ、耐久性、耐食性、機能性を向上させます。これにより、工具の表面を鏡面仕上げにし、その上にPVDコーティングを施すことで、工具の寿命を延ばし、切削性能を向上させます。
CVDの技術とその利点
CVD(化学気相成長法)は、半導体の製造において重要な技術で、化学反応によって高品質な薄膜を生成します。CVDの大きなメリットは、均一な膜を作ることができる点で、これは半導体の性能を高めるために不可欠です。CVDでは、複雑な形状の基板でも均一で密着した薄膜を形成することが可能です。
PVDとCVDのコーティング用途に適した選択肢
要点として、PVDとCVDの選択は、成膜したい膜の種類、成膜する基板の材質、希望する膜の特性などによって異なります。高純度や高均一性の膜が必要な場合はCVDが、低温成膜やシンプルな装置を好む場合にはPVDが適しています。それぞれの技術には利点と制約があり、用途に応じて適切な成膜技術を選択することが重要です。例えば、CVDはガスを使用して膜を形成するため均一性に優れていますが、高温を必要とします。一方でPVDは多様な材料に適用可能であり、比較的低温で成膜が可能です。要点として、目的に応じた技術選択が必要です。
一般的なコーティング用途とPVDの適用例
要点として、PVDは物理的に薄膜を形成する技術で、特に硬さと耐摩耗性が求められる製品に広く利用されています。理由として、PVD法は低温で多元素合金膜を形成することができ、基板材料を選ばないためです。例えば、切削工具、光学レンズ、医療用インプラント、装飾品などに応用され、特にTiNやTiAlNなどのコーティングがよく使用されます。具体例として、PVDは工具の耐摩耗性を高めるために広く利用されており、切削工具やギアの表面に施されます。要点として、PVDは多用途でかつ経済的なコーティング技術といえます。
一般的なコーティング用途とCVDの適用例
要点として、CVDは化学反応を利用して膜を形成する技術で、特に均一で高密度な膜が必要な用途に適しています。理由として、CVDは高温でガスを用いてコーティングを行うため、密着性が優れており、複雑な形状にも適したコーティングが可能です。例えば、半導体の絶縁膜や保護膜、切削工具の刃先部などに多く利用されています。具体例として、半導体製造において、酸化シリコンや窒化シリコン膜の形成によく用いられ、また高温環境に耐えうる膜を提供します。要点として、CVDは高温に耐える材料や均一性が求められる場合に最適です。
半導体業界でのPVDとCVDの役割と重要性
PVD(物理蒸着)とCVD(化学蒸着)は、半導体を作るための大切な技術です。要点として、PVDは材料を蒸発させて薄い膜を作る方法です。例えば、鏡の表面をきれいにするために使われます。一方、CVDはガスを使って化学反応を起こし、材料を固める方法です。これにより、半導体の製造において、重要な表面処理をすることができます。
半導体製造におけるPVDの役割
PVD(物理蒸着)は、半導体製造において非常に重要な役割を果たします。この技術は、材料を加熱して真空中で蒸発させ、基板に薄膜を形成する方法です。具体的には、高品質な金属膜をチップに形成するのに利用され、これにより電子回路が正確に動作するための導体層を作り出します。PVD技術の特長は、その精度と効率にあります。したがって、半導体製品の性能を高めるためにPVDは欠かせない技術として認識されています。
半導体製造におけるCVDの役割
CVD(化学気相成長法)は、半導体の製造において重要な技術です。CVDの大きなメリットは、均一な膜を作ることができる点です。これは、半導体の性能を高めるためにとても大切です。例えば、CVDを使うと、薄い膜を均等に広げることができ、これにより電子機器がより効率的に動くようになります。具体例としては、トランジスタやダイオードのような部品の製造でCVDが用いられ、高度な機能性と安定性を提供します。結果として、半導体製造においてCVDは、サブミクロンレベルの精密な加工を可能にする技術として、重要な役割を果たしています。
PVDとCVDの選択基準と判断ポイント
半導体業界で使用されるPVD(Physical Vapor Deposition)とCVD(Chemical Vapor Deposition)は、それぞれ異なる特性を持つため、用途に応じて適切な技術を選択することが重要です。要点として、PVDは主に物理的な保護膜を形成し、低温でもプロセスが可能で、多様な材料に適しています。一方、CVDは化学反応を利用し、高温での処理が求められ、高密度で均一な膜を形成することができます。例えば、PVDは熱に弱い素材に適しており、CVDは密着性が求められる高温環境での使用が推奨されます。したがって、選択基準としては、温度条件や求められる被膜特性を考慮し、最適な方法を決定することが重要です。
選択する際の重要な基準
PVDとCVDを選択する際の基準は、プロセス温度、膜の特性、材料の構造など多岐にわたります。要点として、PVDは低温で作業が可能で、熱に弱い基材に適しているため、素材の温度耐性が低い場合にはPVDを選ぶことが推奨されます。具体例として、電子デバイスの製造においては、熱による損傷を防ぐため、PVD技術がしばしば選択されます。一方、CVDは高密度で均一な膜形成が可能であり、高温環境が許される場合にその性能を発揮します。このように、膜の密着性や機械的特性が重要視される場合にはCVDが適しています。
用途に応じた最適な判断ポイント
用途に応じた最適な判断ポイントは、要求される膜厚、密着性の質、素材の耐熱性などです。要点を押さえると、PVDは低温で作成できるため、温度に敏感な素材に対して有利です。具体例として、装置の内壁コーティングにおける耐摩耗性向上目的でPVDが使用されることがあります。また、CVDは高温に耐え、優れた密着性と耐久性が求められる用途、例えば航空機部品の保護に利用されます。最終的に、用途に最も適した技術を選択することで、最高のパフォーマンスが引き出されます。
工具のコーティングにおけるPVDとCVDの比較
工具のコーティングにおいて、PVD(物理的蒸着法)とCVD(化学的蒸着法)は、性能と応用において異なる特性を示します。要点は、CVDが高温での化学反応により被膜を形成するため、密着性と均一性に優れています。これは、例えば、高い耐摩耗性が求められる場合に有用です。一方、PVDは低温でプロセスが可能であり、硬度と滑り性が要求される工具に適しています。具体的な使用事例としては、PVDが小型部品に適用された結果、耐クラッキング性能を向上させた例もあります。CVDとPVDの選択は、使用環境や求められるコーティング特性に大きく依存します。このように、それぞれの方法は特化した条件下で優位性を発揮します。
PVDが工具のコーティングに適している理由
PVD(物理的蒸着法)は、工具のコーティングにおいて多くの利点を提供します。要点としては、PVDによるコーティングが比較的低温で行われるため、基材に対する熱影響を最小限に抑えることができます。理由は、工具の素材を損なわずに硬い薄膜を形成でき、耐摩耗性の向上に寄与するからです。具体例としては、金属表面を滑らかにしつつ耐摩耗性を向上させることで、工具の寿命を延ばし、切削性能を高めます。このように、PVDは工具に求められる耐久性と性能向上に寄与し、コーティング方法としての優位性を発揮しています。
CVDが工具のコーティングに適している理由
CVD(化学的蒸着法)は、工具コーティングにおいて共通して高温で行われるため、高い密着力と均一な膜形成が可能です。その要点は、密着性の高いコーティングが得られることです。例えば、高温での処理により、被膜が工具に対して高い密着性を持ち、耐摩耗性の面で優れた性能を発揮します。具体例としては、超硬合金表面へのコーティングにより、耐熱性および密着性の優れた工具を提供できます。このため、CVDは高温環境で使用される工具に特に適しており、製品の品質と性能を向上させる上で重要です。
まとめ
半導体製造において、薄膜技術は不可欠な要素です。その中でも、物理蒸着法と化学蒸着法は、各々の特性に応じて異なる用途に適しています。物理蒸着法は、膜の均一性や密着性が優れており、高い透明度が求められるアプリケーションに最適です。一方、化学蒸着法は、複雑な形状への適用や、特定の化学成分を使った高機能膜の形成が得意です。
どちらの技術を選ぶかは、必要とする膜の特性や製造プロセスの要件によります。選択する際には、膜の性能、コスト、製造スピードなど多角的な視点から考慮し、最適な手法を導き出すことが重要です。最新の市場動向や技術革新を踏まえつつ、適切な戦略を立てることで、競争力を高めることが可能になります。