【知っておきたい】プラスチック射出成形の基本とその利点とは?
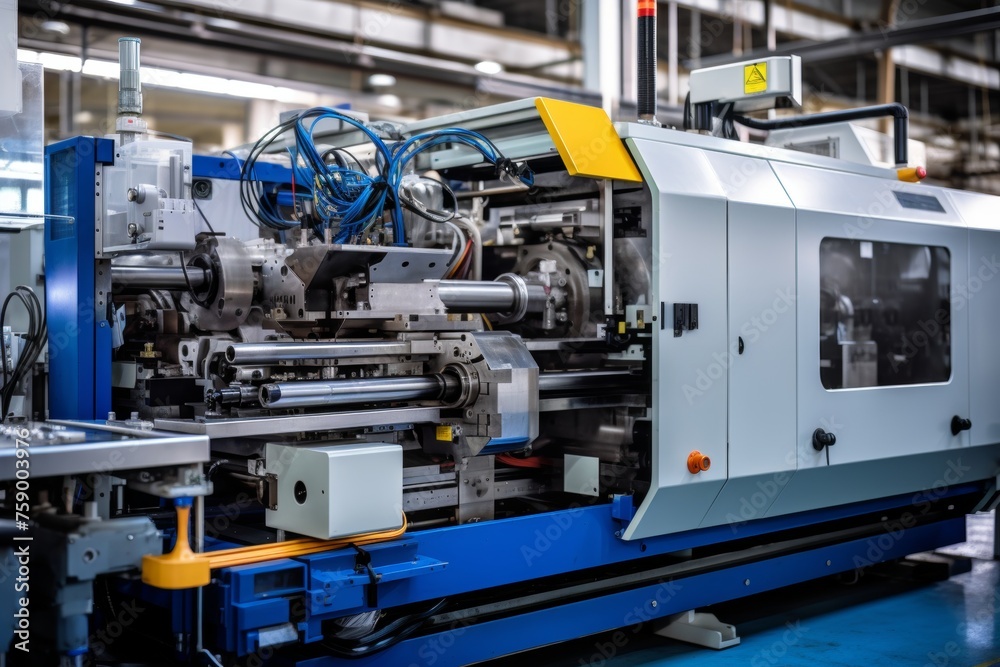
プラスチック製品が私たちの生活に欠かせない存在になっている今、それを形作るプロセスに興味を持つ人も増えてきています。特に、効率的かつ精密に製品を生み出す手法は、多くの業界で重宝されています。もし「プラスチックの成形方法について知りたい」と思っているなら、この記事がその手助けとなるでしょう。
このガイドでは、プラスチック成形の基本的な概念から、その利点までを詳しく解説します。なぜこの手法が選ばれるのか、どのようにして高品質な製品が生まれるのか、そしてそのプロセスがどのように進化してきたのかを掘り下げていきます。これを読めば、プラスチック成形の魅力と可能性についての理解が深まることでしょう。
製造業界における革新や効率化が進む中、この技術がどのように役立っているのかを知ることは、今後のビジネス戦略を考える上でも重要です。それでは、プラスチック成形の世界へと一歩踏み出してみましょう。
プラスチック射出成形の基本とは?
プラスチック射出成形は、プラスチック製品を大量生産するための基本的かつ効率的な製造方法です。要点として、この方法はプラスチック樹脂を加熱して溶かし、高圧で金型に射出し、冷却して形状を固めるというプロセスを踏みます。理由として、射出成形は高精度かつ迅速な生産が可能であり、複雑な形状や薄肉の製品を製造するのに適しています。具体例として、自動車部品や家電製品、医療機器など、日常生活のあらゆる場面で射出成形によって作られた製品が使用されています。要点として、射出成形は多種多様な形状の製品を大量に生産するための最適な加工方法です。
プラスチック射出成形の仕組みを徹底解説
射出成形プロセスは、基本的に3つのステップで構成されています。まず、樹脂を加熱して溶かす「溶融工程」、次に溶けた樹脂を金型に流し込む「充填工程」、そして金型内で樹脂を冷やして固める「冷却工程」です。この工程により、非常に多様な製品を製造することが可能です。例えば、自動車のパネルや電子機器のケースなど、精密で耐久性のある製品がこのプロセスを通じて生み出されています。プラスチック射出成形の仕組みを理解することは、製品設計や製造工程の最適化に役立ちます。
射出成形プロセスのステップバイステップガイド
射出成形のステップは詳細に分かれています。最初に、設計と金型の準備が行われ、その後に樹脂材料を加熱し溶融させる「溶融準備期間」が始まります。次に、溶けた樹脂が高圧で金型に射出される「射出工程」が行われます。金型内で樹脂が冷却・固化された後、「型開き」と製品の「取り出し」が行われ、最終的に製品の品質管理と検査が行われます。プロセスの各ステップを着実に行うことが、高品質で効率的な製品製造に不可欠です。射出成形の詳細なステップガイドは、技術者や設計者にとって重要な知識です。
射出成形のコストと納期を効率化する方法
射出成形の効率的なコスト削減は、企業の競争力を高める上で不可欠です。要点は、固定費や変動費を見直すことです。例えば、原材料の選定をコスト効率の良いものに変更したり、生産量を増やしてスケールメリットを活かすことが考えられます。また、不良率を下げることや、工程の自動化を進めることで省人化を図ることも有効です。結果として、全体の生産コストが削減され、企業の収益性向上につながります。
射出成形のコスト削減テクニック
射出成形のコスト削減には、設計段階での部品の最適化が重要です。壁の厚さを最適化し、材料の使用量を減らすことが可能です。さらに、不要なアンダーカットを無くす設計や、リサイクル可能な材料の利用による廃棄ロスの削減も有効です。具体例としては、パーツの簡素化と製造プロセスの短縮によって、材料費、加工費、設備費を押さえることができます。こうした取り組みにより、全体のコストをかなり削減できるでしょう。
納期短縮のための効果的な対策
納期短縮を実現するためには、スマート工場の導入が効果的とされています。生産効率を向上させることで製造時間を短縮し、結果的に納期も短縮できます。例えば、射出成形機と金型製造現場が同じ工場内にあることで、プロジェクトの流れをスムーズにすることができ、短納期化につながります。また、3Dデータを活用した製造プロセスの最適化によって、さらに納期を短縮することが期待できます。このような技術革新を取り入れることにより、迅速な製品納入が可能となります。
他の成形工法と比べた射出成形の利点
射出成形は、熱可塑性樹脂を高温で溶かし、金型に圧力をかけて注入し、形を形成する手法です。他の成形工法に比べて、自由で複雑な形状の製品を容易に作ることができるという利点があります。また、他の工法よりも短いサイクルで製造でき、製造コストが安く抑えられる点も魅力です。このような特徴により、射出成形は多様な製品の大量生産に適しています。
射出成形の主な特徴とメリット
射出成形は、加熱で溶解したプラスチックを専用の金型に流し込んで成形する製造方法です。この方法は、幅広い分野の製品製造に用いられています。大量生産に適しており、精度が高く均一な製品を製造できる点がメリットです。また、一度金型を製作してしまえば、迅速に製造を行うことができる効率性も特徴の一つです。
射出成形が選ばれる理由とは?
射出成形が選ばれる理由は、まずその量産性にあります。金型を一度製作すれば、材料の分量を調整するだけで速やかに成形を行うことが可能です。また、1回の成形にかかる時間は秒単位であり、一つの金型で複数の成形を行うことも可能です。このため、射出成形は非常に優れた量産性を持っているといえます。
射出成形における機械と技術の詳細
射出成形とは、プラスチック樹脂を加熱して溶融し、金型に射出することで成形品を作る成形法です。この技術には、精密な製品を作るためにサーボモーターを利用して射出装置の制御が行われることが多く、製品の成形精度が向上します。特に金型の設計が重要で、その精度が製品の品質に直接影響します。射出成形機は、成形材料の種類や射出装置の構造から分類され、それぞれの特徴を生かしながら効率的な成形が行われます。主要な技術には、電動式や油圧式などがあります。製品の多様性に対応するため、金型設計の工夫が求められます。
射出成形に必要な機械の種類と機能
射出成形機は、大きく分けて型締装置と射出装置で構成されています。型締装置は、金型を開閉したり、完全な密閉状態を保持する機能があります。射出装置は、プラスチック材料を溶融し、高圧で金型に注入する機能を持っています。これらの動力源には電動方式と油圧方式があり、電動式はサーボモーターを中心とした電力系、油圧式は油圧ポンプを使う機械系に分かれます。それぞれ一長一短があり、用途に応じた選択が必要です。最近では、精密な加工が求められる場合に電動式が利用されることが多いです。
最新技術で変わる射出成形の未来
射出成形の未来は最新技術の導入によって大きく変わろうとしています。3Dプリンティング技術の連携により、製品の開発速度やコスト効率が向上し、カスタマイズされた製品の小ロット生産が可能になります。また、セラミックス射出成形技術の導入は、製造業の未来を大きく変える可能性があります。製品品質に影響を与えるデジタルツインや自動化の推進が重要視され、IoTやAIを活用したスマートファクトリーの導入が進んでいます。さらに、高付加価値化の要求に応える技術開発が続けられています。
射出成形を導入する際のリスクと課題
射出成形を導入する際の主なリスクと課題は、材料の無駄、成形不良、初期投資の高さ、および市場投入までの時間プレッシャーです。材料の無駄は、スプルーやランナーなど、製品以外の部分が成形されるため生じます。これに対しては、リサイクルや圧力・速度の最適化などで対策を講じることが重要です。例えば、射出圧力や速度を適切に設定することで、成形不良などのリスクを回避することができます。これらの課題を克服することにより、より効率的な生産体制を築くことが可能です。
射出成形導入時のリスク管理と対策
射出成形を導入する際のリスク管理と対策では、安全性の確保と生産効率の改善が重要です。対策として、射出圧力や速度の調整、金型温度の最適化、冷却時間の延長などが挙げられます。例えば、射出速度を遅くすることで、製品のキャビティに近い部分での成形不良を防ぐことができます。さらに、金型の温度を適切に設定することで、成形品の品質を向上させることが促進されます。これにより、安定した生産環境を確保することが可能です。
よくある課題とその解決策
射出成形におけるよくある課題には、成形不良や材料の過剰使用が含まれます。これに対する解決策としては、金型温度や射出温度を調整し、樹脂の注入を効率的に行うことが挙げられます。具体的には、樹脂の注入位置を厚い部分に直角に射出することで、製品内部への樹脂流入がスムーズになり、成形品質が向上します。これにより、射出成形の効率を高め、歩留まりを向上させることができます。
まとめ
プラスチックの成形方法の中でも、射出成形は非常に一般的で効率的なプロセスです。この技術は、複雑な形状の部品を大量生産できるため、製造業において広く利用されています。材料の無駄を最小限に抑えることができるのも、射出成形の大きなメリットの一つです。
また、射出成形は短時間で高精度の製品を生産することが可能であり、コストパフォーマンスにも優れています。多様な材料を利用できるため、用途に応じた適切な選択が可能で、さまざまな業界でのニーズに応えることができます。この技術を理解することで、製品開発や生産プロセスの最適化に寄与できるでしょう。