【精密板金の基礎知識】これだけは押さえたい技術と工程
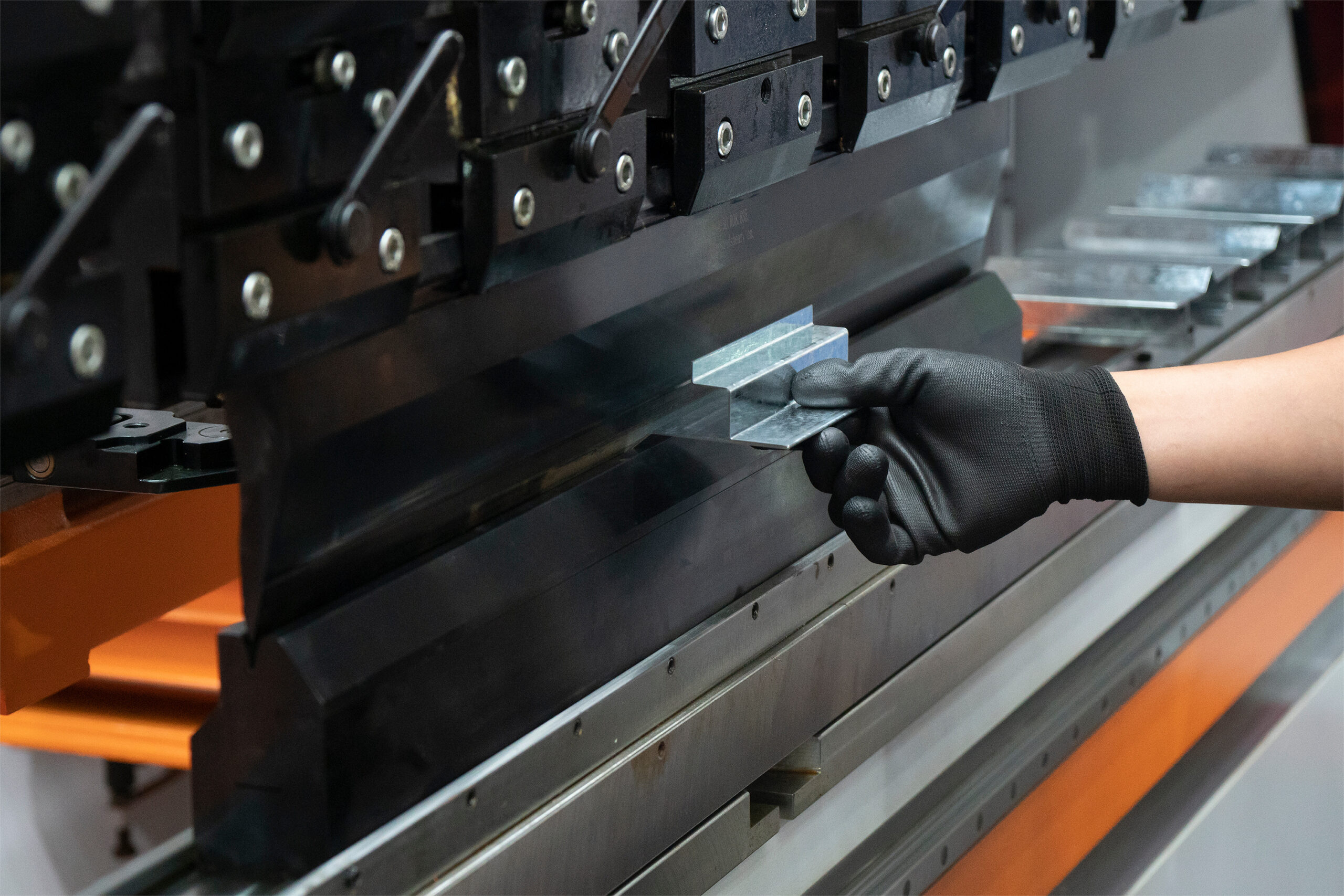
精密な加工技術が求められる現代において、特定の分野での技術力は競争力の源となります。特に、精密な形状や寸法が要求される製品において、板金加工は欠かせない工程です。しかし、その技術や工程について詳しく知っている人は意外と少ないかもしれません。
この記事では、精密板金に関する基本的な知識や、押さえておくべき技術、さらにはその工程について詳しく解説します。どのような材料が使われ、どのように加工が行われるのか、また、その結果どのような製品が生まれるのかを探っていきます。
これからのものづくりにおいて、精密板金はますます重要な役割を果たすでしょう。技術を理解することで、より高品質な製品を生み出すための第一歩を踏み出しましょう。この記事を通じて、精密板金の魅力と奥深さを感じていただければ幸いです。
精密板金と一般的な板金加工の違い
要点として、精密板金と一般的な板金加工の相違点は、精密性や使用材料にあります。精密板金加工は、より薄い板材を使用し高度な精密性を要求される一方、一般的な板金加工は比較的厚い板材を扱い、精度がさほど厳しくありません。理由として、精密板金は医療機器や半導体部品など、精密さが求められる製品に多く用いられるためです。具体例として、精密板金は0.1mm~3mm程度の板厚を使用する一方、一般的な板金加工では1mm~7mm厚の板材を使用します。このように、用途によって精密性や材料が異なる点が、両者の大きな違いといえます。
精密板金加工の特徴とは
精密板金加工の特徴は、非常に高い精度での加工が可能であることにあります。要点として、精密板金加工は複雑な形状の製品にも対応でき、特に小ロットでの生産に向いている点が特徴です。これにより、多様な製品ニーズに対応できるのが大きな利点です。例えば、精密機械や光学機器の部品製造において、その精度の高さは不可欠であり、加工誤差を極力抑えることができます。このような高精度加工によって、競争力のある製品を生み出すことが可能になります。
一般的な板金加工との比較
一般的な板金加工と比較すると、精密板金加工は使用材料や加工精度において大きな違いがあります。一般的な板金加工では主に鉄やステンレスが使用されますが、精密板金ではそれに加えアルミニウムや銅、真鍮など多様な金属を加工することができます。例えば、一般的な板金加工の寸法精度は±0.5~2.0mm程度であるのに対し、精密板金加工では曲げ加工で±0.2mm以下、抜き加工で±0.05mm以下の精度が求められます。こうした精度の違いが、両者の適用範囲を分ける要因となっています。
精密板金加工の具体的な流れと方法
精密板金加工は、最初に設計図を作成し、板金加工の各プロセスを効率的に行う流れを考えます。例えば、金型選定、曲げ加工、抜き加工の順序や回数を工夫し、効率的に製造する方法が必要です。具体的には、展開図を作成し、使用する金型や曲げ加工の角度を決定します。最も一般的な曲げ加工として、金属板を90度や45度に曲げる方法があるため、パンチとダイで金属板を挟み、少しずつV字に曲げていきます。これにより、必要な形状や角度を正確に作り出すことができます。
設計から製造までの工程解説
設計から製造までの工程では、3DプリンターやCADを活用することが重要です。設計段階では、実際の形状や性能を事前に評価するため、3Dプリンターでプロトタイプを作成し、設計図の精度を確認します。これにより、後工程での修正や手戻りを減らすことができます。製造は、量産化に向けた試作を繰り返し行い、検証を重ねて最適化を図ります。このプロセスを経ることで、設計から製造への円滑な移行が可能となります。
使用される技術と機械の紹介
精密板金加工で使用される機械には、NC装置を有する工作機械が一般的です。NC(数値制御)機械は、従来の手作業から解放され、自動で精密な加工が可能です。具体例としてパンチプレスやレーザーカット機があります。これらの機械を使用することで、金属の切断や穴あけを高精度かつ高速で行うことができ、効率的な生産が実現します。AIを活用した画像認識技術も、製品の品質管理に役立っており、不良品の検知に利用されています。
精密板金加工を行う企業の所在地と特徴
精密板金加工は、幅広い工程をカバーする技術力が求められる分野です。多くの企業は、設計から組立まで一貫したサービスを提供しており、顧客の多様なニーズに対応しています。例えば、東京や神奈川、大阪などの都市圏には、24時間稼働を実現し、迅速な納品を心掛ける企業が数多く存在します。具体例として、岡部工業や山崎製作所などが挙げられます。これらの企業は、品質・コスト・納期を重視し、信頼性の高い製品を供給しています。
主要な精密板金加工企業の紹介
精密板金加工においては、多くの企業がそれぞれの強みを活かしています。代表的な企業として、株式会社リ・フォースや竹下工業株式会社があります。これらの企業は最新の設備を導入し、高度な技術を駆使して高品質な製品を提供しています。また、都留製作所やアイザックなども、多様なニーズに応える製品ラインを展開しており、信頼性の高いパートナーとして顧客から選ばれています。こうした企業は、長年にわたる実績と技術力で業界をリードしています。
地域別の企業分布とその強み
精密板金加工企業は、地域ごとに特有の強みを持っています。例えば、関東地方では交通の利便性から迅速な物流対応が可能であり、多くの企業が集積しています。地域内のネットワークを活用し、迅速なサポート体制を整えていることが強みです。関西地方では、製造技術の高さとコスト管理能力に優れる企業が多く、特に大阪や京都に集中しています。さらに、各地域の地元資源を活用し、独自の製品開発力を持つ企業も多いです。これにより、地域ごとの特色が競争力を高めています。
精密板金加工を導入する際のコストと効率性
精密板金加工を導入する際のコストと効率性は、企業戦略において重要な要素とされます。コストに関しては、製品の複雑さや大量生産の有無によって大きく影響されます。理由として、精密板金加工は通常、少量生産の場合でも高いコストパフォーマンスを発揮しますが、大量生産に移行することで一個当たりのコストダウンを図ることが可能です。具体例として、特注品や短納期製品の製作に精密加工技術が活用されています。これにより、コスト効率の高い生産が実現されるのです。
導入にかかる費用の内訳
精密板金加工を導入する際の費用には、様々な要素が含まれます。まず、加工費用に加えて、設計段階での準備費用や、使用する金属の種類、量、さらには作業員の人件費などが挙げられます。理由としてこれらの費用が加工工程において必須であり、全体のコストに大きく影響を与えるからです。例えば、鋼材の価格は1kgあたり数千円とされており、材料費が軽視できない要素であることがわかります。このように、導入時には詳細な費用の内訳を把握し、適切な予算管理を行うことが重要です。
コスト削減と効率化のポイント
精密板金加工においてコスト削減と効率化を図るポイントは、設計段階から最適な加工方法を選択することにあります。理由は、加工方法によっては無駄な材料使用を削減し、効率的な生産を実現できるからです。具体例として、溶接を最小限にし、同じ板厚の材料を使用することで、コストと外観品質を両立できる設計が挙げられます。また、最新技術を導入し、全体の工程を自動化することで、さらにコストを抑えることが可能です。このように、しっかりとした計画と実行により、コスト削減と効率性の向上を図ることができます。
精密板金加工における最新技術とトレンド
近年、精密板金加工業界では、最新技術の進化が注目されています。その中でも特に関心を集めているのが、高精度なコンピュータ制御による板金加工です。これは、CADデータを基に自動的に加工が行われるため、従来の手作業に比べて精度が格段に向上しています。このような技術は、航空宇宙産業だけでなく、自動車産業や電子機器製造においても広く採用されており、業界全体での効率向上と品質向上に寄与しています。こうした傾向は今後も続くと予想され、企業は積極的に最新技術を導入し、業務効率化を図る動きが見られます。
最新の加工技術の概要
精密板金加工における最新技術として、デジタル技術と自動化の融合が進んでいます。特に、CAD/CAMシステムの普及やIoTの活用により、生産工程が一層効率的になっています。具体例として、デジタル化されたデータを基にした加工ラインの自動化が進み、従来では難しかった複雑な加工プロセスが迅速かつ正確に行えるようになりました。このように、高度な技術の導入は、業界全体の生産性を向上させる一方で、新たな市場のニーズに応えるための柔軟な対応を可能にしています。
今後の技術動向とその影響
精密板金加工業界において、今後の技術動向はさらに進化することが期待されています。特に、自動化とデジタルトランスフォーメーションの進展により、生産効率の向上と品質管理の厳密化が実現されています。その具体例として、AI技術を活用したリアルタイムのデータ分析により、精度の高い加工が可能となっています。このような技術の進化は、業界の競争力を高めるだけでなく、環境への配慮や持続可能な製品開発にも寄与しており、今後の市場拡大を支える重要な要素となるでしょう。
まとめ
精密板金は、金属加工の一分野であり、非常に高い精度が求められます。この技術は、設計から製造までの工程が複雑であり、熟練した技術者による慎重な作業が必要です。板金の成形、加工、溶接、仕上げなど、各工程において高い技能が求められます。
特に、精密さが求められる部品や製品を作る際には、各工程での品質管理が重要です。最新の機械やツールを使用することで、加工精度を向上させ、効率的な生産が可能になります。また、技術革新が進む中で、新しい技術や材料の導入も成功の鍵となります。