【無電解ニッケルメッキ】の基本知識、仕組みとメリットを徹底解説
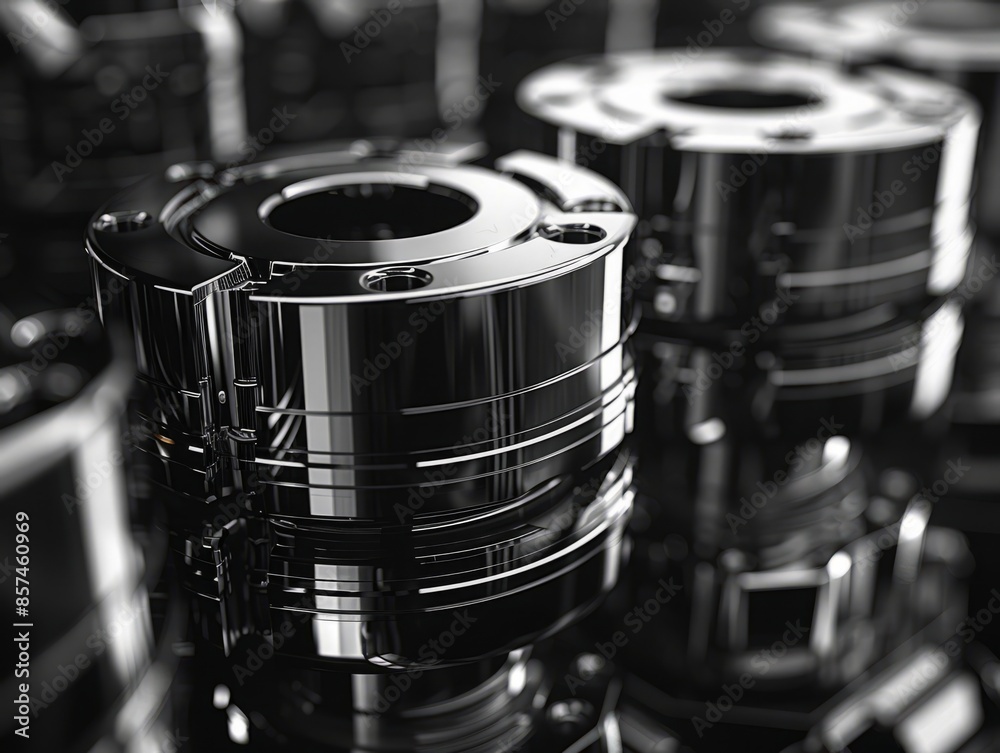
金属の表面処理に関心がある方、または産業界で新たな技術を探求している方にとって、特定のメッキ技術が非常に重要な役割を果たします。特に、耐腐食性や耐摩耗性が求められる場面で、この技術は欠かせません。では、どのようにしてこの技術が機能し、どんな利点があるのでしょうか?この技術を理解することで、さまざまな産業応用が広がり、製品の品質向上やコスト削減につながる可能性があります。
この記事では、メッキ技術の基礎知識から、その仕組み、さらには具体的なメリットに至るまで、幅広く解説します。これからの技術革新を見据え、知識を深める手助けをしてくれる内容となっていますので、ぜひご覧ください。
無電解ニッケルメッキの特性と用途
無電解ニッケルメッキは、電気を使用しないで化学的にニッケルを析出させるメッキ方法で、優れた特性を有します。要点として、電気を使用しないため均一なメッキ厚を実現しやすく、複雑な形状への施工が可能です。例えば、ハードディスクのような精密機器の部品や、電子部品、抵抗体としても使用されています。これらの用途はその耐腐食性、耐摩耗性、電気伝導性に優れていることから多岐にわたります。
無電解ニッケルメッキの基本特性
無電解ニッケルメッキの基本特性は、その高い硬度と耐摩耗性にあります。要点として硬度が高いことで、摩擦に強く耐久性が向上します。リンプ含有率により硬度は変化し、特に熱処理を施すことでさらに硬度が増します。具体例として、これにより自動車部品や工具の耐久性向上に寄与しています。
無電解ニッケルメッキが使用される主な用途
無電解ニッケルメッキは、幅広い用途に使用されています。要点として、耐腐食性が高いため、海洋環境や化学工場などの過酷な環境でも使用されるとされています。具体例として、海底ケーブルのコーティングや、重化学産業のパイプラインなどがあります。このように、過酷な使用条件下でもその性能を発揮するため、活用範囲が広がっています。
無電解ニッケルメッキの処理工程
無電解ニッケルメッキは、アルミニウムやステンレス、銅材に対して、特有の前処理を行うことで密着性の高いメッキ皮膜を作ることが可能です。この工程は、複雑な形状や細かい部品にも対応でき、高品質な仕上がりを実現します。例として、様々な素材に対して、無電解メッキ液を用いた還元反応によってメッキを形成することが挙げられ、このプロセスが優れためっき性能を保証します。
無電解ニッケルメッキの基本的な処理手順
無電解ニッケルメッキの基本的な手順には、脱脂、洗浄、酸処理、メッキ処理、後処理といった工程があります。これらの手順により、メッキの密着性や耐久性が向上します。たとえば、脱脂工程では、表面の油分や汚れを取り除くことで、より適正なメッキ環境を整えます。この一連の流れが、効率的なメッキ処理の基盤となります。
処理工程での注意点と品質管理
無電解ニッケルメッキにおいては、温度、pH、撹拌といった工程条件の管理が重要です。これにより、均一で高品質なメッキが得られます。例えば、温度管理を怠るとメッキ層の不均一が発生しやすくなります。また、品質管理の一環として、メッキの密着性や厚みを定期的に評価することが求められます。これにより、製品の耐久性や性能を確実に確保することができます。
無電解ニッケルメッキの再処理の可否
要点として、無電解ニッケルメッキの再処理は可能です。しかし、その前提として現状のメッキを剥離する必要があります。理由として、メッキをそのまま追加することは技術的に不可能であり、剥離によって表面を再度処理可能な状態に戻す必要があるからです。具体例として、鉄に処理された無電解ニッケルメッキは、まず剥離してから新たにメッキを施すことができるため、再処理が可能です。要点として、この過程では適切な技術と条件が必要となります。
再処理が可能な条件と方法
要点として、無電解ニッケルメッキの再処理を行うには、剥離作業が成功し、素材の状態が良好である必要があります。理由として、剥離によって基材が荒れてしまうと、再度メッキを施す際に問題が発生する可能性があるからです。具体例としては、剥離薬を使用して既存のメッキを除去し、基材を保護しながら再メッキを行います。要点として、正しく剥離し再メッキが行われることで、望ましい表面特性を再現することが可能です。
再処理を行う際の注意点
要点として、無電解ニッケルメッキの再処理では、剥離による基材の損傷を避けることが重要です。理由として、元の表面粗さを維持することが難しい場合があるため、剥離薬の選択や使用法に慎重さが求められます。具体例として、剥離工程に失敗すると、素材表面が荒れて再メッキが困難になることがあります。要点として、慎重な剥離と再処理の条件管理が、再メッキの成功に繋がります。
無電解ニッケルメッキと他のメッキ方法の違い
無電解ニッケルメッキと他のメッキ方法の違いの要点として、電解メッキは電気を流した際の電気分解による金属析出を利用しているのに対し、無電解ニッケルメッキは薬品による化学反応を利用しています。具体的には、無電解ニッケルメッキはメッキ浴内で製品表面に還元反応を生じさせてメッキ皮膜を成長させる方法です。これにより、電気が流れない絶縁体にもメッキが可能です。
電解メッキとの比較
電解メッキとの比較で見ると、電解メッキは電気を使って金属皮膜を形成することで、短時間で処理が可能であり、厚みを調整しやすい反面、均一性に欠ける場合があります。一方で、無電解メッキは化学反応を用いるため、電気が流れない非導電体にもメッキが可能で、高い均一性と密着性を持つ皮膜を形成することができます。そのため、複雑な形状の製品にも適しており、耐食性に優れます。
各メッキ方法のメリットとデメリット
各メッキ方法のメリットとデメリットについて述べると、無電解ニッケルメッキは、均一な膜厚と高度な耐食性、耐摩耗性を持つことが大きなメリットです。導電性が必要ない素材にもメッキが可能ですが、長時間の処理が必要な場合があり、コストが高くなることもあります。一方、電解メッキは比較的低コストで短時間で処理可能というメリットがありますが、膜厚の管理が難しいため、高精度の製品には適さないことがあります。
無電解ニッケルメッキ導入時のコストとリスク
無電解ニッケルメッキの導入時には、主に材料費、設備費、人件費、廃棄物処理費などの様々なコストが関係します。高価な反応液や処理時間の長さがコストを押し上げる要因となりがちです。例として、電解ニッケルメッキと比べると材料コストが高く、処理速度が遅いため、全体的な費用が高くなる傾向があります。しかし、その耐食性や均一性は他の方法にはない強みとされ、使用する環境や目的によってはコストパフォーマンスが見合う場合もあります。したがって、導入の際にはコストを詳細に分析し、リスクを考慮した上で計画を立てることが重要です。
導入にかかるコストの内訳
無電解ニッケルメッキの導入にかかるコストは、主に材料費、設備投資、人件費、廃液処理費などに分類されます。例えば、使用する化学薬品は高価であるため、材料費が高くなります。また、処理設備の維持管理にかかるコストや、品質管理を行うための人件費も大きな割合を占めます。さらに、使用後の液体の廃棄処理は環境規制に従って安全に行われる必要があり、関連するコストが発生します。これらすべての要素を考慮に入れることで、総合的なコスト管理が可能になります。
リスク管理と対策方法
無電解ニッケルメッキの導入に伴うリスクには、膜の剥がれや腐食、処理の不均一性などがあります。これらのリスクを未然に防ぐためには、適切な前処理および後処理を行うことが重要です。例えば、基材の表面を酸洗浄して清浄に保つことで、メッキの密着性を向上させることができます。また、腐食を防ぐために、処理後の保管環境を適切に管理することも必要です。加えて、設備や薬品の扱いに関する定期的な安全教育を行い、作業員の技術向上を図ることがリスク低減に繋がります。こうした対策を講じることで、無電解ニッケルメッキの安全性と品質を高めることが可能です。
まとめ
無電解ニッケルメッキは、特に耐食性や摩耗抵抗性が求められる分野で広く利用されています。このメッキ技術は、電気を使わずにニッケルを基材に沈着させるため、複雑な形状や細かい部品にも均一にメッキが施されるという利点があります。
また、無電解ニッケルメッキは、基材の特性を損なうことなく、優れた硬度と耐腐食性を提供します。そのため、航空宇宙や自動車産業、電子機器など、多様な産業での需要が高まっています。技術の進化により、さらなる性能向上が期待されており、今後の展開にも注目が集まります。