【工程】を知ることでわかるマシニング加工の【メリット】と【デメリット】
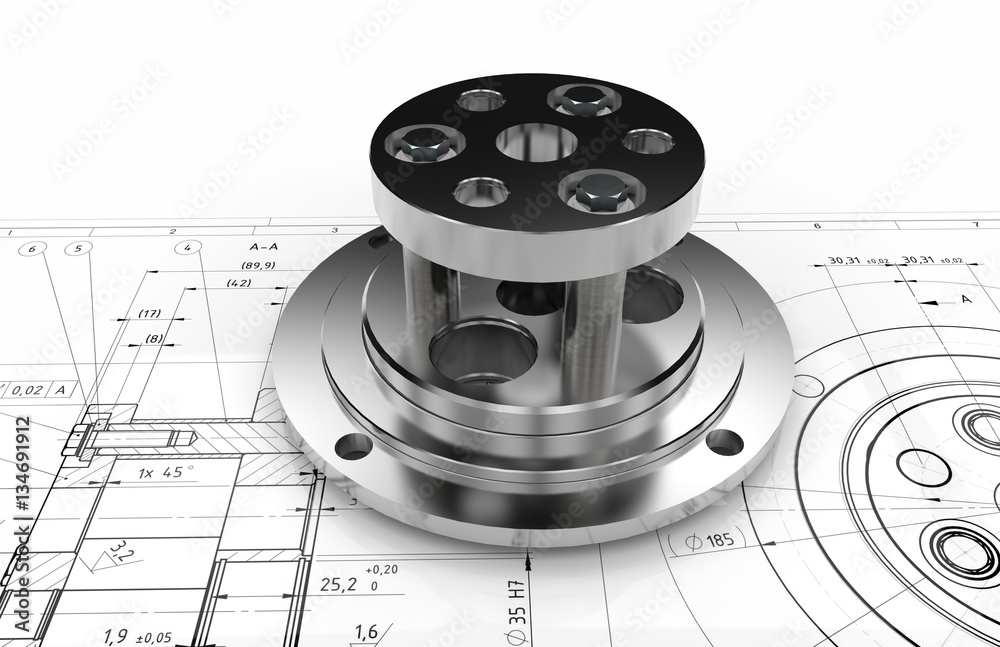
マシニング加工は、現代の製造業において欠かせない技術の一つです。複雑な形状を精密に加工するこの工程は、様々な産業で広く利用されていますが、その特性や利点、さらには注意すべき点も存在します。この記事では、マシニング加工の基本的な特徴や工程について詳しく解説し、そのメリットとデメリットを明らかにします。これを読むことで、あなたがこの技術をどのように活用できるか、新たな視点を得ることができるでしょう。
もし、製造プロセスを見直したい、または新たな技術導入を検討しているなら、マシニング加工の理解は非常に重要です。具体的な工程やその効率的な使い方を知ることで、より高品質な製品をより迅速に生産できるようになります。この記事を通じて、マシニング加工の全貌を掴み、あなたのビジネスにおける競争力を高める手助けをいたします。
マシニング加工の基本とその特徴
マシニング加工は、金属やプラスチックなどの素材を削り出して形状を作る加工法で、主な特徴は高精度で複雑な形状を実現できることです。加工工程は、設計データに基づいたプログラムを機械に入力し、CNC(コンピュータ数値制御)を利用して自動的に切削を行います。具体例として、金型や自動車部品の製造に広く利用されています。また、フライス加工の一種と考えることもでき、工具が高速で回転し、素材を削り取って目的の形状にします。要するに、マシニング加工は複雑な形状を高精度で仕上げるための重要な方法と言えるでしょう。
マシニング加工とは何か?基本を理解する
マシニング加工とは、NC(数値制御)装置を備えたフライス加工機で行う高度な切削加工を指し、特に「マシニングセンタ」を使用するケースが一般的です。この機械を使用することで、素材を固定し、刃物を回転させ加工する作業機械加工となります。具体例として、ドリルを使って穴を開けたり、エンドミルなどの回転工具で素材を削ったりするものがあります。要点として、マシニング加工は自動化された切削加工として非常に有用であり、多機能な工作機械を利用した加工と言えます。
マシニング加工の特徴と他の切削加工との違い
マシニング加工は、多くの製品加工に採用されている高い汎用性を持つ方法ですが、適した素材と不適な素材が存在します。特徴として、平面の切削、穴あけ、溝加工など、形状の自由度が高い点が挙げられます。他の切削加工との違いは、加工工具が回転して、材料をあらゆる方向から削る機械であることです。具体例として、旋盤とマシニングセンタを比較すると、前者はワークが回転する仕組みであるのに対し、後者は工具が回転する仕組みであることが主な相違点です。要するに、マシニング加工は高度な切削加工法として、設計図面と比較しながら加工を行えるのが特徴です。
マシニング加工の工程を詳しく解説
マシニング加工では、切削工具を高速で回転させることにより材料を削り取り、目的の形状に仕上げます。この加工はコンピュータ制御の下で行われ、設計から実際の加工までがシームレスに進みます。具体的な工程としては、まず設計・プログラミングを行い、その後素材の準備、段取り、切削加工、検査へと進みます。これにより、複雑な形状の部品でも高い精度で製造が可能です。
マシニング加工の具体的な工程ステップ
マシニング加工の主なステップには、プログラムの作成、素材の準備、実際の加工、最終検査があります。プログラムの作成では、コンピュータを用いて加工内容を指示するための指示を作成します。その後、素材が正しく設置されていることを確認し、加工機械を動作させます。最終的に、製品が指示通りに仕上がっているかを検査し、必要に応じて修正を行います。
各工程で使用される機械とその特徴
マシニング加工には多様な機械が使用され、各工程で適切な機械選択が求められます。例えば、切削加工にはフライス盤や旋盤が一般的に使用され、これらは高精度な加工を可能とする特性を持ちます。フライス盤は特に複雑な形状を高精度で作成するのに優れています。各機械の特性を理解し、適切に活用することで、効率的な生産が実現します。
マシニングセンタの種類とその利点・欠点
マシニングセンタは、立型、横型、門型、5軸制御など、さまざまな種類が存在します。これらの種類により、それぞれ異なる利点と欠点があります。例えば、立型マシニングセンタは垂直方向の加工が得意で、視認性が高いことが利点ですが、大きなワークには不向きです。横型は大きなワークの連続加工に適していますが、設備のコストがかかることが欠点です。門型は大型の複雑な構造や部品に適しており、5軸制御は多軸制御により複雑な加工が可能ですが、プログラムの設定が難しく、操作が複雑です。これらの利点と欠点を理解することで、適切なマシニングセンタを選定し、生産効率を向上させることができます。
異なるマシニングセンタの種類を解説
マシニングセンタは、主に加工の形態や軸の数により、いくつかの種類に分類されます。立型マシニングセンタは、主軸が垂直に設置され、上から材料を加工するスタイルで、設計図面を見比べながら加工を進めやすいのが特徴です。横型マシニングセンタは、主軸が水平に配置されており、重い材料をしっかり固定して加工することが可能です。門型マシニングセンタは、大規模な部品の加工に用いられることが多く、広い作業スペースを必要とします。さらに、5軸制御マシニングセンタは、複雑な形状の加工を可能にし、需要が高まっています。それぞれの特性に応じて使用することで、製造業の効率を大幅に向上することができます。
各マシニングセンタの利点と欠点を比較
マシニングセンタの利点と欠点を比較することで、最適な選定が可能です。立型マシニングセンタは、視認性が高いという利点がありますが、大型のワークには適しません。横型マシニングセンタは、大量生産や連続加工に最適である一方、導入コストが高いことがデメリットです。門型マシニングセンタは大規模な加工が可能でありながら、設置スペースを取るため、場所が限られます。5軸制御マシニングセンタは、複雑な形状の加工を一度に行えるため効率的ですが、その分操作スキルが要求されます。これらの特徴を理解し、適切なマシニングセンタを選ぶことが重要です。
マシニング加工の導入におけるコストと技術的ハードル
マシニング加工の導入には、初期コストと技術的ハードルが大きな課題となります。これらの要点として、マシニングセンタの購入や運用にかかる高額な設備投資が挙げられます。特に、初期の導入時には数百万円から数千万円が必要となり、さらにCAD/CAMソフトや治具のコストも計上されます。このようなコストがあるため、導入にあたっては慎重な検討が必要です。
マシニング加工を導入する際のコスト分析
導入コストを考慮する際、高精度なマシニング加工を行うには一定のコストが伴います。例えば、マシニングセンタ本体は高価であり、CAD/CAMソフトのライセンス費用、必要な治具やツール類の購入も考慮する必要があります。企業は生産効率や製品品質の向上を通じて、これらの初期コストを回収し、長期的なコスト削減を目指します。具体例として、生産量を増やすことでコストのバランスをとる方法が挙げられます。
技術的ハードルとその克服方法
技術的ハードルには、操作スキルの習得や複雑な設計への対応が含まれます。克服するためには、デジタルトランスフォーメーションの活用が鍵となります。デジタル技術を活用することで、設計段階の効率化や精度の向上が可能となり、技術的な課題を軽減できます。具体的な例としては、CAD/CAMの自動化やAIによる加工条件の最適化が挙げられます。これにより、複雑な加工も高精度に対応できるようになります。
マシニング加工を製造プロセスに活用する方法
マシニング加工は、その高精度と効率性から製造プロセスにおいて重要な役割を果たします。要点として、製造プロセス全体の合理化が挙げられます。理由として、マシニング加工ではCAD/CAMソフトウェアを使用して設計図を元に加工プログラムを作成し、CNC(コンピュータ数値制御)を用いて自動化された高精度加工を実現することができるためです。具体例として、航空機や自動車の精密部品の製造において、マシニング加工が従来の手作業に比べて大幅に効率を改善したケースが報告されています。このように、マシニング加工は製造プロセスを最適化するために欠かせない技術です。
マシニング加工の活用事例とその効果
マシニング加工はさまざまな分野での革新的な部品製作に貢献しています。要点として、加工の多様性と効率性が挙げられます。理由は、5軸マシニングセンタを戦略的に活用することで、複雑な形状の部品を短期間で高精度に製作できるためです。具体例として、航空機部品の製造では、マシニング加工により加工時間を大幅に短縮し、トータルコストを削減する効果が確認されています。これにより、製造現場における生産性と競争力が向上します。
製造プロセスにおけるマシニング加工のメリットとデメリット
マシニング加工の最大のメリットは、高精度と生産性の両立が可能であることです。要点として、高精度加工と量産性の高さが挙げられます。理由は、CAD/CAMによる設計と数値制御による自動加工により、μmオーダーの非常に高い精度を実現できるためです。具体例としては、医療機器や自動車部品など、特に高精度が求められる分野での使用が一般的です。しかし、デメリットとしては、工具の磨耗が発生するため、厚みがあるワークの加工には限界があることが挙げられます。このように、メリットとデメリットを理解し、適切に活用することが重要です。
まとめ
マシニング加工は、精密な部品を製造するための重要なプロセスであり、高い精度と再現性が求められます。加工工程は主に切削、研削、穴あけなどから成り立っており、これらの工程を駆使することで多様な形状や機能を持つ部品を実現できます。
この加工方法には、複雑な形状を一度の工程で製造できるメリットがありますが、一方で、初期投資や運用コストが高くなるデメリットも存在します。また、材料の特性や加工条件によって仕上がりが変わるため、経験に基づいた適切な知識が必要です。全体を理解することで、より効果的な加工が可能になります。